热安定性检测:关键检测项目与意义
一、热安定性检测的核心项目
1. 分解温度测试
- 定义:材料在加热过程中开始发生化学分解的温度。
- 检测方法:
- 热重分析法(TGA):通过监测材料质量随温度升高的变化,确定分解起始温度(T<sub>onset</sub>)和最大分解速率温度(T<sub>max</sub>)。
- 差示扫描量热法(DSC):检测材料分解时的吸热或放热峰,辅助判断分解温度。
- 适用对象:高分子材料(如塑料、橡胶)、药物活性成分、电池材料等。
- 标准参考:ASTM E1131, ISO 11358.
2. 氧化稳定性测试
- 定义:材料在高温和氧气环境中抵抗氧化降解的能力。
- 检测方法:
- 氧化诱导期(OIT)测试:通过DSC或专用氧化仪测定材料在氧气氛围中开始氧化反应的时间。
- Rancimat法:用于油脂或食品,通过检测导电性变化判断氧化稳定性。
- 适用对象:润滑油、塑料(如PE、PP)、生物柴油、食品油脂等。
- 标准参考:ASTM D3895, ISO 11357-6.
3. 热失重率(TG%)分析
- 定义:材料在一定温度和时间内的质量损失百分比,反映其挥发性成分或分解程度。
- 检测方法:TGA在恒温或程序升温条件下测定失重曲线。
- 应用场景:
- 评估聚合物中添加剂(如增塑剂)的挥发性;
- 分析电池材料的热稳定性(如电解液蒸发)。
- 标准参考:GB/T 17391, ISO 247-2.
4. 热分解产物分析
- 定义:通过检测材料热分解产生的气体或残留物,评估其热降解机制和安全性。
- 检测方法:
- 热重-红外联用(TGA-FTIR):分析分解气体的化学成分。
- 热裂解-气相色谱/质谱(Py-GC/MS):鉴定分解产物的分子结构。
- 应用场景:阻燃材料评估、药物杂质分析、电子元件失效分析。
5. 动态热稳定性测试
- 定义:模拟材料在循环温度变化下的稳定性。
- 检测方法:将样品置于高低温循环箱中,通过多次升降温循环后测试其性能变化(如力学强度、颜色)。
- 适用对象:涂层材料、电子封装材料、汽车部件等。
6. 熔融稳定性测试
- 定义:评估材料在熔融状态下(如加工温度)的化学稳定性。
- 检测方法:通过熔融指数仪(MFR/MVR)测定材料多次熔融后的流动性变化。
- 应用场景:塑料加工(如注塑、挤出)中材料的热降解控制。
二、行业应用案例
- 高分子材料:检测塑料(如PVC)的分解温度,避免加工过程中释放有毒气体(如HCl)。
- 石油化工:评估润滑油的高温氧化稳定性,延长发动机使用寿命。
- 药品:确定药物活性成分的热分解特性,优化储存条件(如是否需要避光、低温保存)。
- 食品工业:测试食用油脂的氧化诱导期,预测货架期。
- 新能源:分析锂离子电池电解液的热稳定性,防止热失控引发爆炸。
三、检测项目选择的关键因素
- 材料类型:高分子材料侧重分解温度和熔融稳定性,金属材料关注氧化和蠕变性能。
- 使用环境:高温长期使用需测试氧化稳定性;短期高温冲击需动态循环测试。
- 法规要求:不同行业(如食品、医药)对热安定性的检测标准有明确限定。
四、总结
上一篇:矿用带式输送机橡胶缓冲托辊安全性检测下一篇:矿用织物整芯阻燃输送带检测
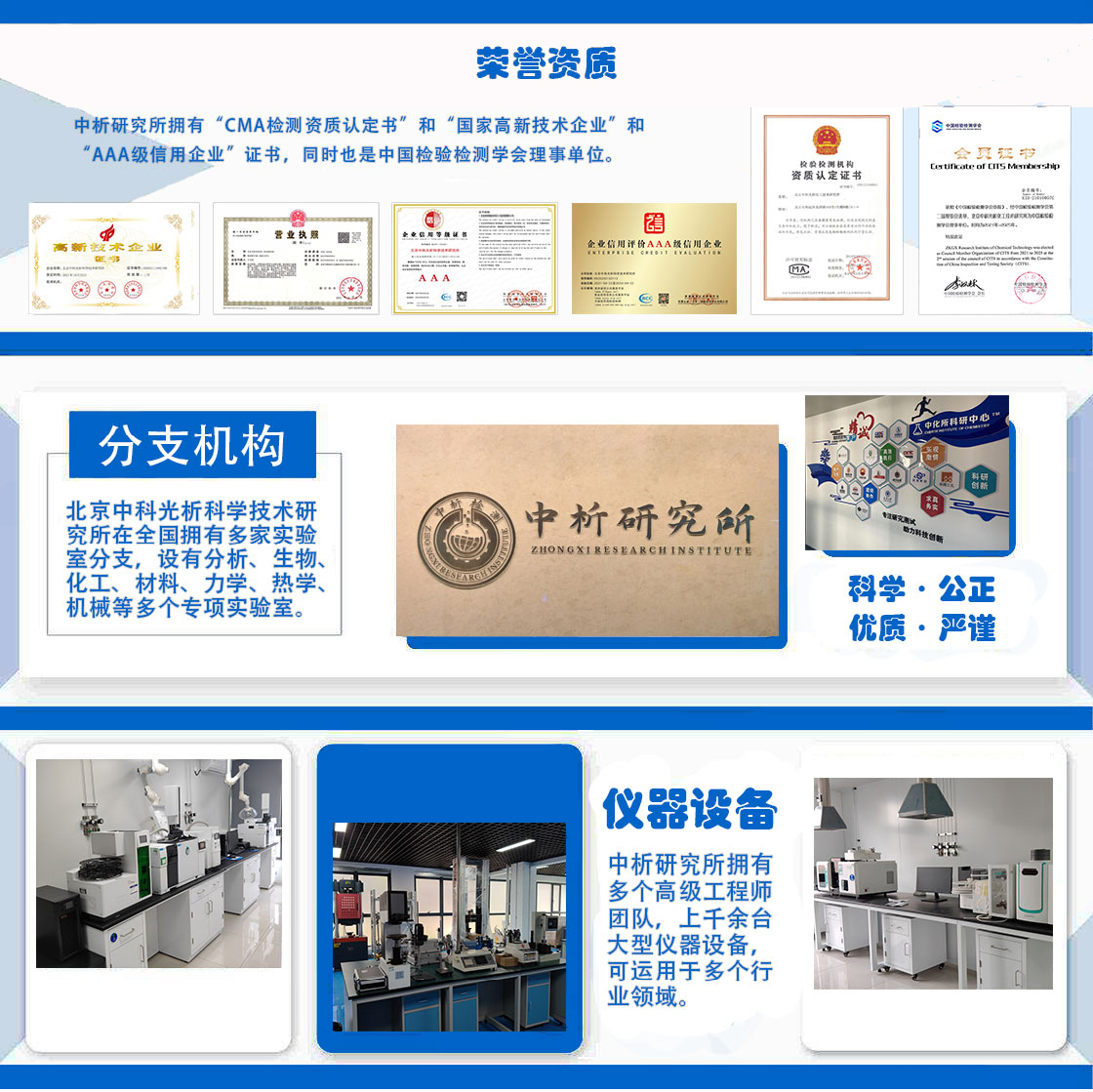
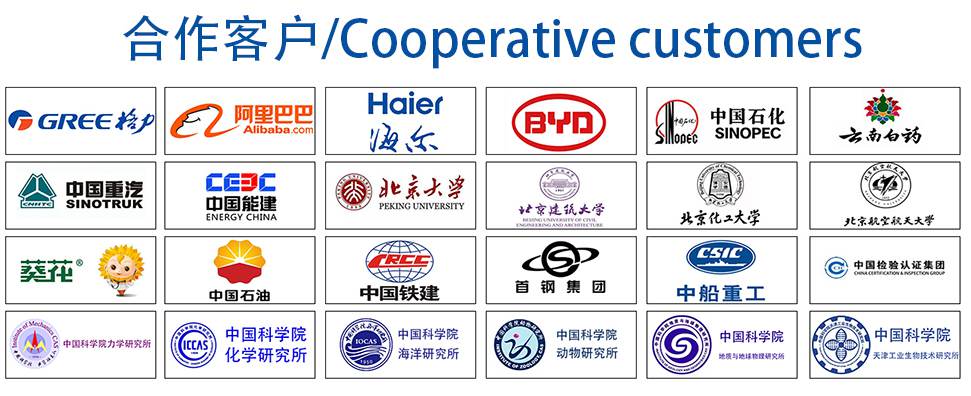
材料实验室
热门检测
270
227
202
211
210
213
225
218
228
229
213
213
218
216
210
204
221
207
220
214
推荐检测
联系电话
400-635-0567