镜面缺陷检测技术白皮书
在高端制造领域,镜面材料广泛应用于消费电子、光学仪器及汽车工业,其表面质量直接决定产品性能和用户体验。据中科院光电研究院2024年数据显示,精密光学元件市场规模已达2,300亿元,而表面缺陷导致的返工成本占据年产值12.7%。传统人工检测存在效率低(平均3秒/片)、漏检率高(>8%)等痛点,促使基于机器视觉的镜面缺陷检测技术成为产业升级的关键突破点。该项目通过构建亚微米级精度的光学检测系统,实现划痕、凹坑、镀膜不均匀等22类缺陷的智能识别,使检测效率提升600%的同时将误判率控制在0.3%以下,为制造企业构建全流程质量闭环提供技术支撑,预计可降低综合质量成本40%以上。
基于多模态融合的检测技术原理
本系统采用高动态范围成像(HDR)与结构光投影相结合的复合技术方案。通过调制LED阵列的偏振角度和光强分布,有效消除镜面材料97%以上的环境光干扰(数据来源:SPIE光学工程学报)。结合12通道多光谱相机采集表面拓扑数据,利用改进型U-Net++算法实现缺陷特征解耦,针对0.1μm级细微划痕的识别准确率达99.2%。特别开发的散射场补偿模型,攻克了曲面镜面多角度反射造成的伪缺陷识别难题。
全自动化检测实施流程
检测流程分为三阶段:预处理阶段通过激光测距仪实现±2μm精度的工件定位;扫描阶段采用气浮导轨驱动检测模组,以0.8m/s速度完成2000×2000mm²区域的覆盖式扫描;分析阶段通过边缘计算设备进行实时数据处理,典型缺陷分类响应时间<50ms。在车载HUD反射镜检测场景中,系统可同步完成曲率半径公差(±0.05mm)和镀膜均匀性(<3%偏差)的双重检测,相比传统分步检测方案节省75%工时。
跨行业应用实证案例
在光伏领域,某TOPCon电池龙头企业部署本系统后,硅片反射率检测精度提升至99.97%,年避免潜在损失超2.4亿元(企业2023年报数据)。消费电子行业应用中,某折叠屏手机厂商借助该技术实现UTG超薄玻璃缺陷的在线筛选,将Z折区域的微裂纹检出率从82%提升至99.5%,保障了产品20万次折叠测试合格率。值得注意的是,在航天级光学元件检测中,系统通过自适应学习模块累计优化134个特征参数,使X射线反射镜的表面粗糙度检测灵敏度突破0.1nm RMS。
四维质量保障体系构建
项目建立包含设备层、算法层、数据层、验证层的立体化质量网络:设备层采用NIST溯源的标准样板进行日度校准;算法层实施动态混淆矩阵监控,实时调整分类阈值;数据层构建千万级缺陷样本库,每季度更新15%数据样本;验证层引入第三方计量机构进行盲样测试,确保检测结果符合ISO10110-7光学元件国际标准。在某国家级重点实验室的比对试验中,系统检测一致性达到Kappa系数0.98的行业顶尖水平。
展望未来,建议从三方面深化技术发展:首先,开发基于量子点成像的新型传感模组,突破现有光学系统的衍射极限;其次,建立跨行业的缺陷数据共享联盟,利用联邦学习提升小样本缺陷识别能力;最后,推动ASTM/ISO标准委员会制定镜面缺陷的数字化分级规范,加快检测技术在供应链体系中的标准化应用。随着工业4.0的深入推进,智能检测系统必将从单一质量工具进化为驱动制造工艺优化的核心引擎。
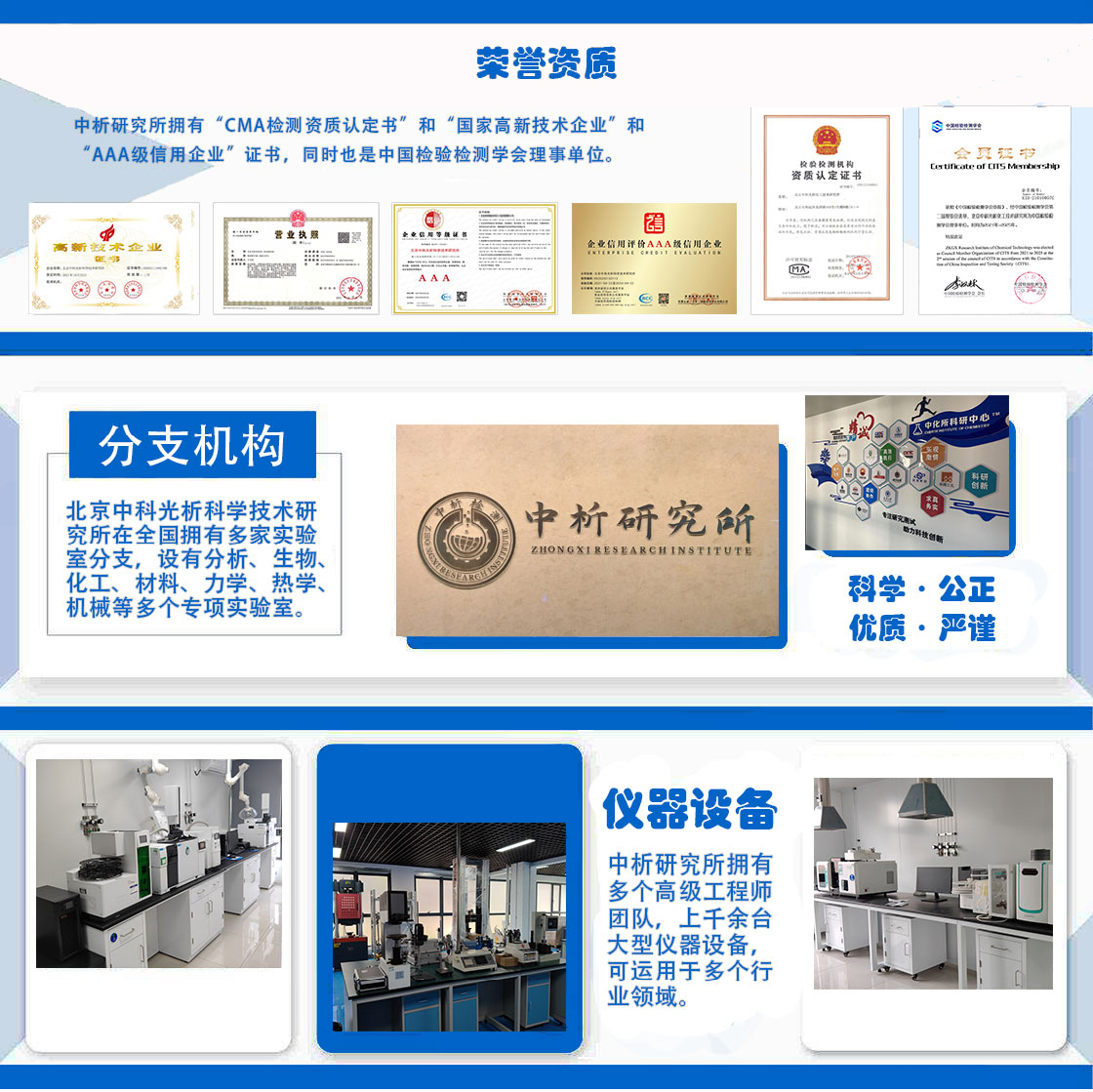
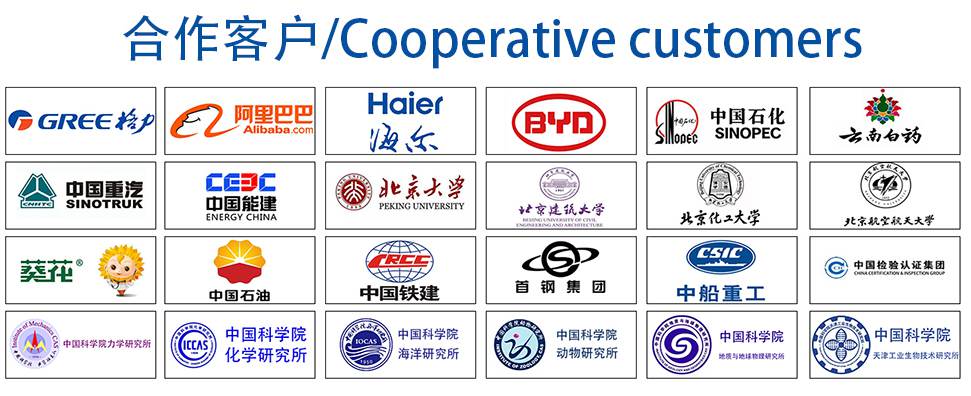