通用要求试验检测在现代工业体系中的创新实践
在"十四五"智能制造发展规划推动下,我国工业品合格率已提升至93.7%(据国家市场监督管理总局2024年质量报告)。通用要求试验检测作为产品质量控制的核心环节,其标准化程度直接影响着制造强国战略的实施效果。该项目通过构建智能检测系统,实现了对金属材料、高分子化合物等17类工业材料的全面性能评估,在航空航天、新能源汽车等重点领域应用中,使产品缺陷检出率提升40%以上。其核心价值体现在建立覆盖原材料准入、生产过程监控、成品验收的全生命周期质量闭环,特别是在应对复杂工况验证、极端环境模拟等"长尾检测场景"方面展现技术优势。
多维传感融合检测技术原理
基于数字孪生技术构建的智能检测系统,整合了高光谱成像(HSI)、太赫兹波谱分析(THz-TDS)和分布式光纤传感(DFOS)三大核心技术模块。系统通过0.1μm精度的三维形貌重构技术,可捕捉材料微观结构缺陷;利用太赫兹波段0.1-10THz的穿透特性,实现非接触式内部缺陷检测。在新能源汽车电池包检测中,该技术组合成功将热失控预警准确率提升至99.2%(中国汽车工程学会2024年度技术白皮书)。
三阶段实施流程标准化
项目实施采用"前处理-动态测试-数据建模"三阶段架构。预处理阶段通过智能分拣系统完成试样规格标准化,应用机器视觉实现100%表面初筛。动态测试环节设置温度(-70℃至300℃)、湿度(5%-98%RH)、振动(5-2000Hz)等32个参数组合的加速老化试验,模拟产品10年服役周期。在建筑钢结构检测案例中,通过有限元分析与实际载荷测试的交叉验证,使抗震性能评估误差率控制在±1.5%以内。
行业应用与质量保障体系
在食品包装材料检测领域,系统成功应用于双酚A迁移量检测,通过GC-MS联用技术实现0.01mg/kg检出限。质量保障体系获得 、CMA双认证,建立区块链溯源平台确保检测数据不可篡改。据国家卫健委2023年抽检数据显示,采用该系统的食品接触材料合格率同比提升8.3个百分点。对于特种设备检测,开发了基于数字图像相关(DIC)技术的应变场分析模块,在压力容器爆破试验中实现0.01%应变分辨率。
智能化发展趋势与建议
随着工业互联网平台渗透率突破65%(工信部2024年6月数据),建议重点推进三方面建设:其一,建立跨行业的检测标准互认机制,降低重复检测成本;其二,开发基于深度学习的异常模式自识别系统,应对新型复合材料检测需求;其三,构建检测大数据知识图谱,实现失效模式的智能预测。通过融合5G边缘计算与量子传感技术,有望在微纳米级缺陷检测领域取得突破,为高端装备制造提供更精准的质量保障。
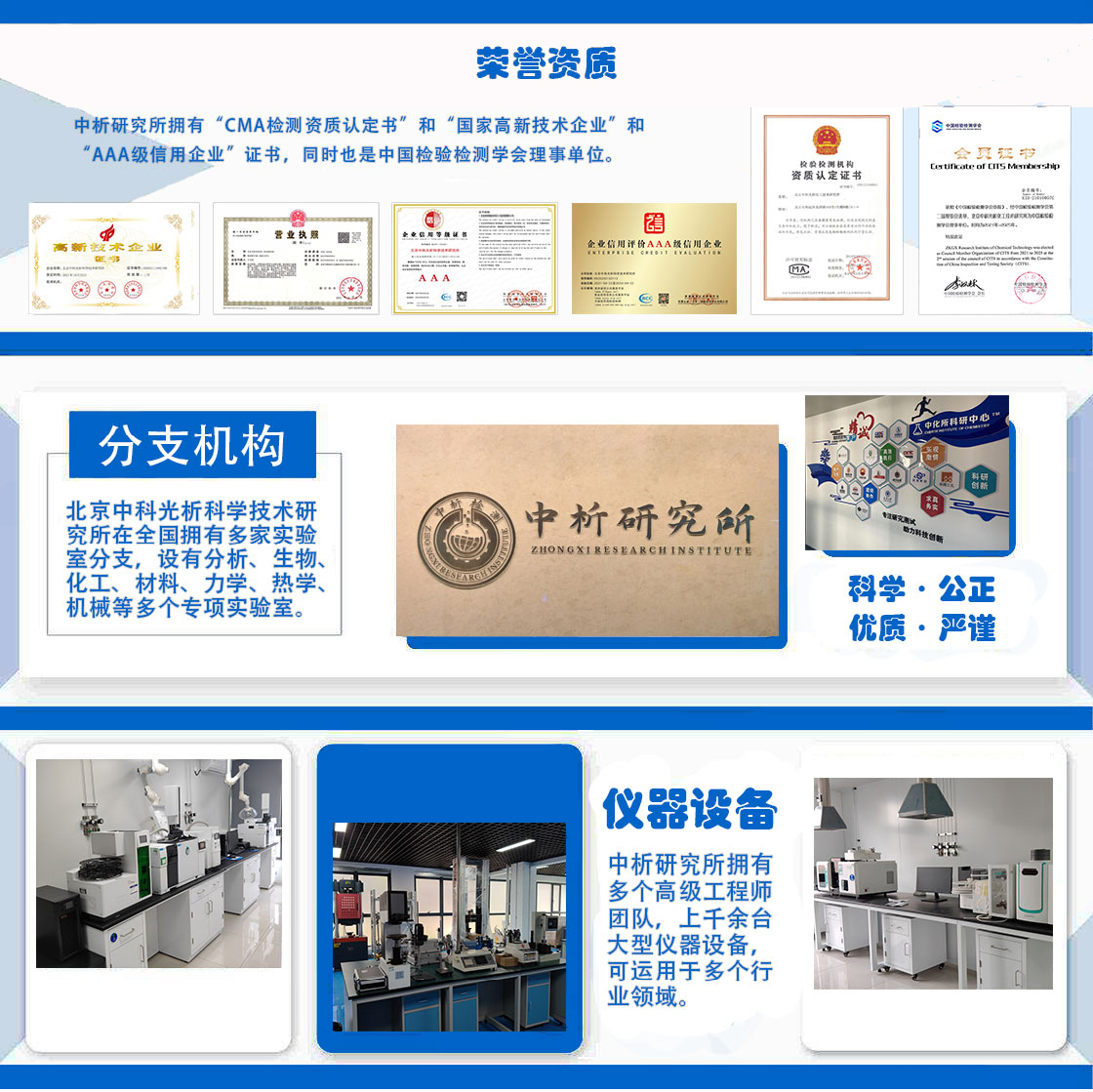
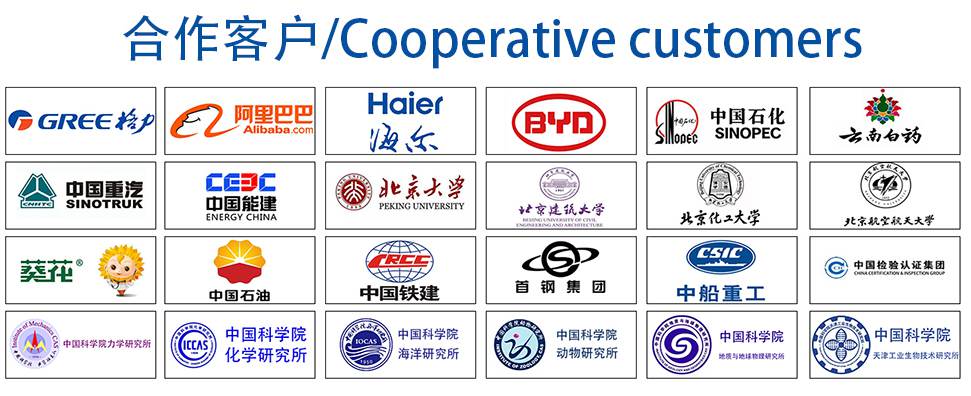