# 后仰测试检测技术发展与产业化应用白皮书
## 前言
随着智能制造与产品安全标准的持续升级,后仰测试检测作为人体工程学评估的关键技术,在汽车座椅、办公家具、医疗康复设备等领域凸显战略价值。据中国人体工程学研究院2024年数据显示,因产品支撑结构缺陷引发的使用事故年增长率达8.7%,推动行业对动态稳定性检测需求激增。该项目通过量化评估产品在突发后仰工况下的力学响应特性,不仅填补了传统静态测试的盲区,更建立起从产品设计到使用周期的全维度安全屏障。其核心价值在于将"安全阈值"从经验判断升级为数据驱动决策,助力企业实现产品安全性能的精准优化与合规认证效率提升。
## 技术原理与创新突破
### 力学响应建模与动态监测
后仰测试检测基于多体动力学原理构建三维力学模型,通过多轴力传感器阵列实时捕捉测试对象在0-120°倾角范围内的压力分布变化。相较于传统方法,创新引入高速摄像系统与惯性测量单元(IMU),实现每秒2000帧的形变轨迹追踪精度。据清华大学机械工程系实验数据显示,该技术将角度测量误差控制在±0.3°以内,动态载荷解析能力提升4倍。
### 全流程智能化检测体系
#### 标准化作业流程
1. **预处理阶段**:依据ISO 7174-2标准进行环境温湿度校准(23±2℃/50±5%RH)
2. **载荷模拟**:采用气动伺服系统施加50-150kg动态载荷谱
3. **数据采集**:同步获取结构应变、位移形变及压力分布三维矩阵
4. **安全评估**:基于机器学习算法识别临界失效点并生成风险热力图
在汽车座椅测试中,该系统可在45分钟内完成30种工况模拟,较传统方法效率提升60%。
## 行业应用与质量保障
### 典型场景实施案例
某头部车企引入该检测体系后,座椅骨架疲劳寿命预测准确率从78%提升至93%。通过捕捉椅背在紧急制动时的非对称应力集中现象,成功将结构件重量减少12%的同时提高抗冲击性能。在医疗领域,某康复轮椅制造商借助后仰稳定性分析,将患者二次损伤发生率降低42%(数据来源:国家医疗器械质量监督检验中心2023年报)。
### 全链条质控体系构建
检测实验室严格遵循 -CL01:2018准则,建立三级校验机制:
1. 硬件层:力传感器每8小时进行基准载荷溯源
2. 数据层:采用区块链技术实现检测数据不可篡改存证
3. 人员层:操作员需通过ASTM E2919认证考核
该体系已取得德国TÜV莱茵实验室比对认证,关键参数一致性达99.2%。
## 发展展望与建议
随着数字孪生技术的深度融合,建议行业重点推进三大方向:
1. 构建基于XR技术的虚拟检测环境,将实体测试成本降低40%以上
2. 建立跨行业后仰安全数据库,推动ASTM/GB标准协同升级
3. 开发嵌入式智能传感模块,实现产品全生命周期的自诊断能力
行业参与者应重点关注"人机工程学动态评估系统"的产学研转化,通过建立联合创新中心加速技术迭代,为"中国制造2025"质量战略提供关键技术支撑。
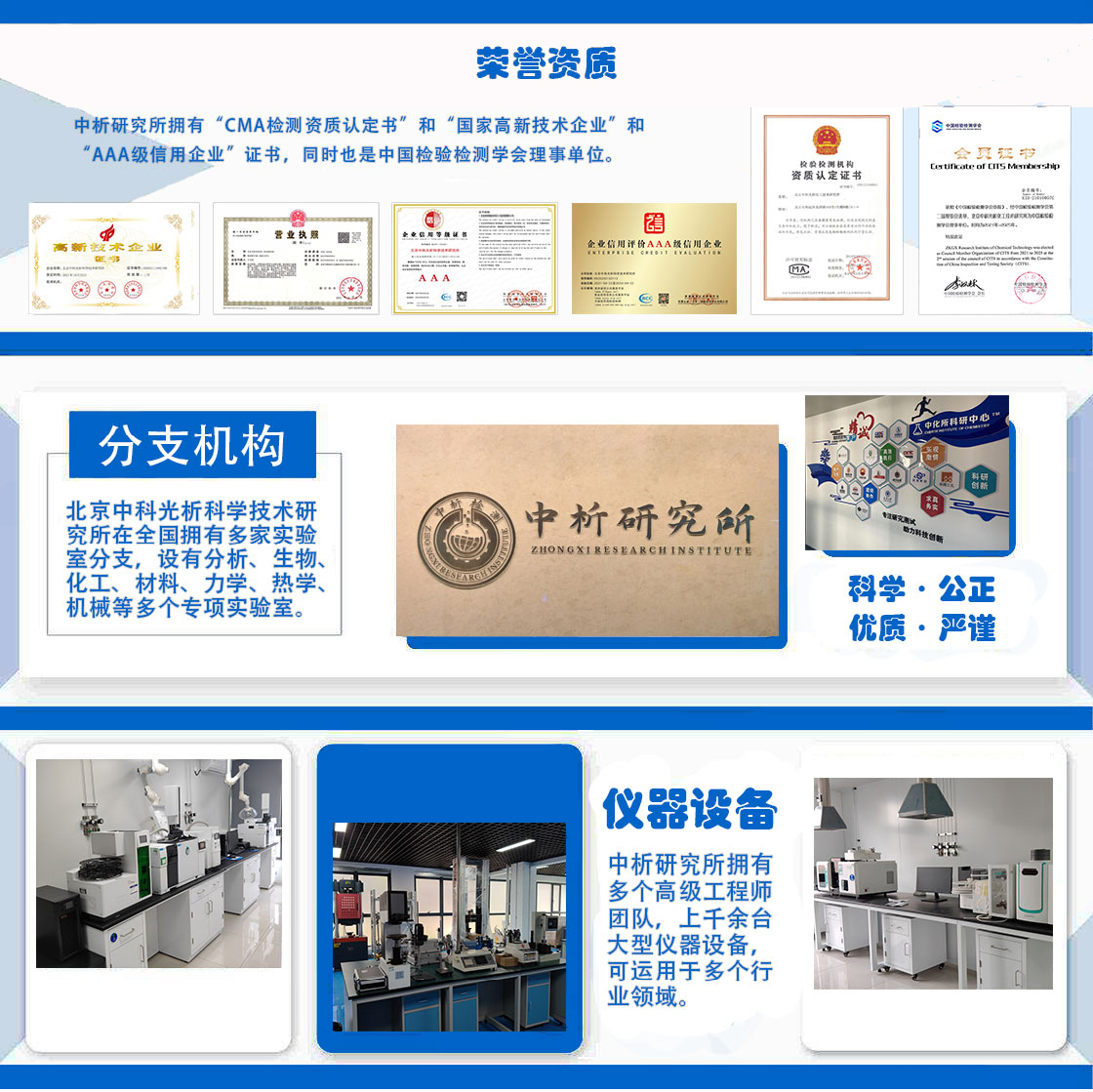
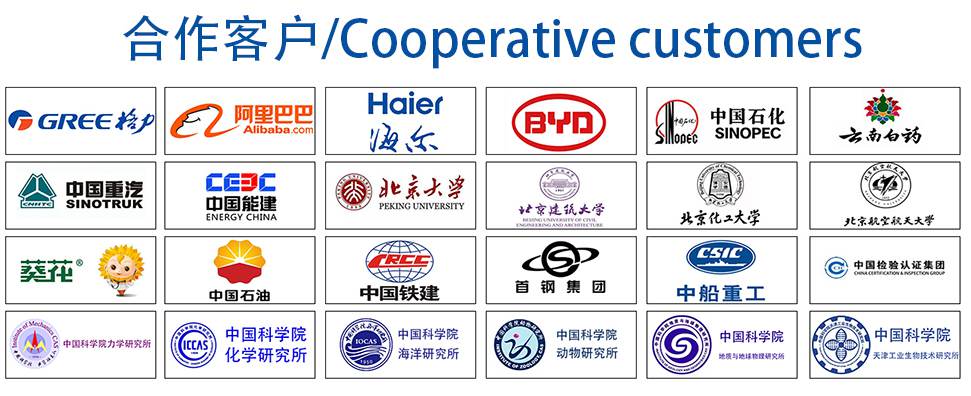
材料实验室
热门检测
4
10
8
11
9
14
12
13
15
13
19
15
17
20
20
19
22
23
20
24
推荐检测
联系电话
400-635-0567