硬质合金晶粒尺寸检测
硬质合金晶粒尺寸检测的重要性
硬质合金作为一种优异的材料,因其高硬度和耐磨损性能广泛应用于切削工具、模具和耐磨零件的制造中。硬质合金的性能在很大程度上取决于其微观结构,特别是晶粒尺寸。因此,晶粒尺寸的检测对于保证硬质合金质量和优化生产工艺至关重要。
硬质合金晶粒的特性
硬质合金通常由碳化钨(WC)颗粒通过粉末冶金工艺和金属粘结剂(如钴)烧结而成。碳化钨颗粒的晶粒尺寸对材料的力学性能有显著影响。通常,细小的晶粒提供更高的硬度和强度,而较大的晶粒能够提供更好的韧性。因此,不同应用可能需要不同的晶粒尺寸优化方案。
常用的硬质合金晶粒尺寸检测方法
光学显微镜法
光学显微镜法是一种直接观察并评估晶粒尺寸的常见方法。样品经过加工和抛光后,用化学试剂腐蚀表面以显现晶粒边界。光学显微镜由于操作简单且成本相对较低,通常被用作初步的分析工具。然而,其分辨率有限,无法有效识别非常细小的晶粒。
扫描电子显微镜(SEM)
扫描电子显微镜可以提供更高的分辨率和更详细的表面结构信息。在SEM下,电子束扫描样品表面并产生高分辨率的图像。这种方法可以识别微米甚至纳米级的晶粒尺寸,同时还能获取表面形貌和元素组成信息。但是,其设备复杂且操作成本较高。
X射线衍射法(XRD)
X射线衍射法通过测量晶格间距的变化来推断晶粒尺寸。虽然这是一种间接测量方法,但对于大批量生产的晶粒尺寸分析以及粉末形式的材料非常有效。X射线衍射能够提供晶粒尺寸的统计分布信息,但通常需要结合其他方法进行综合分析。
影响晶粒尺寸检测的因素
影响晶粒尺寸检测精度的因素有很多。首先,样品的制备方法非常重要,样品的切割、嵌入和抛光等前处理步骤必须严格控制,以避免对晶粒的破坏。其次,选择合适的检测方法和设备也至关重要,不同检测技术可能对样品的要求和分析结果有较大差别。此外,操作人员的经验和技能也会对最终结果产生影响,尤其是在分析图像或解释数据时。
硬质合金晶粒尺寸检测的技术进展
随着检测技术的不断进步,新型的检测方法和设备不断被开发出来,为更精确、快速地获得晶粒尺寸信息提供了可能性。例如,数字图像处理技术可以结合显微镜图像进行自动化分析,从而减少人为误差。此外,三维结构分析技术也在不断发展,如聚焦离子束-扫描电子显微镜(FIB-SEM)系统,可以三维重建样品结构,提供更加全面的微观信息。
展望与挑战
随着制造业对材料性能需求的不断提高,硬质合金中的晶粒尺寸及其分布了解及控制将变得越来越重要。未来的发展方向可能包括提高检测技术的灵敏度和精度,实现更快速的在线检测以及开发更加智能的分析软件。面对挑战,需要材料学家、工程师和设备制造商共同合作,不断探索和创新,优化检测过程,提高分析的可靠性和效率。
硬质合金晶粒尺寸的有效检测对于保证材料质量和推动新材料开发具有关键意义。现有的检测技术各有优劣,综合应用光学显微镜、扫描电子显微镜和X射线衍射等多种方法,可以更全面地了解硬质合金的微观结构。同时,随着科技进步,新技术必将拓宽我们的检测能力,为工业生产和科学研究提供更多可能性。
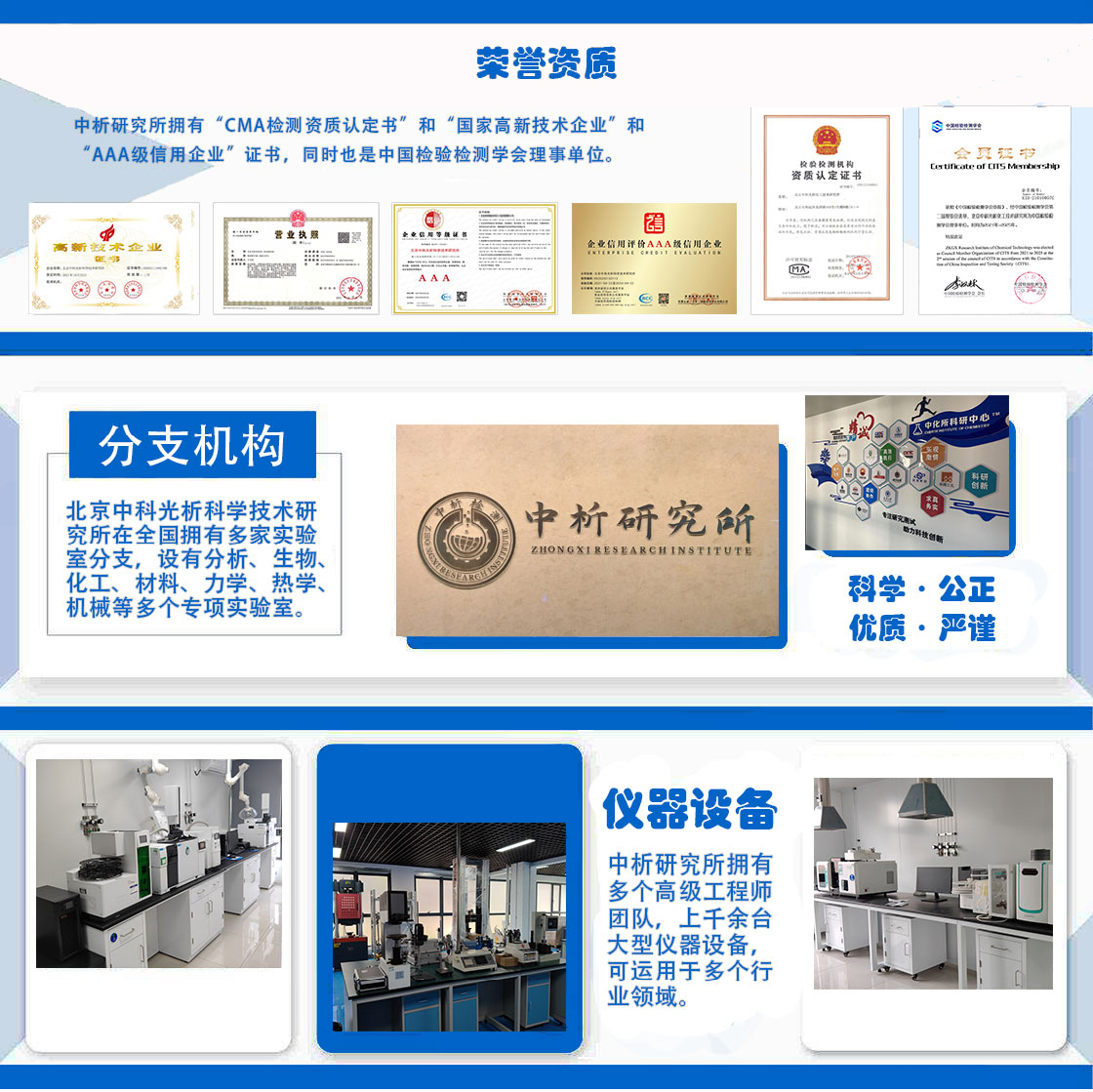
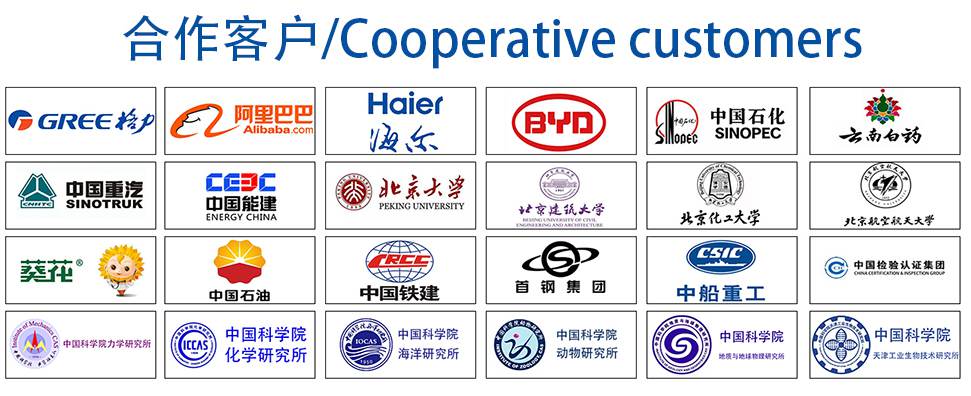