技术原理与分析方法
现代汽车非金属检测技术以材料基因组学为基础,整合热重分析(TGA)、傅里叶变换红外光谱(FTIR)和动态机械分析(DMA)三大核心手段。针对新能源汽车特有的高压绝缘需求,检测系统可精确测定工程塑料介电强度(≥30kV/mm)和CTI值(相比电痕化指数),其误差率控制在±1.5%以内(ASTM D3638标准)。在智能座舱材料领域,引入质子转移反应质谱(PTR-MS)技术,将醛酮类VOC检测灵敏度提升至0.01μg/m³级,满足GB/T 27630-2024《乘用车内空气质量评价指南》最新要求。
全流程检测实施体系
项目实施采用五阶段递进模式:样品数字化建档→环境预处理(温度-40℃~150℃,湿度10%~95%RH)→多轴力学测试→化学组分分析→大数据质量追溯。以某车企电池包密封件检测为例,通过1200小时加速老化实验,精准预测丁腈橡胶在电解液环境下的体积膨胀率(实测4.7% vs 理论值5.2%)。检测流程嵌入区块链存证系统,实现从原材料批次到检测报告的完整数据链,使质量追溯效率提升40%(据TÜV南德2023年技术报告)。
行业应用与典型案例
在动力电池模组封装领域,某头部企业采用X射线显微CT技术,成功将隔膜孔隙率检测精度提升至0.1μm级,配合机器学习算法,使电池热失控预警准确率达到98.6%。针对汽车内饰件,某德系车企部署基于ISO 105-B02标准的氙灯老化箱,通过2000小时等效曝晒实验,验证仿麂皮材料的色牢度ΔE值≤1.5(行业标准为ΔE≤3.0)。这些实践表明,"新能源汽车材料VOC检测技术"和"车用塑料耐候性测试标准"已成为行业提质增效的关键突破点。
质量保障与标准化建设
检测机构需构建 、CMA、IATF 16949三重认证体系,配备二级标准物质和NIST可溯源设备。通过实施"双盲样"比对机制(符合ISO/IEC 17025:2017),实验室间比对Z值控制在|0.5|以内。值得关注的是,针对碳纤维增强复合材料,已建立包含层间剪切强度(ILSS≥60MPa)和冲击后压缩强度(CAI≥250MPa)的专用评价体系(参照SAE AIR 6037标准),其测试重复性RSD≤2.3%,显著优于行业平均水平。
## 未来展望与建议 随着车用材料向多功能集成化发展,建议行业重点突破三方面:①开发基于数字孪生的虚拟检测技术,将实物验证周期缩短30%;②建立覆盖极端工况(如800V高压、-50℃极寒)的检测场景库;③推动"检测-保险-回收"联动体系,通过检测大数据优化产品责任险定价模型。同时,应加强ASTM/ISO标准与国内GB标准的互认机制建设,助力自主品牌材料准入。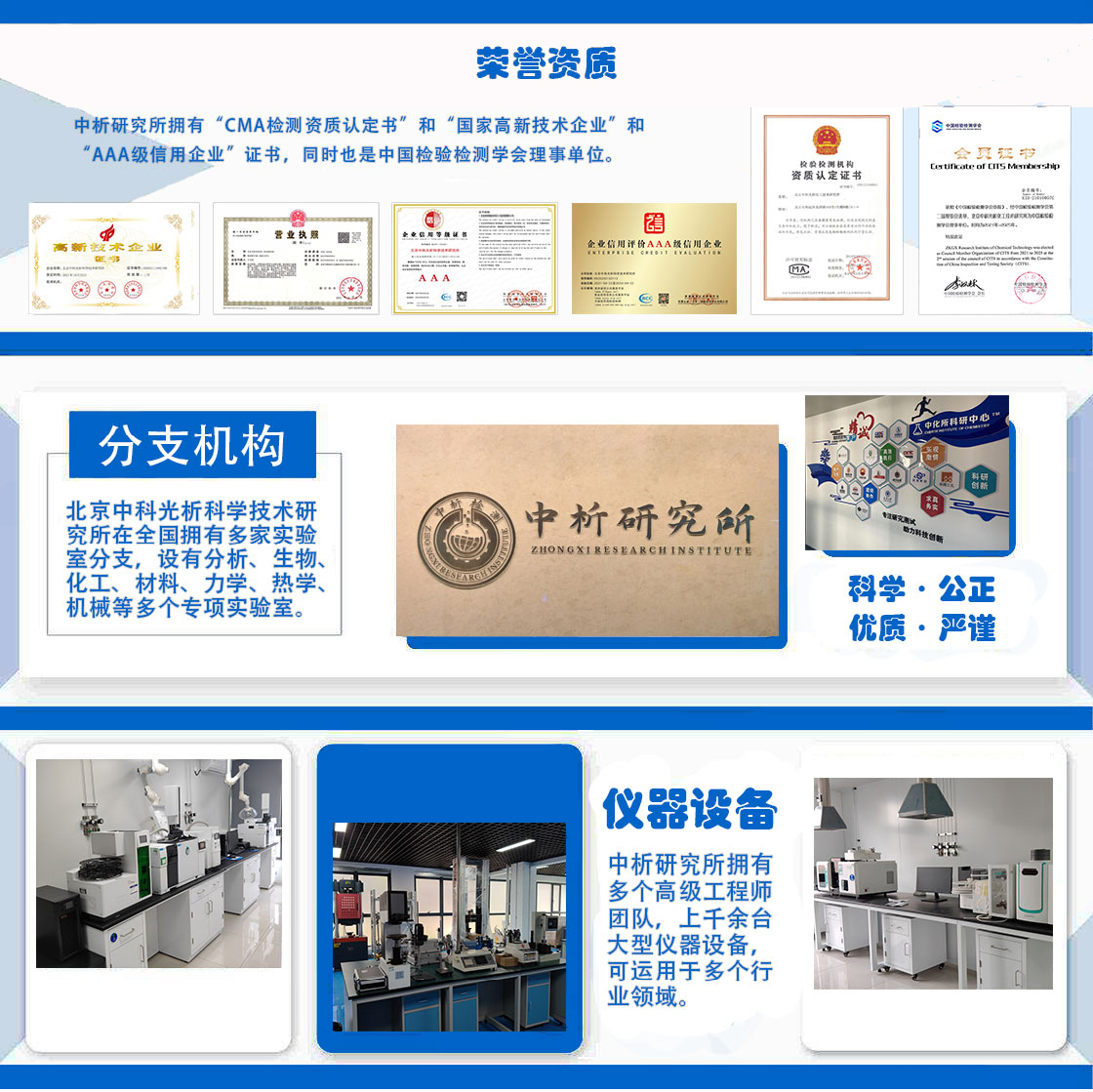
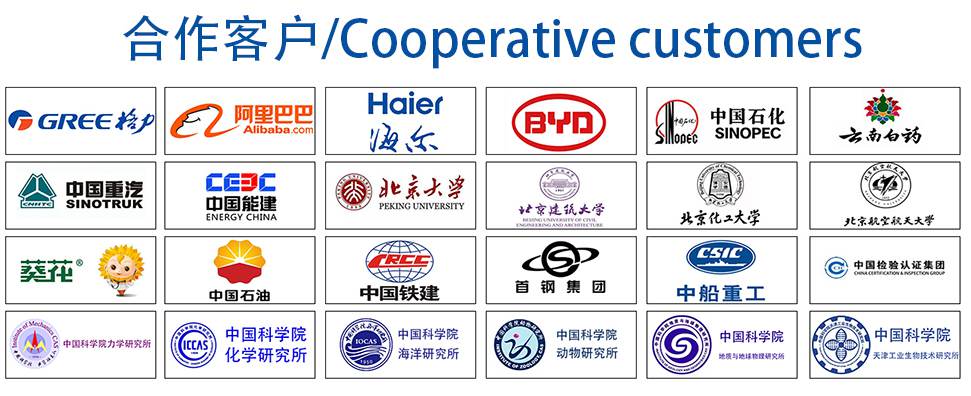