硬质合金孔隙度和非化合碳检测
硬质合金孔隙度和非化合碳检测的重要性
硬质合金是一种由金属碳化物(如碳化钨)和金属粘结剂(如钴或镍)组成的复合材料。由于其优越的耐磨性、高硬度和良好的抗腐蚀性能,硬质合金被广泛应用于切削工具、耐磨部件及其他机械零件的制造。然而,为了确保产品的质量和性能,检测硬质合金的孔隙度和非化合碳含量至关重要。
硬质合金孔隙度的影响及检测
孔隙度是指材料内部孔洞的体积分数,它是评估硬质合金质量的重要指标之一。理想的硬质合金应该有较少的孔隙,因为过高的孔隙度会降低材料的强度和韧性,导致工具易碎,影响使用寿命。此外,孔隙会成为潜在的裂纹扩展路径,加速材料的疲劳失效。
检测孔隙度的方法有多种,其中一种常用的是金相显微镜分析。制备好的硬质合金样品经过抛光和腐蚀处理后,可在显微镜下观察其微观结构,评估其中的孔隙率。此外,还可以利用计算机断层扫描(CT)技术进行无损检测,通过三维成像技术全面地分析材料内部的孔隙分布。显微硬度测试也可以用于评估孔隙对材料性能的影响。
非化合碳及其检测
非化合碳是指在硬质合金中存在的未与金属元素结合的碳元素。其存在会导致晶界脆化,使材料变得脆弱。此外,多余的非化合碳还可能造成脱碳现象,进一步影响硬质合金的机械性能和耐磨性。
检测非化合碳含量的关键在于利用化学和物理分析方法。其中,电弧红外吸收法被广泛应用,它利用高温下碳元素释放的气体通过红外光谱检测进行定量分析。此外,X射线光电子能谱(XPS)技术也可用于分析非化合碳的化学状态和含量,通过能谱分析图谱确定碳元素的存在形式和浓度。
优化硬质合金性能的策略
提高硬质合金性能的关键在于降低孔隙度和控制非化合碳含量。为此,制造过程中应严格控制粉末的粒度分布和混合均匀性,确保在烧结过程中理想的致密度。此外,优化烧结参数,如温度和时间,能有效减少孔隙的形成,确保材料的均匀性和致密度。
非化合碳的含量可以通过调整原料成分和合理的烧结气氛加以控制。例如,提高粘结剂质量,确保它能充分润湿和覆盖碳化物颗粒,以减少自由碳的生成。另外,在烧结过程中使用碳势控制或真空脱碳技术也有助于降低非化合碳的含量。
结论
硬质合金的孔隙度和非化合碳含量是影响其性能的关键因素。通过多种检测手段对其进行严格监控,可以显著提高产品质量和可靠性。结合齐全的制备技术和工艺优化策略,不仅能够生产出性能优异的硬质合金材料,还能延长其使用寿命,扩大其应用领域。未来的研究计划可以进一步探索细化的控制技术和新型工具,以更高的精准度提升硬质合金的质量,满足不断增长的工业需求。
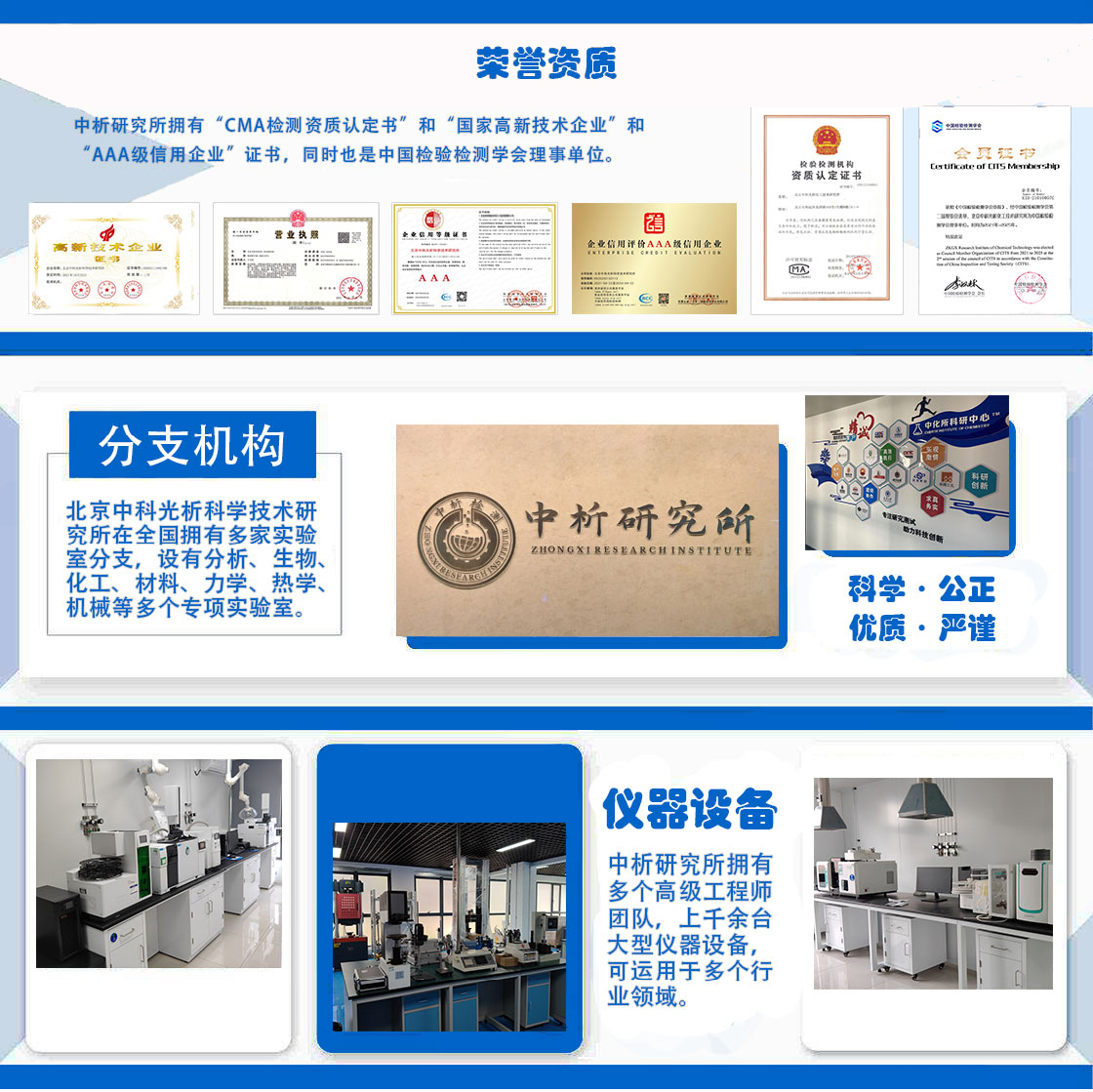
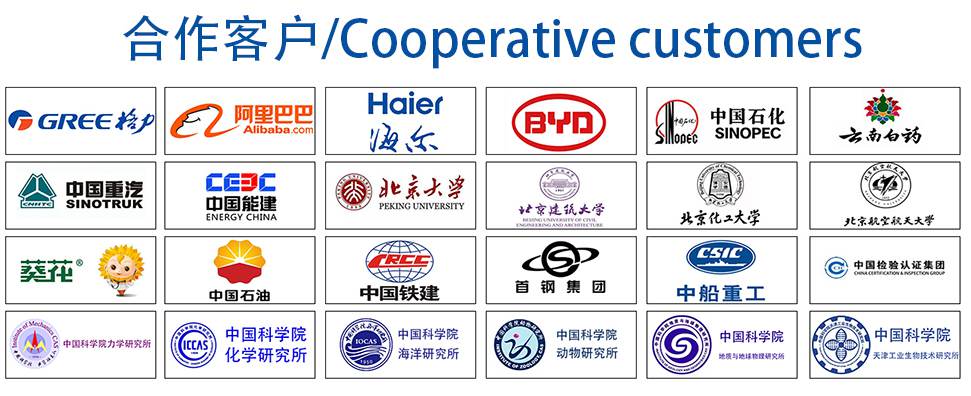