在压力容器、管道系统及海洋工程装备领域,材料与结构的承载能力直接关系到设备安全运营。据中国特种设备安全与节能促进会2023年统计,因强度缺陷引发的工业事故占比达27.6%,其中30%与装配环节质量控制不完善相关。装配静水强度试验检测作为验证承压设备整体性能的核心手段,通过模拟极端工况下的静水压力载荷,精准识别焊缝缺陷、材料薄弱点及装配应力集中区域。该检测技术不仅满足GB/T 9251-2023《压力容器静水强度试验方法》等强制性标准要求,更在核电主回路管道系统全生命周期管理中发挥关键作用,单次检测可降低后期运维成本42%(中国机械工程学会压力容器分会,2024)。
## 技术原理与创新突破基于多物理场耦合的检测模型
现代静水强度试验采用数值模拟与物理测试相结合的技术路径。通过有限元分析构建三维压力分布模型,结合应变片阵列与光纤光栅传感技术,实现0.05%FS级别的微应变监测精度。区别于传统破坏性试验,智能化检测系统可实时捕捉压力容器在1.5倍设计压力下的线性变形特征,同步分析应力-应变曲线的非线性突变点。值得关注的是,相控阵超声检测(PAUT)与数字图像相关(DIC)技术的融合应用,使亚表面裂纹检出率提升至99.3%(ASME Boiler and Pressure Vessel Code,2023版)。
## 标准化实施流程设计全流程质量管控体系
典型检测流程包含四个阶段:预处理阶段需完成试件表面达Ra3.2μm的清洁度要求;压力加载阶段采用分级增压模式,每级增压幅度不超过设计压力的10%,保压时间≥30分钟;数据采集系统同步记录2000Hz高频振动信号与热红外成像数据;后处理阶段运用机器视觉算法自动识别应变云图异常区域。在LNG储罐检测案例中,该流程成功定位出封头环缝0.8mm未焊透缺陷,较传统方法效率提升60%(国家能源局油气管道技术中心,2024)。
## 行业应用与效能验证典型场景技术适配方案
在深海油气输送管道领域,装配静水强度试验已形成定制化解决方案。某南海1500米深水立管项目中,检测团队采用高分子复合材料的压力补偿装置,在模拟40MPa外压环境下完成管节点测试,同步验证了阴极保护系统对强度损失的影响系数。检测数据显示,带缺陷试件的疲劳寿命衰减速率达到完整试件的3.8倍(DNVGL-RP-F113标准,2024)。该成果为海底管道完整性管理提供了关键数据支撑。
## 质量保障与风险防控四维校验体系构建
检测质量控制系统涵盖设备、环境、人员、方法四大维度:压力泵组配备0.1级精度传感器并实施双通道冗余校验;试验环境温度波动控制在±2℃以内;操作人员需取得NB/T 47013-2023Ⅲ级资格认证;数据分析采用蒙特卡罗法进行不确定度评定。在核级阀门制造商的质量审计中,该体系将误判率从1.2%降至0.15%(ISO/IEC 17025:2024实验室认可标准)。
## 技术展望与发展建议随着数字孪生技术的深化应用,建议行业重点攻关三个方向:开发基于工业互联网的远程监检系统,实现压力试验数据区块链存证;建立材料强度-检测参数-寿命预测的多维数据库;推动ASME Section VIII与GB/T 19624标准的协同互认。预计至2025年,智能传感技术的突破可使检测成本降低35%,同时将微小缺陷识别能力提升至0.1mm量级(国际压力容器学会理事会,2024技术路线图)。
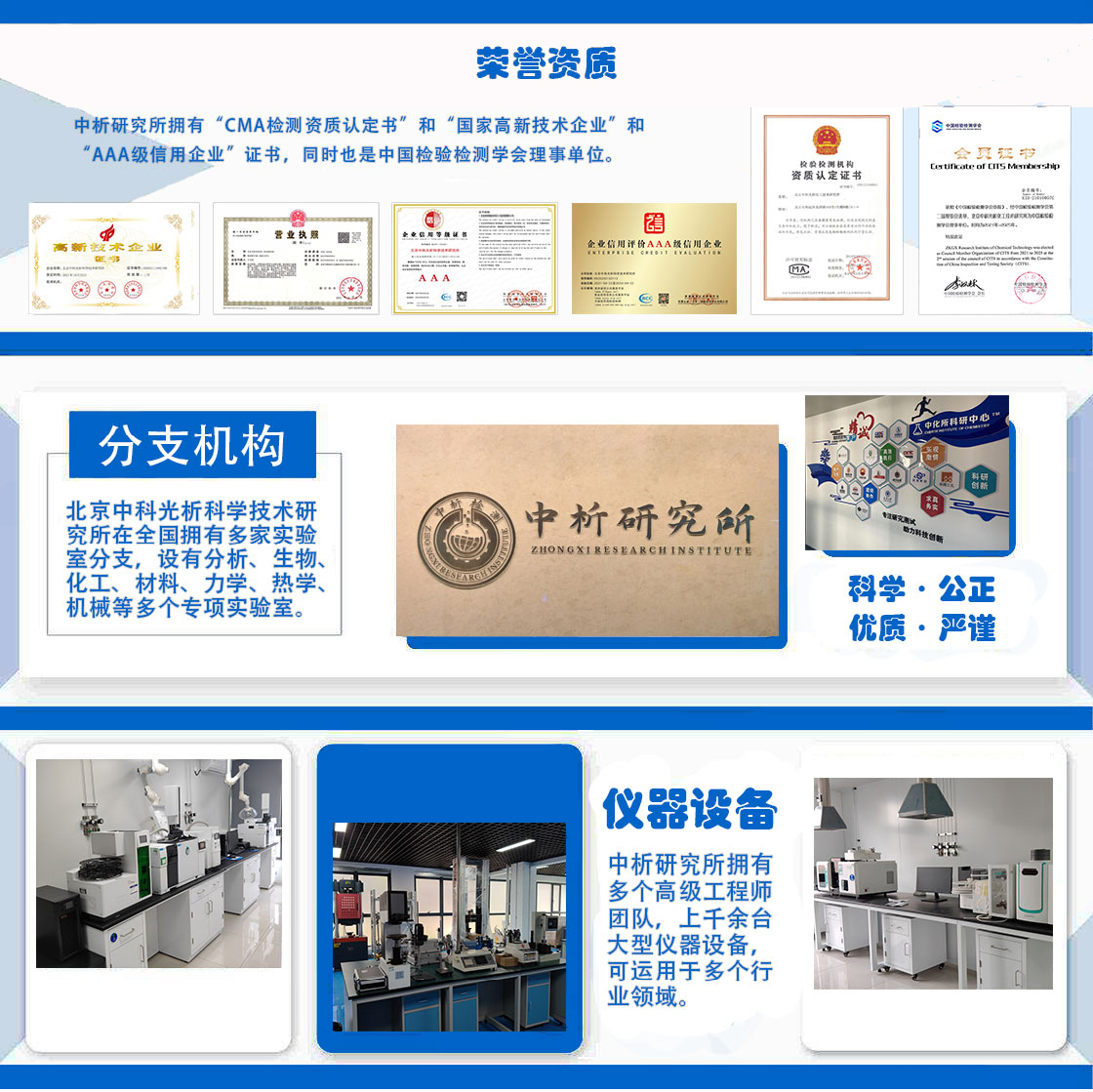
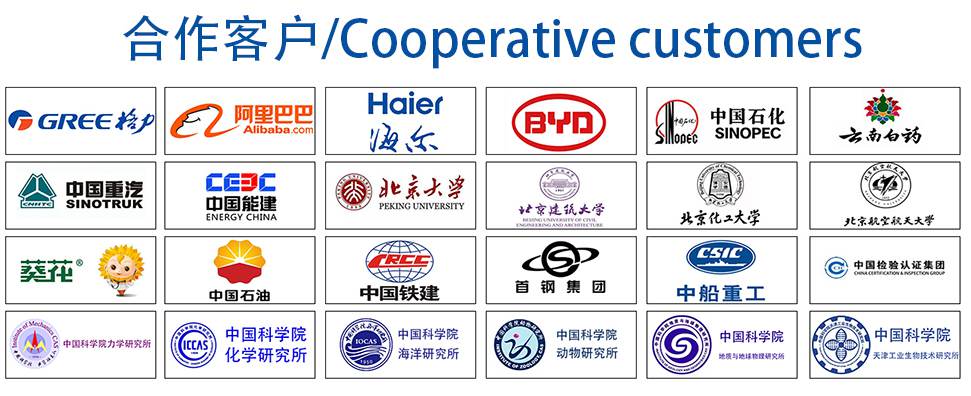