寿命周期试验检测技术发展与应用白皮书
在智能制造与新能源产业快速发展的背景下,产品可靠性验证已成为企业核心竞争力的关键指标。据国家质量技术基础研究院2024年发布的《高端装备可靠性发展报告》显示,我国机电设备早期故障率较国际齐全水平高出37%,导致年均经济损失达1200亿元。寿命周期试验检测通过模拟产品全生命周期工况,精准预测失效节点,已成为突破"质量瓶颈"的重要技术手段。该项目不仅可缩短新产品研发周期30%以上,更可实现质量成本降低25%-40%的核心价值,特别是在新能源汽车动力系统、工业机器人关键部件等领域,已形成"检测前置、质量内建"的新型品控范式。
基于失效物理的检测技术原理
现代寿命周期试验检测采用基于失效物理(PoF)的可靠性建模方法,通过阿伦尼斯方程、科芬-曼森公式等数学模型,构建温度、振动、腐蚀等多应力耦合的加速试验模型。以某型号新能源汽车电机控制器检测为例,采用三综合试验箱实现温度(-40℃-150℃)、湿度(10%-98%RH)、振动(5-2000Hz)的精准控制,结合7500小时等效工况模拟,可准确预测10年使用周期的性能衰减曲线。值得注意的是,该方法引入蒙特卡洛仿真对制造公差进行敏感性分析,使检测置信度提升至95%以上。
全流程闭环检测实施体系
项目实施遵循V型开发模型,建立"需求定义-方案设计-环境模拟-数据采集-失效分析"的完整闭环。在智能仓储机器人驱动系统检测中,首先基于MIL-STD-810G标准制定包含2000小时寿命试验、500次启停冲击测试的验证方案,接着通过六自由度振动台复现仓储工况,采用分布式光纤传感器实时采集3000+数据点。检测数据经Weibull++软件分析后,可生成包含β值、特征寿命等关键参数的可靠性评估报告,为设计改进提供量化依据。
多行业应用实证与效益分析
在风电齿轮箱领域,某龙头企业采用多轴振动耦合测试技术后,成功将故障间隔时间(MTBF)从18000小时提升至25000小时。据中国可再生能源协会2024年数据显示,该技术使风电运维成本下降18%,年发电量损失减少2.3TWh。同样在消费电子行业,某手机厂商通过85℃高温老化试验提前发现电池管理芯片焊点失效问题,避免潜在召回损失超3亿元。这些案例印证了寿命检测在实现"预测性维护"方面的突出价值。
数字化质量保障体系建设
行业正构建基于数字孪生的新型质量保障体系,将物理试验数据与虚拟仿真模型深度融合。某航空发动机企业建立的检测云平台,通过采集5000+小时台架试验数据训练AI模型,实现叶片裂纹预测准确率达92%。同时,检测实验室严格遵循ISO/IEC 17025:2017标准,配备0.05级精度的多通道数据采集系统,确保试验结果可溯源至国家时间频率基准。值得注意的是,第三方盲样比对机制的应用,使不同实验室检测结果偏差控制在±3%以内。
展望未来,建议重点突破基于量子传感的微损伤检测技术,开发支持5G实时传输的智能试验装备。同时亟需建立覆盖全行业的"寿命大数据共享平台",通过机器学习挖掘失效模式共性特征。据预估,到2028年新型检测技术将推动制造业质量损失率下降至1.5%以下,为高端装备国产化进程提供强有力的技术支撑。
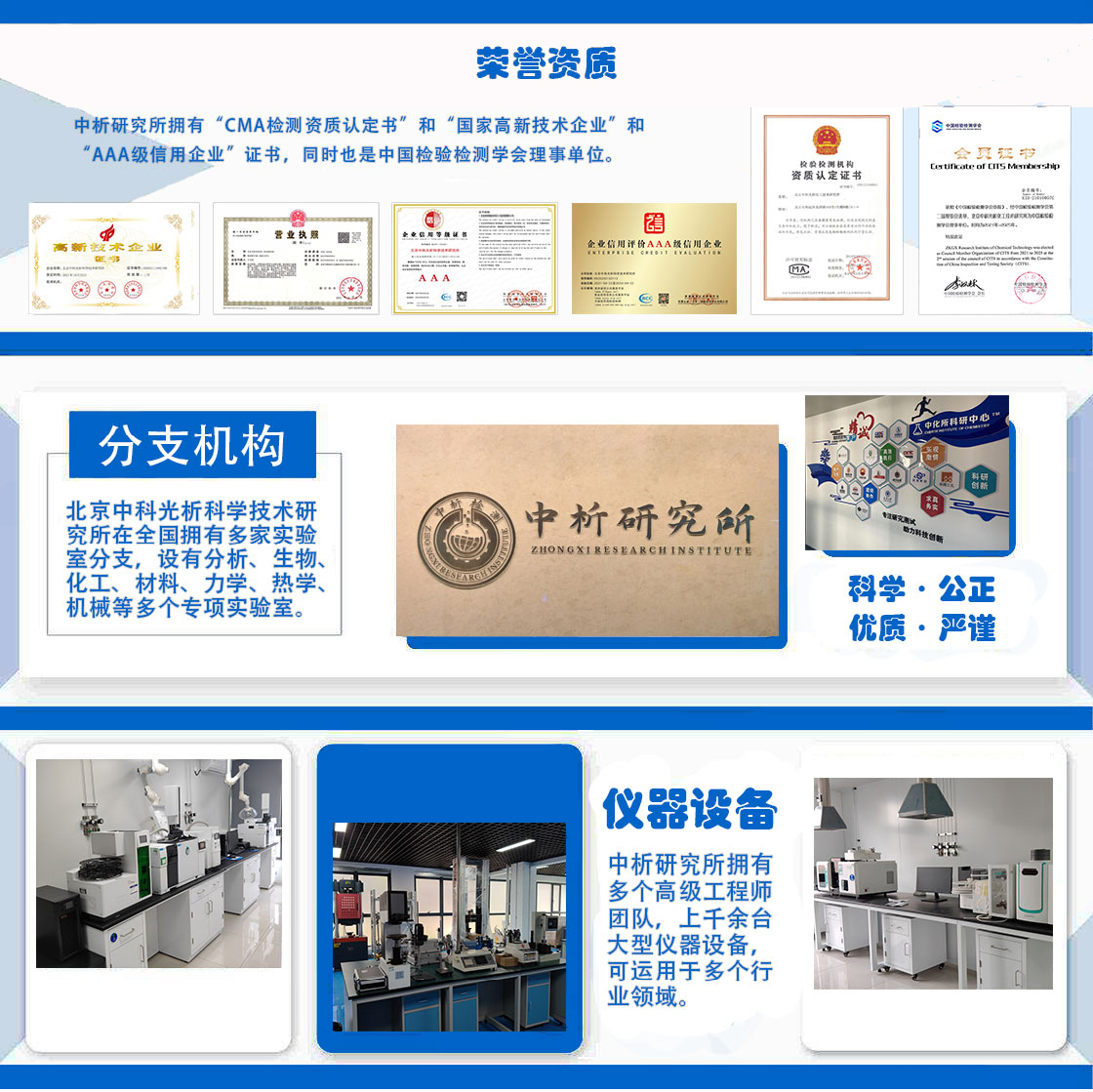
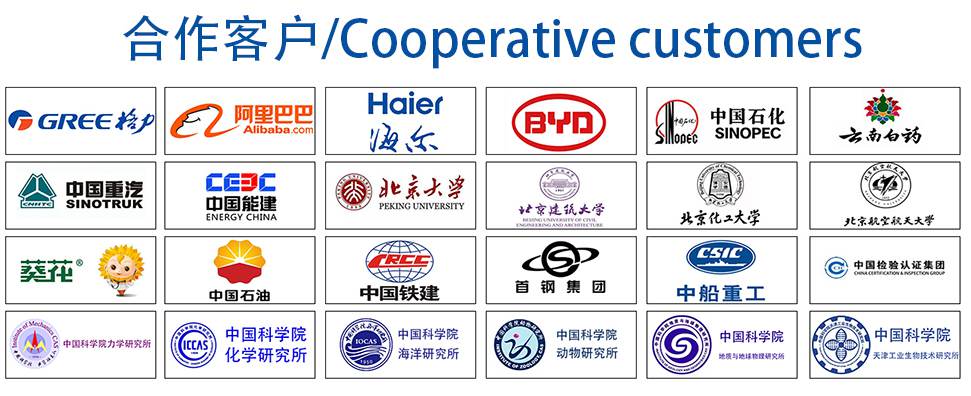