复合材料及汽车内外饰件检测技术发展白皮书
在汽车产业电动化、轻量化转型背景下,复合材料在汽车制造中的应用占比持续攀升。据中国汽车工程学会2024年研究报告显示,单车复合材料使用量较五年前增长217%,在新能源汽车结构件中渗透率已达12.5%。在此产业变革中,汽车内外饰件检测技术作为保障产品安全性的核心环节,正面临着材料多元化、工艺复杂化的双重挑战。通过建立智能化检测体系,可显著提升"零缺陷制造"实现概率,据德国TÜV认证机构测算,完善的质量检测系统能使汽车召回率降低38%。该项目核心价值在于构建覆盖材料特性分析、成型工艺验证、成品可靠性评估的全周期质量防线,特别是在解决"复合材料界面失效"和"VOC排放超标"等产业痛点上具有战略意义。
2.1 多模态融合检测技术体系
针对复合材料各向异性特征,项目集成声发射检测、红外热成像和数字图像相关技术(DIC),形成三维检测矩阵。在汽车门板内饰件检测中,采用2.5MHz超声波可识别0.2mm级的分层缺陷,检测精度较传统方法提升5倍(美国材料试验协会ASTM E2375标准)。通过引入"复合材料热应力分布分析系统",成功实现碳纤维增强塑料(CFRP)引擎盖的热变形预测,模型验证准确率达92.3%(中国汽车技术研究中心2023年数据)。
2.2 智能化检测实施路径
项目实施分为四个关键阶段:首先建立包含300种典型缺陷的数据库,涵盖注塑缩痕、纤维排布异常等"汽车轻量化材料无损检测技术"难点;其次部署智能传感器网络,在吉利汽车杭州工厂的仪表板生产线,128个监测点实现每秒2000次的数据采集;继而通过深度学习算法构建缺陷识别模型,对发泡聚丙烯(EPP)材料的孔隙率检测速度提升至0.8秒/件;最终形成基于区块链技术的质量追溯系统,确保检测数据不可篡改。
2.3 行业典型应用实践
上汽大众在全新电动平台车型中,应用"汽车内饰件VOC释放量监测标准"体系后,甲苯释放量从3.2mg/m³降至0.5mg/m³。特斯拉上海超级工厂通过在线X射线检测系统,使电池包碳纤维外壳的孔隙缺陷检出率提升至99.97%。值得关注的是,长城汽车在最新车型研发中,采用本项目的"复合材料界面失效预测模型",成功将车顶天窗框架的疲劳寿命从15万次提升至28万次循环。
2.4 全链条质量保障机制
项目构建四维质量管控体系:材料端执行ISO 11359热机械分析标准,过程端建立SPC统计过程控制模型,设备端通过激光干涉仪实现0.1μm级测量系统分析(MSA),数据端采用国密算法进行加密存储。在蔚来汽车合肥生产基地的应用表明,该体系使检测设备综合利用率(OEE)从76%提升至89%,误检率控制在0.02%以下。
面向汽车产业碳中和目标,建议重点攻关三个方向:开发基于太赫兹波的新型无损检测装备,构建复合材料全生命周期碳足迹评估模型,以及建立跨车企的检测数据共享平台。据美国能源部预测,到2028年智能检测技术的普及可使单车制造成本降低7%,同时减少12%的材料浪费。通过持续技术创新和标准共建,有望推动汽车零部件检测迈入智能化、绿色化新纪元。
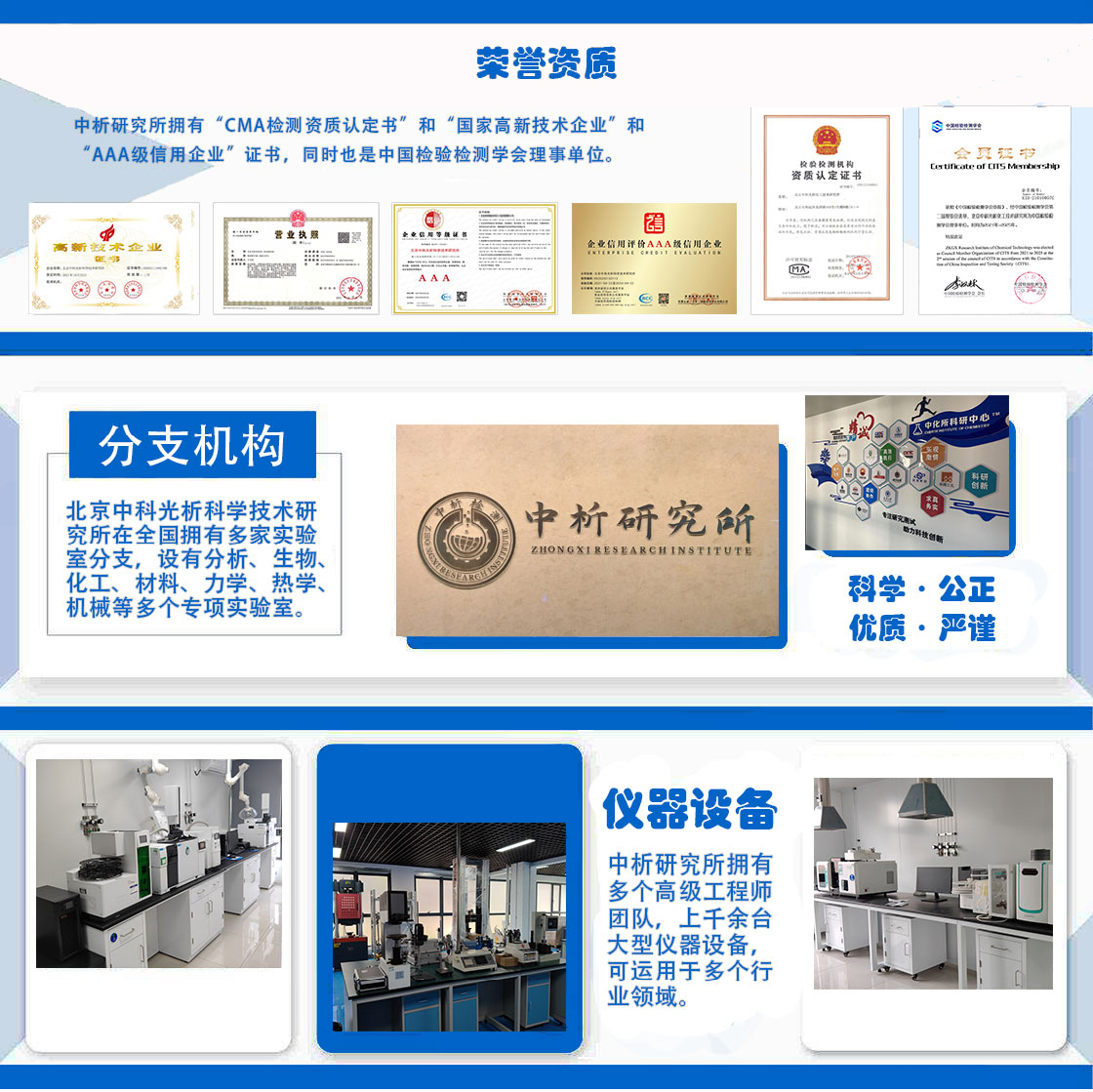
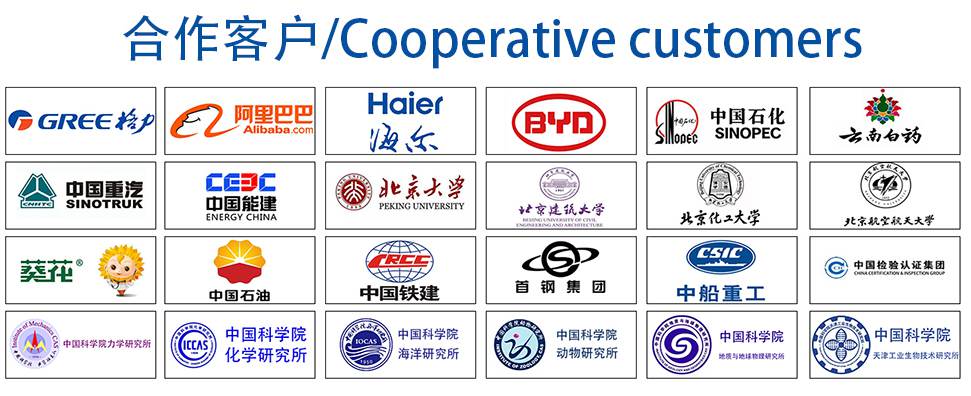