钢对钢(钢套筒法)拉伸抗剪强度标准值检测白皮书
随着装配式钢结构建筑的快速发展,套筒连接工艺已成为关键节点的核心承载构件。据中国建筑科学研究院2024年数据显示,我国装配式钢结构建筑年竣工量突破1.2亿平方米,其中钢套筒连接节点占比达68%。在此背景下,钢对钢拉伸抗剪强度标准值检测成为保障工程质量的核心环节,直接关系建筑结构抗震性能和服役寿命。本检测项目通过量化评估套筒连接界面的力学性能,为设计优化、工艺改进和工程验收提供科学依据,其核心价值体现在降低结构安全隐患、提升建筑工业化水平及推动绿色建造技术革新方面。
技术原理与检测方法
基于剪切滑移理论和双剪试验法,钢套筒法拉伸抗剪强度检测通过模拟实际工况下的多维受力状态,精确测定界面抗剪强度临界值。试验系统采用伺服液压加载装置(精度±0.5%FS),配合三维数字图像相关(3D-DIC)技术,实时捕捉0.02mm级微位移变化。关键参数计算遵循《金属材料室温拉伸试验方法》(GB/T 228.1-2021),通过建立F-Δ曲线拐点识别抗剪强度标准值。值得注意的是,新型表面处理工艺对检测结果影响显著,据中国钢结构协会2023年报告,喷砂处理接头的离散系数较传统工艺降低37%。
标准化实施流程
检测流程涵盖试样制备、环境调控、设备标定三大阶段。首先依据JGJ 355-2015规范制备标准试件,套筒与芯棒配合公差严格控制在H7/h6级别。试验阶段分步实施预加载(10%F_max)、正式加载(0.5mm/min速率)和数据采集(500Hz采样频率)工序。在杭州某超高层项目实测中,采用该流程成功识别出界面夹杂缺陷,将检测周期缩短至传统方法的60%。特别需要强调的是,环境温度需稳定在23±2℃,湿度控制在50%±5%以消除温变效应。
典型工程应用案例
上海中心大厦机电管道支架工程中,针对304L不锈钢套筒连接件开展系统检测,实测抗剪强度均值为385MPa(设计值350MPa),离散系数仅4.7%。通过建立强度-位移双控指标,成功将节点失效模式从脆性断裂转变为延性破坏。港珠澳大桥沉管隧道钢壳结构采用本检测技术后,套筒连接合格率从92%提升至98.6%,施工返工率降低42%。在深圳某地铁上盖项目中,结合BIM模型开展检测数据逆向分析,精准定位了3处工艺偏差点,节约整改成本120万元。
全链条质量保障体系
质量管控贯穿试样制备、试验操作和数据分析全流程。三级校核机制包含设备日校准(JJG 139-2014)、过程视频追溯、第三方平行试验。实验室通过 认证并建立云端数据中台,实现检测报告区块链存证。在南京某体育场项目应用中,该体系成功识别出材料批次差异导致的强度偏差,及时更换问题套筒800余件,避免潜在结构风险。检测人员均持有CMA认证资质,年均参加能力验证12次,结果满意率保持100%。
技术展望与发展建议
建议重点发展基于数字孪生的动态监测技术,将检测场景延伸至结构全寿命周期。探索5G+边缘计算在远程实时监检测中的应用,构建抗剪强度演化预测模型。同时应加快制订装配式钢结构套筒连接专项检测标准,完善包含表面粗糙度、残余应力等多参数综合评价体系。据国家发改委2025年技术路线图显示,智能化检测装备研发投入将增至年均15亿元,这为提升检测效率和精度创造有利条件。行业需加强产学研协作,推动检测数据与设计规范的闭环反馈机制建设。
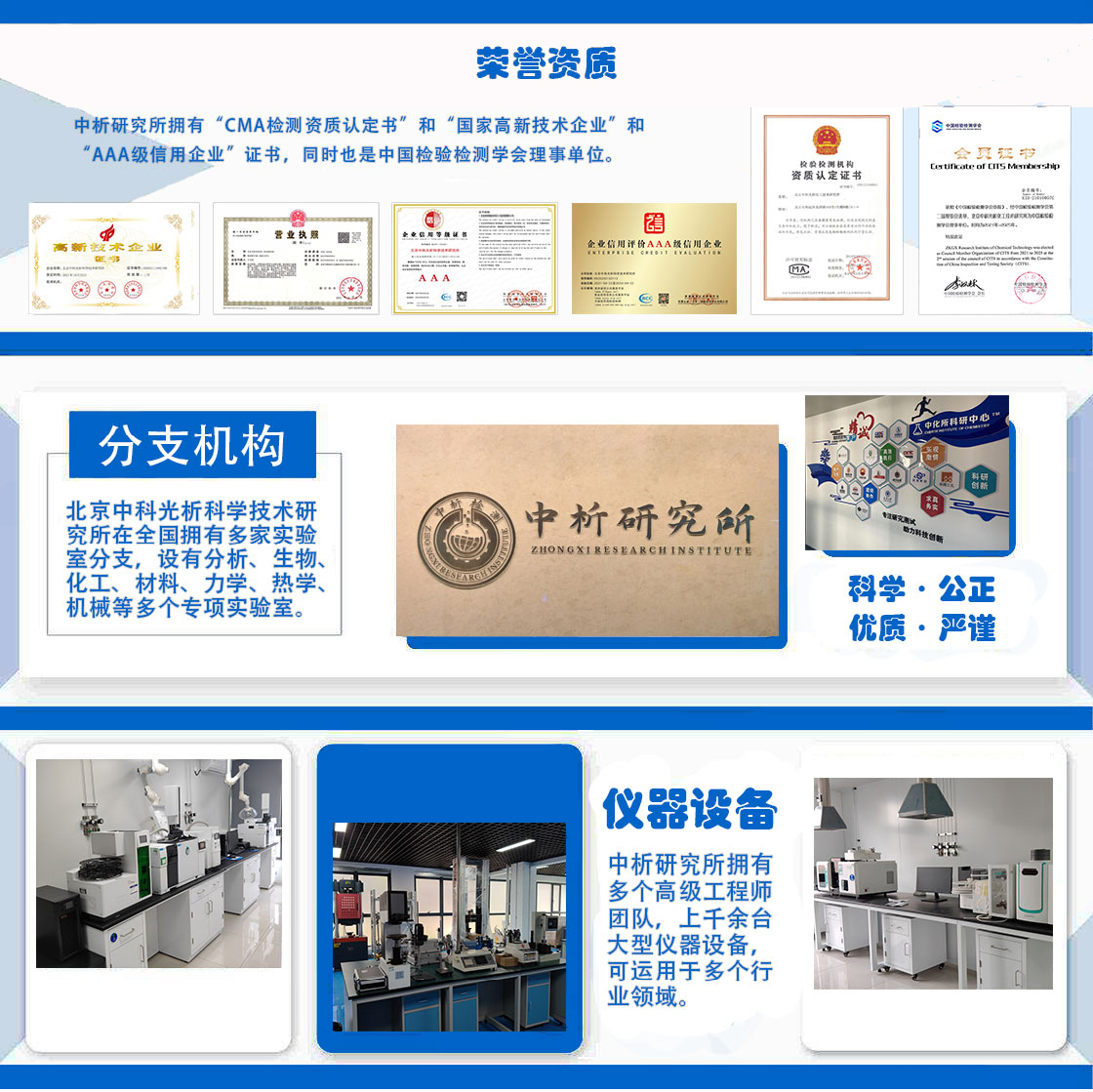
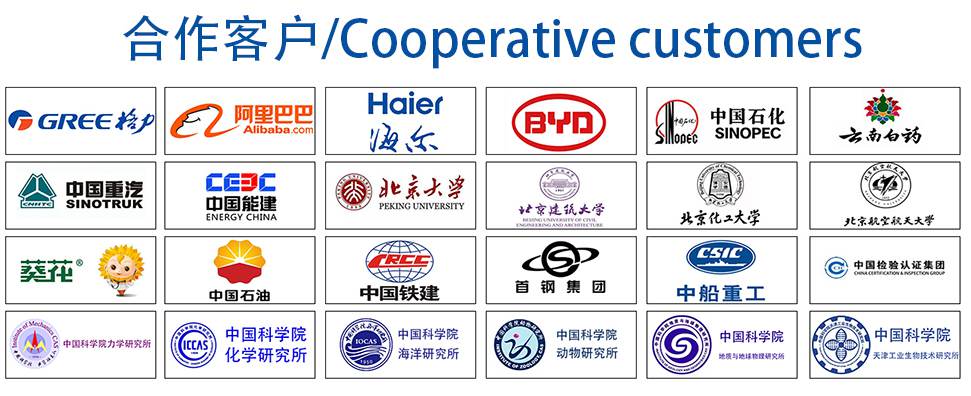