转向传动轴检测的重要性与技术要点
转向传动轴作为汽车动力传递的核心组件,承担着连接变速箱与驱动轮、实现动力高效传递的关键作用。其工作状态直接影响车辆操控性、行驶安全性及动力传输效率。在长期使用中,传动轴可能因金属疲劳、机械磨损或外力冲击产生变形、裂纹等隐患,专业检测可有效预防突发性故障,避免因传动失效导致的转向失控、动力中断等严重事故。根据JIS D0105标准要求,每行驶3万公里或发生碰撞后必须实施系统检测。
核心检测项目及实施规范
1. 外观完整性检测
使用10倍放大镜配合工业内窥镜进行360°表面扫描,重点检查焊接部位、花键连接处是否存在≥0.2mm的裂纹。通过三维坐标测量仪检测轴体直线度,允许挠曲量应≤0.15mm/m。锈蚀面积超过总表面积5%或存在深度>0.5mm的蚀坑需判定为失效。
2. 动平衡测试
在专用动平衡机上以额定转速的120%进行测试,不平衡量应控制在10g·cm以内。检测时需模拟实际工况安装万向节,使用激光传感器测量振幅,振动速度值不应超过4.5mm/s(ISO 10816标准)。超标时需通过配重块调整,单次配重不超过3处。
3. 万向节配合间隙检测
使用数显扭力扳手测量十字轴轴向间隙,新品应<0.05mm,维修极限为0.15mm。滚针轴承径向游隙采用气动量仪检测,允许范围为0.02-0.08mm。超过标准值会导致异常噪音并加速磨损,需立即更换总成。
4. 花键配合检测
使用花键综合检测仪测量齿侧间隙,正常配合间隙为0.1-0.3mm。配合松旷超过0.5mm时,会产生明显冲击异响。同时检查花键齿顶磨损量,当齿厚减少量>15%原始尺寸时,必须更换传动轴总成。
5. 材料性能验证
采用超声波测厚仪检测管壁厚度均匀性,同一截面最大厚度差应<0.2mm。对可疑部位进行硬度测试(HRC28-32),洛氏硬度偏差超过3个单位表明存在热处理缺陷。必要时取样进行金相分析,确认材料晶粒度达到ASTM 6级以上标准。
6. 动态负载测试
在液压疲劳试验台上模拟实际工况,施加交变扭矩至额定值的150%。连续运行50万次循环后,检查传动轴是否出现塑性变形或微观裂纹。同时监测运行时的NVH特性,振动加速度峰值应控制在0.6g以内。
检测结果分析与处置建议
检测数据需录入专业MES系统进行趋势分析,建立零部件全生命周期档案。对存在轻微变形的传动轴可采用液压校正工艺修复(最大校正量不超过轴径的3%),校正后需重新进行动平衡测试。当检测发现2项以上关键参数超标时,建议直接更换原厂配件,确保行车安全。
通过系统化的检测流程,可提前发现95%以上的潜在故障。建议配合车载OBD系统进行实时监测,当监测到传动系统振动异常或扭矩波动时,及时触发预警提示,构建主动式安全保障体系。
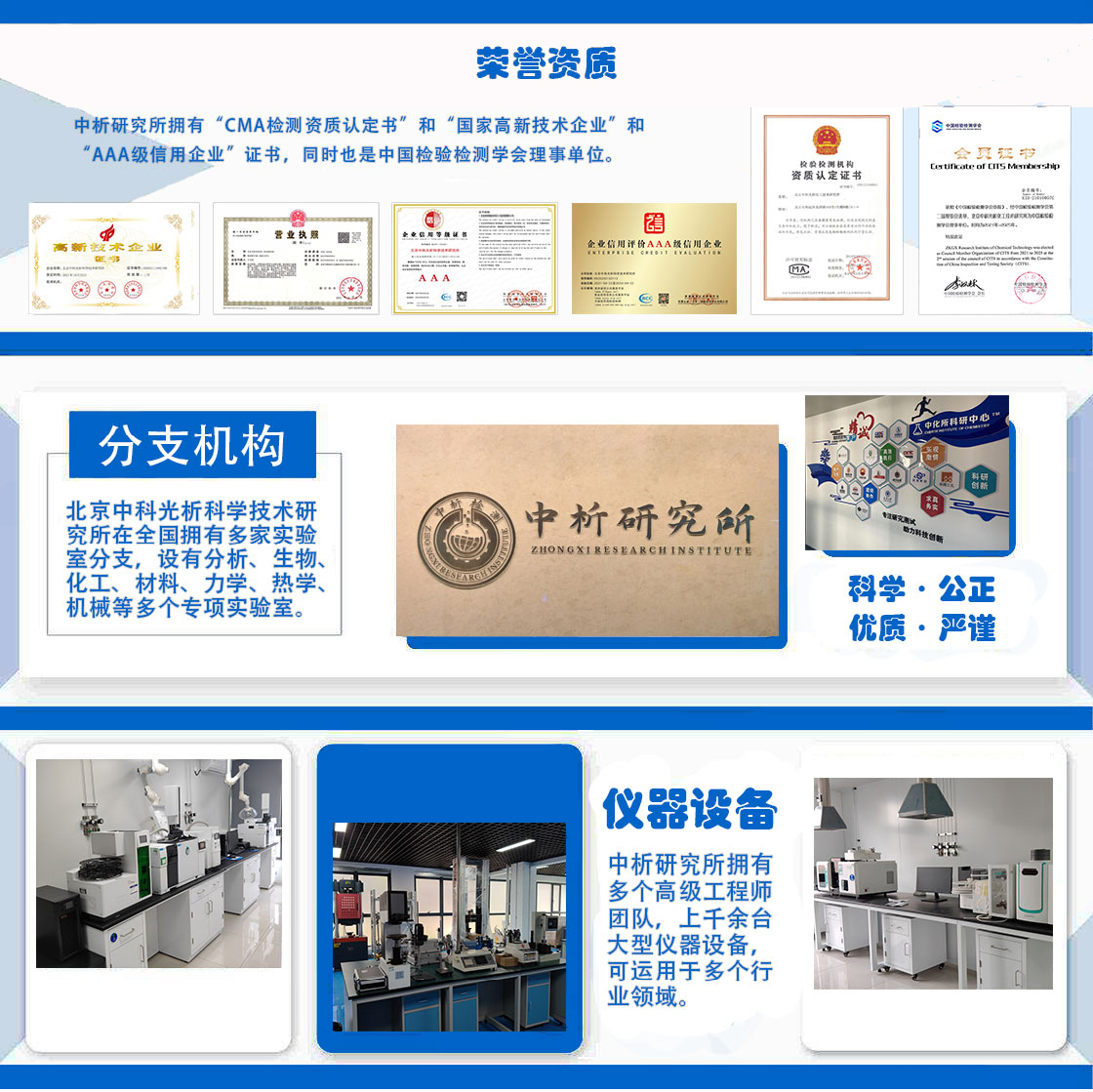
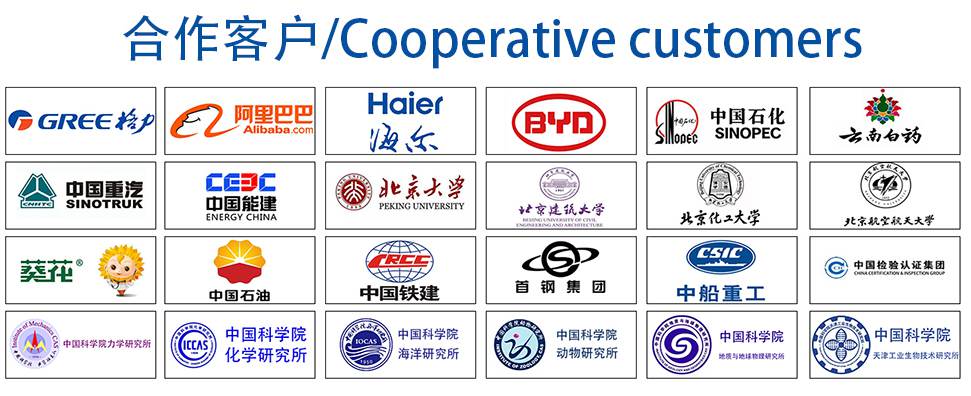