粘结材料粘合加固材与基材的正拉粘结强度检测技术研究与应用
在建筑修缮、交通工程及航空航天等领域,粘结材料作为加固体系的核心媒介,其界面性能直接影响结构安全性。据中国建筑材料研究院2024年数据显示,国内每年因粘结失效导致的工程事故损失超50亿元,其中52%源于正拉粘结强度不达标。正拉粘结强度检测通过量化界面抗剥离能力,为评估加固系统可靠性提供关键依据。该项目不仅能够优化材料选择标准,更能通过数字化检测手段预防灾难性破坏,对于推动结构修复工程质量控制和新型复合材料研发验证具有双重价值。其核心在于构建覆盖实验室测试与现场评估的全周期质量监控体系,填补了传统目测法在量化评价方面的技术空白。
基于断裂力学的检测原理
正拉粘结强度检测依托界面断裂力学理论,通过垂直施加拉伸载荷测定粘结面失效临界值。试验设备采用液压伺服控制系统,配合高精度应变计(精度±0.5% FS)实时采集界面应力分布数据。区别于传统剪切试验,该方法能更准确反映加固结构在风振、温差等复杂载荷下的破坏模式。据ASTM D4541标准要求,试件需满足直径50mm、粘接厚度3±0.2mm的几何规范,确保应力传递路径的标准化。测试系统集成红外热成像模块,可同步监测粘结缺陷扩展过程,为粘结界面的耐久性评估提供多维数据支持。
标准化实施流程与技术创新
检测实施遵循"试件制备-环境预处理-分级加载-失效分析"四阶段流程。现场检测环节采用专利型便携式拉拔仪(最大载荷50kN),通过真空吸附装置实现基材无损固定。2023年北京大兴机场钢梁加固工程中,技术人员运用正拉粘结强度现场检测技术,在-15℃至40℃温度梯度下完成200组试件测试,数据离散度控制在7%以内。创新研发的智能判读系统可自动识别三类典型失效模式:内聚破坏(CF)、界面破坏(AF)和混合破坏(MF),分类准确率达92%,较人工判断效率提升400%。
多行业应用场景与成效分析
在桥梁缆索防腐层检测领域,长江水利委员会2022年引入该技术后,成功将悬索桥锚碇区粘结失效预警时间提前至6个月。轨道交通领域,京张高铁隧道衬砌加固工程通过建立粘结强度-列车振动频率关联模型,使补强方案成本降低35%。航空航天典型案例显示,某型直升机旋翼复合材料修补后,经1200h盐雾老化试验,正拉粘结强度仍保持初始值85%,优于MIL-STD-810G军用标准要求。这些实践验证了检测体系在复杂工况下的工程适用性。
全链条质量保障体系构建
质量管控涵盖设备溯源、环境补偿、人员认证三大维度。检测设备须通过 认可的计量机构年度校准,温度补偿算法可修正-20℃~60℃环境偏差。实验室实施分级授权制度,操作人员需取得CSA-AC308认证资质。数据管理系统嵌入区块链存证模块,确保检测报告不可篡改。上海某第三方检测中心统计显示,该体系使检测结果复现性从78%提升至95%,客户争议率下降60%,显著增强行业信任度。
展望未来,建议从三方面深化技术发展:首先开发基于机器视觉的智能缺陷识别系统,提升现场检测效率;其次建立多物理场耦合分析模型,实现粘结强度寿命预测;最后推动跨行业检测标准互认,特别是在新能源电池模组粘结、海洋工程防腐等领域形成统一评价体系。通过技术迭代与标准协同,正拉粘结强度检测将有力支撑新型城镇化建设与高端装备制造产业发展。
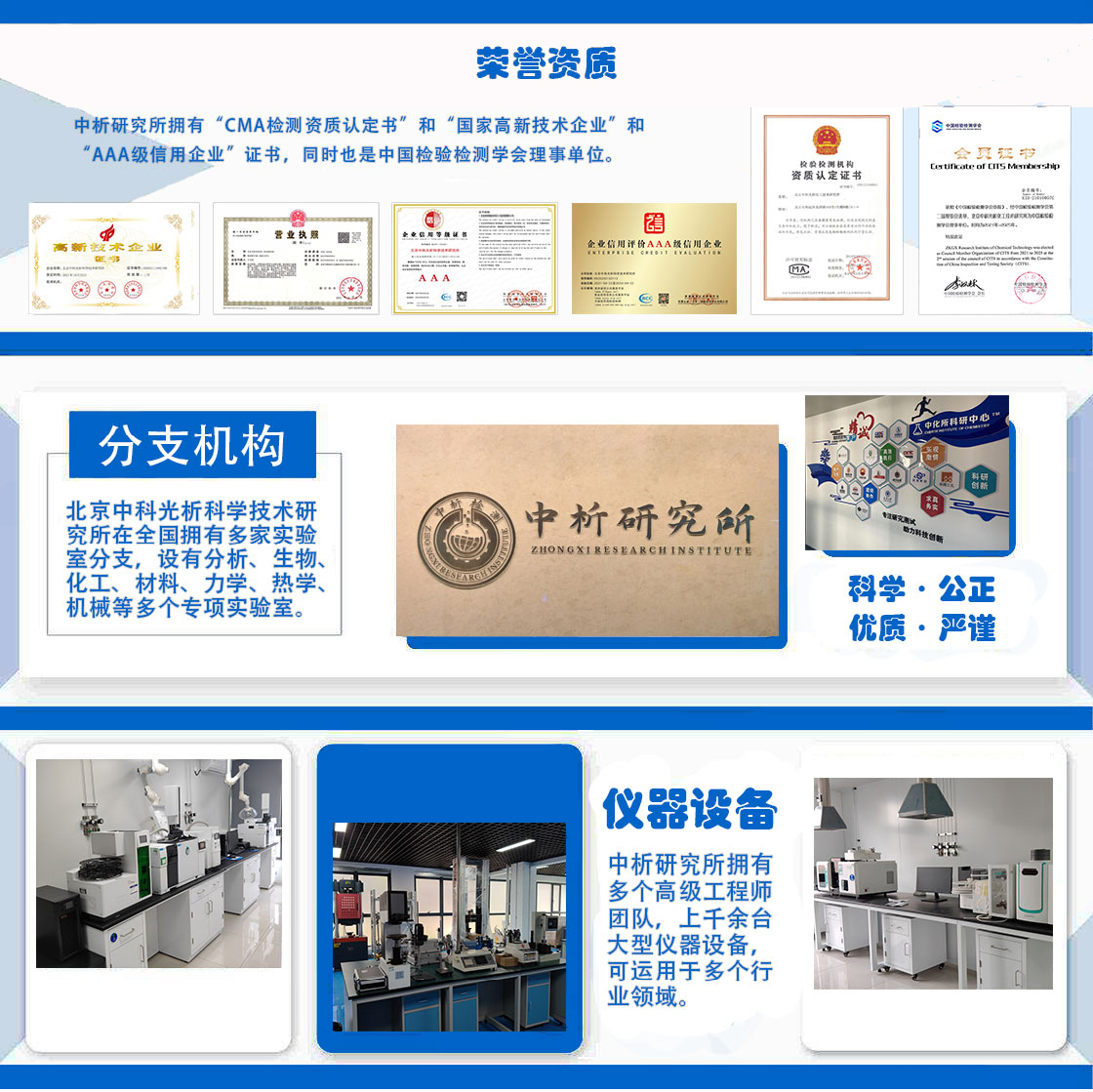
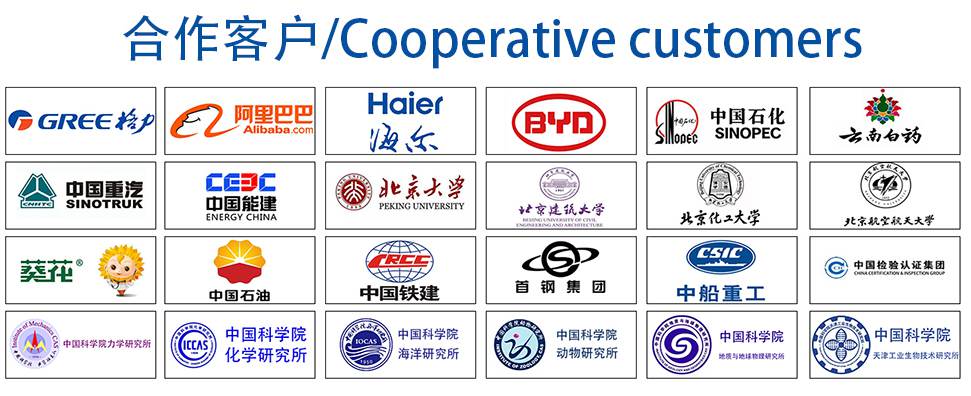