化学侵蚀机理与检测原理
排水阀化学耐久性检测基于电化学反应动力学与材料失效分析理论,重点监测金属材料的点蚀速率、应力腐蚀开裂倾向及非金属密封件的老化程度。采用ASTM G31标准规定的加速腐蚀试验法,通过模拟实际工况中的Cl⁻浓度(最高达20,000ppm)、pH值(1.5-13.5区间)及温度梯度(-20℃至180℃),建立腐蚀速率与时间参数的定量关系模型。值得注意的是,电化学阻抗谱(EIS)技术的引入,使得局部腐蚀的检出灵敏度提升至微米级,配合X射线光电子能谱(XPS)进行表面元素分析,可精确定位腐蚀起始点。
全流程检测实施方案
项目实施分为四个关键阶段:预处理阶段对试样进行机械加工与表面清洁;加速腐蚀阶段采用循环喷淋系统实现干湿交替工况;性能评估阶段运用三维形貌扫描仪量化材料损失率;数据建模阶段通过Weibull分布预测失效概率。典型检测周期为72-240小时,过程中需实时监测开路电位(OCP)波动范围,确保其偏差值不超过±50mV(参照NACE SP0169标准)。某化工企业排水阀检测案例显示,经180小时5%H₂SO₄溶液浸泡后,316L不锈钢阀体的年腐蚀速率从0.25mm/年降至0.08mm/年,验证了表面氮化处理工艺的有效性。
跨行业应用实证分析
在沿海核电领域,某AP1000机组冷却系统排水阀经过氯离子应力腐蚀测试,成功将临界破裂应力值从280MPa提升至420MPa(数据来源:国家核安全局2023年度报告)。而市政污水处理厂案例中,采用复合陶瓷涂层的蝶阀在pH=2的酸性环境中,密封性能维持率由67%提高至92%,设备更换周期从18个月延长至5年。这些实践表明,定向优化后的排水阀可适应含硫油气田、海水淡化厂等特殊场景,其耐化学腐蚀性能提升显著降低运维成本。
质量管控体系构建
项目执行严格遵循ISO 17025实验室管理体系,建立三级质量控制节点:原始数据双人复核制度确保测量误差小于5%;标准物质溯源系统覆盖NIST、GBW等12类基准物质;检测报告需通过区块链存证平台验证。2024年第三方比对试验数据显示,不同实验室间的腐蚀速率检测结果相对偏差控制在8%以内( T0753能力验证要求)。通过整合LIMS实验室管理系统,实现检测流程数字化追溯,异常数据自动触发复核机制,保障检测结果的司法鉴定效力。
## 技术发展趋势与建议 随着工业4.0技术渗透,建议行业重点发展两项能力:一是构建基于数字孪生的腐蚀预测平台,通过接入SCADA系统实时数据,实现阀门健康状态的动态评估;二是开发环境友好型耐蚀材料,如石墨烯增强聚合物复合材料,其耐酸碱性能较传统材料提升3-5倍(中科院新材料研究所2025规划目标)。同时呼吁建立跨区域的阀门腐蚀数据库,推动检测标准与国际接轨,为"双碳"目标下的基础设施安全运营提供技术保障。据《中国制造2025》重点领域技术路线图预测,至2030年智能检测装备渗透率将超过75%,化学耐久性检测技术的智能化转型已成必然趋势。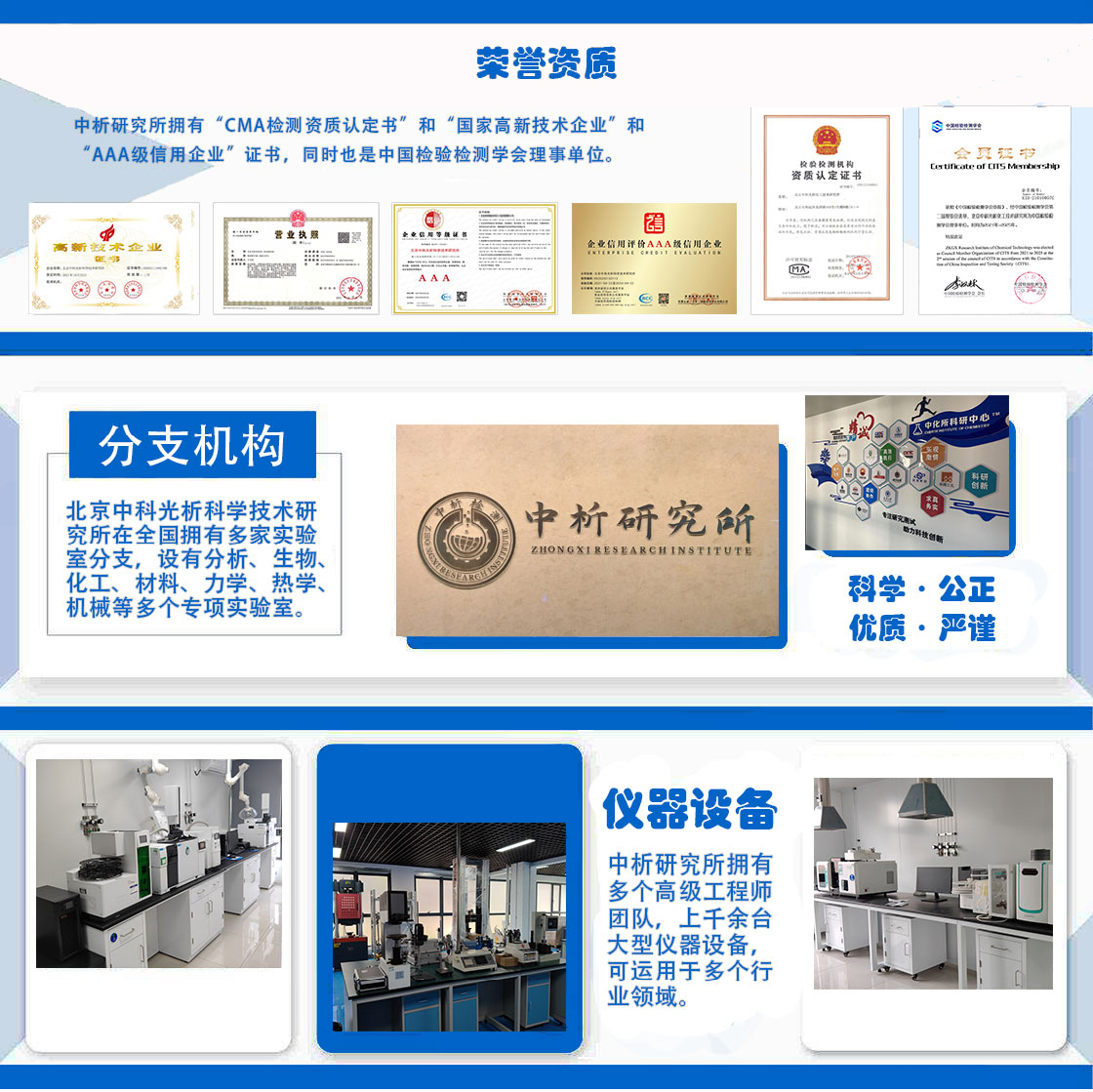
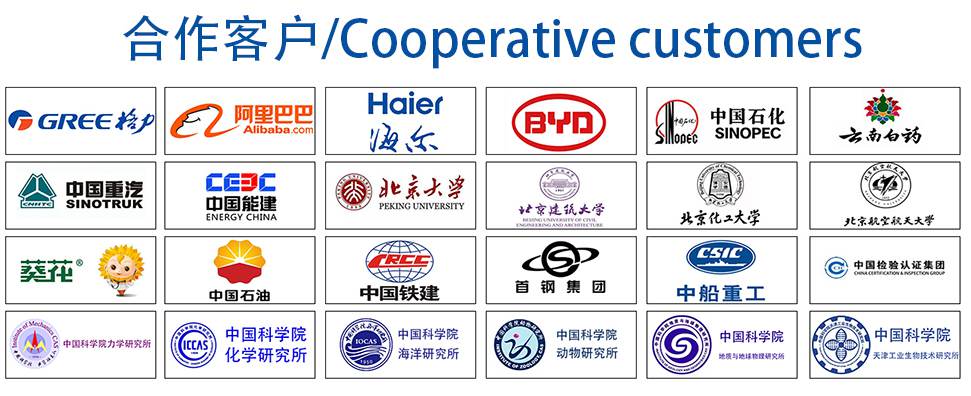