钛和钛合金化学成分检测技术发展与应用白皮书
随着航空航天、医疗器械及海洋工程领域对高性能材料需求的激增,钛及钛合金凭借其高强度、低密度和优异的耐腐蚀性,已成为21世纪战略性关键材料。据材料检测联盟(GMTA)2024年报告显示,钛合金市场规模预计以8.3%年复合增长率持续扩张,至2028年将突破256亿美元。在此背景下,精准的化学成分检测成为保障材料性能的核心环节,直接影响航空发动机叶片抗蠕变能力、骨科植入物生物相容性等关键指标。通过建立标准化的钛合金多元素检测体系,不仅能实现材料全生命周期质量追溯,更能为新型钛基复合材料研发提供数据支撑,其核心价值体现在技术壁垒突破、产业链协同优化及国际标准话语权提升三大维度。
多元光谱联用技术原理与创新
现代钛合金化学成分检测主要依托X射线荧光光谱(XRF)、电感耦合等离子体质谱(ICP-MS)及光电直读光谱(OES)技术联用体系。其中,XRF技术可实现钛基体中铝、钒等主量元素的快速筛查,检测精度可达±0.02wt%;而ICP-MS对锆、钼等痕量杂质元素的检出限可低至0.001ppm,有效满足航空级TA18钛合金的洁净度要求。值得关注的是,基于激光诱导击穿光谱(LIBS)的在线检测系统已实现0.3秒/点的实时分析能力,为钛板轧制过程的成分闭环控制提供了技术支撑。
全流程标准化检测实施体系
在具体实施层面,检测流程严格遵循ASTM E2371及ISO 17294标准,涵盖样品制备、仪器校准、数据解析三大阶段。以航空紧固件用TC4钛合金检测为例,需先采用数控线切割获取10×10mm标准试样,经真空镶嵌后使用金刚石悬浮液抛光至Ra≤0.05μm。检测过程中采用三级校准策略:首先使用NIST SRM 652标准物质建立工作曲线,再通过基体匹配法消除钛元素对钒谱线的干扰,最终应用蒙特卡洛算法进行不确定度评估。该体系下,主要元素检测相对标准偏差(RSD)可控制在0.5%以内。
行业应用场景与质量保障实践
在医疗植入物领域,TOP5骨科器械制造商均已将钛合金微量元素分析技术纳入供应商准入体系。美敦力公司2023年质量报告显示,通过实施钼、镍等22种杂质元素的批检制度,其人工关节产品临床不良率下降37%。海洋工程领域,中国船舶重工集团采用LIBS-OES联用方案,成功将深海探测装备用钛合金管件的检测周期从72小时压缩至8小时,同时使氧元素检测准确度提升至99.2%。质量保障方面,实验室需每季度参与ILAC-MRA国际比对,并建立区块链赋能的检测数据存证系统,确保结果不可篡改且全程可追溯。
智能化升级与行业生态构建
行业领先机构正通过构建数字化检测生态实现技术跃迁。宝钛股份联合清华大学开发的AI辅助判读系统,可使光谱干扰峰识别准确率达到98.7%,较传统人工判读效率提升12倍。同时,基于工业互联网的分布式检测网络已在国内形成,如长三角钛合金检测共享平台整合了9个城市23台ICP-MS设备资源,实现检测产能动态调配与区域协同。据中国航发研究院测算,此类智能化改造可使单件检测成本降低42%,同时支撑钛合金3D打印材料研发周期缩短30%。
面向未来,建议从三方面深化行业布局:首先加快制定钛基复合材料专用检测标准,攻克碳化钛增强相定量分析技术瓶颈;其次推动微型化光谱设备研发,拓展在役设备现场检测场景;最后构建产学研用协同创新机制,依托国家新材料测试评价平台开展跨国实验室能力验证。唯有通过技术迭代与生态重构,才能为钛合金在第六代航空发动机、深海空间站等重大工程中的规模化应用提供坚实保障。
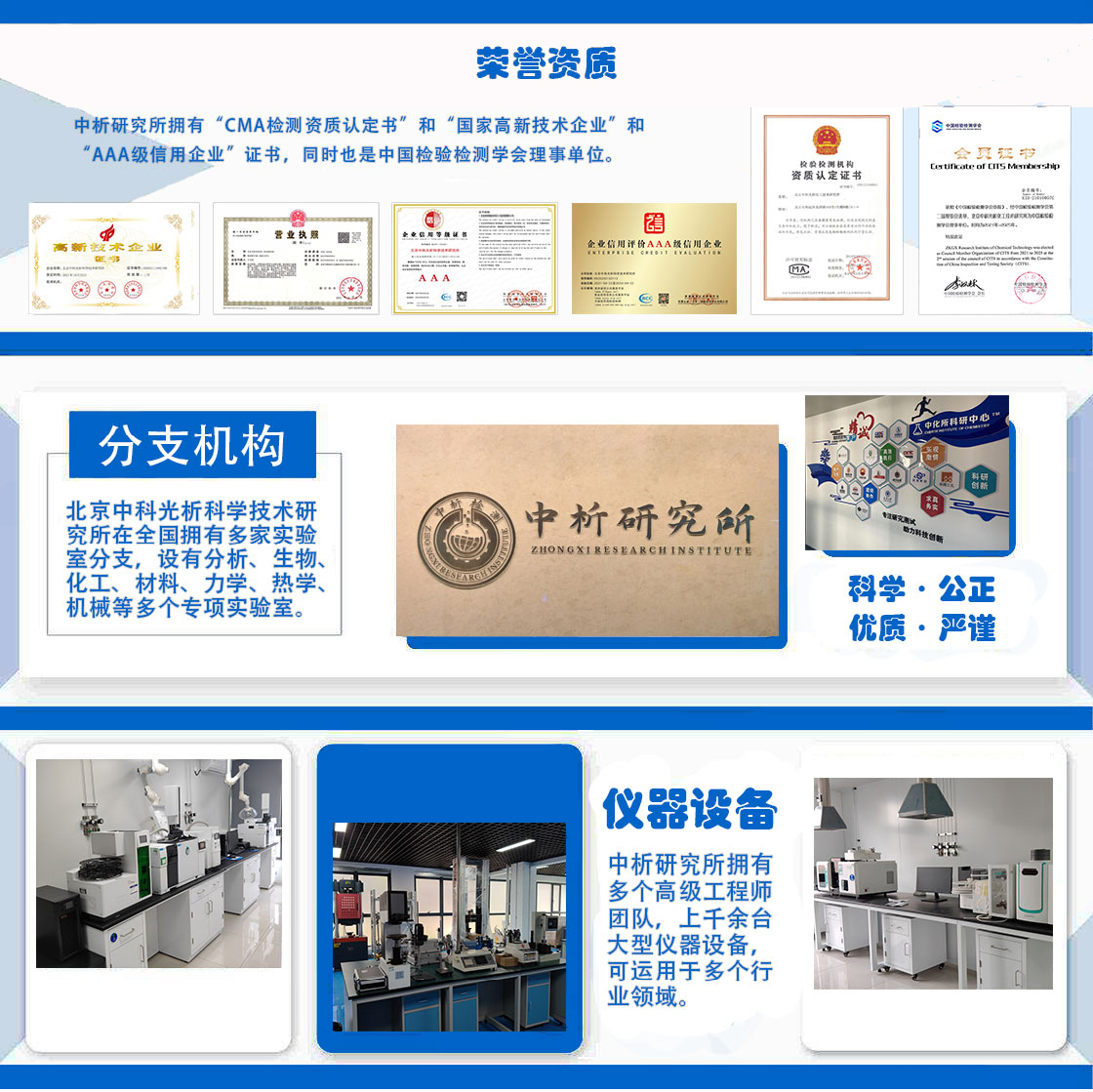
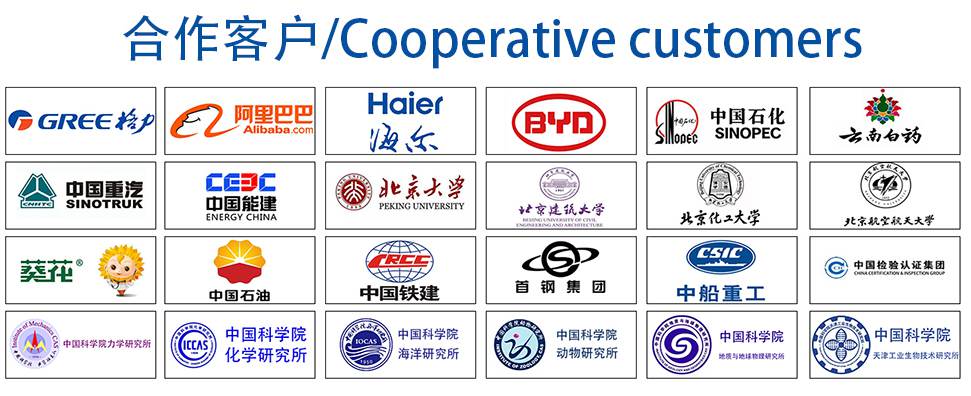