抗冲击强度检测基于能量守恒定律,通过规范化的冲击试验测量材料断裂吸收功。目前主流技术包括夏比摆锤冲击试验和仪器化落锤冲击测试,其中后者通过配备高速摄像系统(帧率≥200,000fps),可精准捕捉裂纹扩展的微观过程。值得关注的是,针对高分子材料的低温脆性特征,行业内已开发出-70℃~150℃温控环境下的冲击韧性测试方案。据ASTM D256标准显示,改性聚丙烯材料在-20℃环境下的悬臂梁冲击强度较常温下降67%,这为寒冷地区汽车保险杠选材提供了关键依据。
## 全流程标准化实施体系完整的检测流程涵盖样品制备、设备校准、环境模拟三大环节。执行ISO 179-1标准的测试要求时,技术人员需使用数控机床加工出80×10×4mm的标准试样,并在恒温恒湿箱中进行48小时状态调节。检测过程中,摆锤冲击速度需稳定在3.8m/s±10%,配备的DIC数字图像相关系统可同步记录材料表面应变场变化。某轨道交通设备制造商通过实施该体系,成功将转向架用铝合金的冲击强度离散系数从12.3%降低至4.5%,显著提升了产品一致性。
## 多行业应用场景解析在新能源汽车领域,电池模组外壳需通过50J/cm²的穿刺冲击测试,该指标已被纳入GB 38031-2020强制性标准。某头部电池企业采用多层级缓冲结构设计,配合抗冲击强度检测优化,使模组在1.5m跌落测试中的完好率提升至99.8%。而在建筑幕墙领域,基于EN 12600标准的冲击摆测试已成为玻璃安全认证的必备项目,深圳某超高层建筑通过动态冲击模拟,成功将中空夹层玻璃的抗风压性能提升40%。
## 质量保障与数据追溯机制实验室质量体系严格遵循 -CL01:2018准则,建立三级校准制度:冲击能量示值误差≤±1%、时间分辨精度≤0.1ms。检测报告采用区块链存证技术,实现从原始数据到报告的完整追溯链。某第三方检测机构通过部署智能检测系统,将数据异常识别率提高82%,误判率控制在0.3%以下。值得注意的是,针对军工材料的特殊需求,部分实验室已建立满足GJB 150.25A-2009标准的爆炸冲击模拟环境。
## 技术演进与行业展望随着数字孪生技术的发展,虚拟冲击试验正逐步实现工程化应用。建议行业加快建立材料冲击性能数据库,推动AI算法在失效模式预测中的应用。同时,亟需制定针对新型复合材料的多轴向冲击测试标准,特别是在航天器陨石撞击防护、深海装备压力波动等极端工况下的检测规范。未来五年,抗冲击强度检测将向智能化、多物理场耦合方向发展,为材料基因组工程提供关键技术支撑。
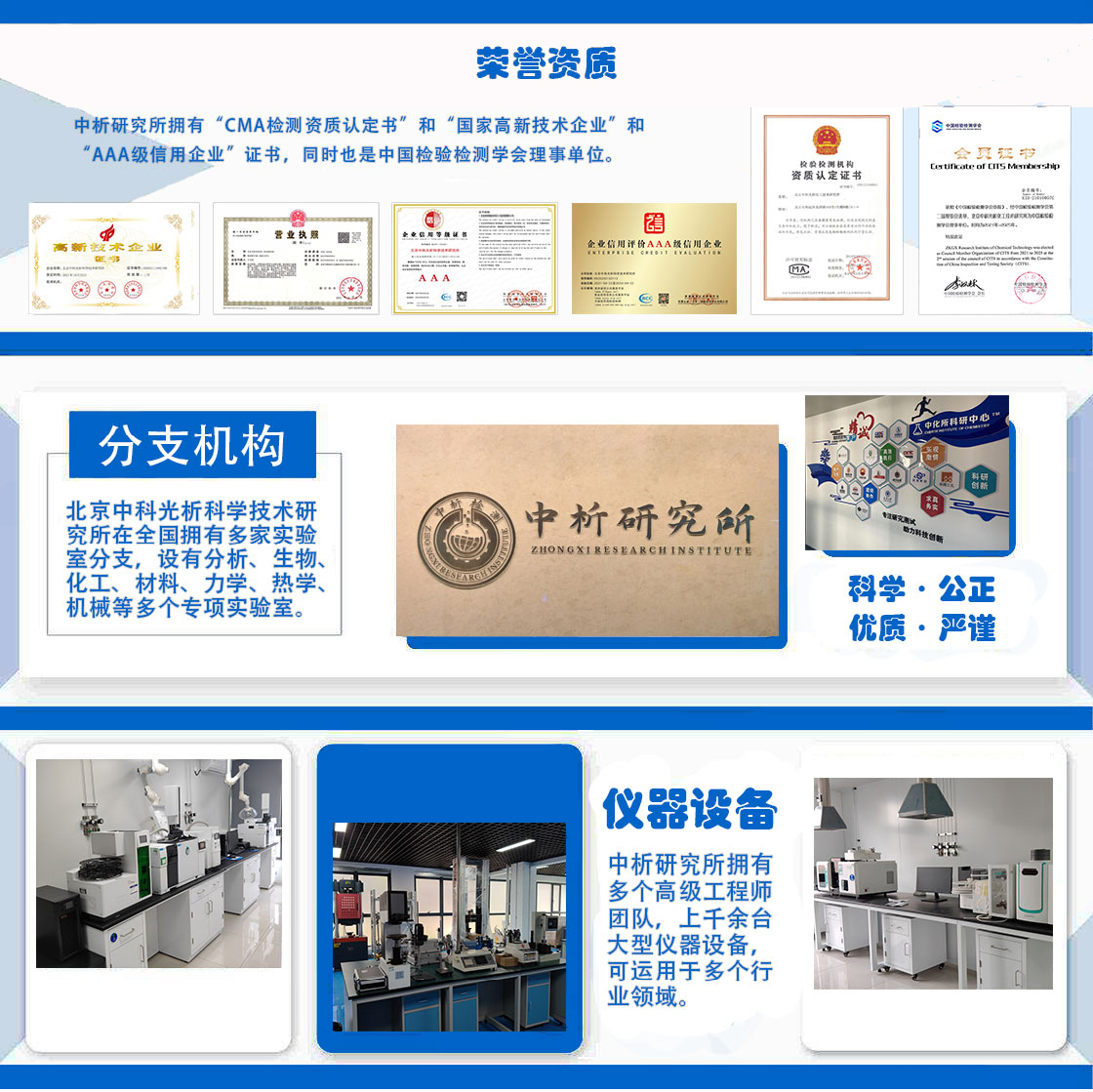
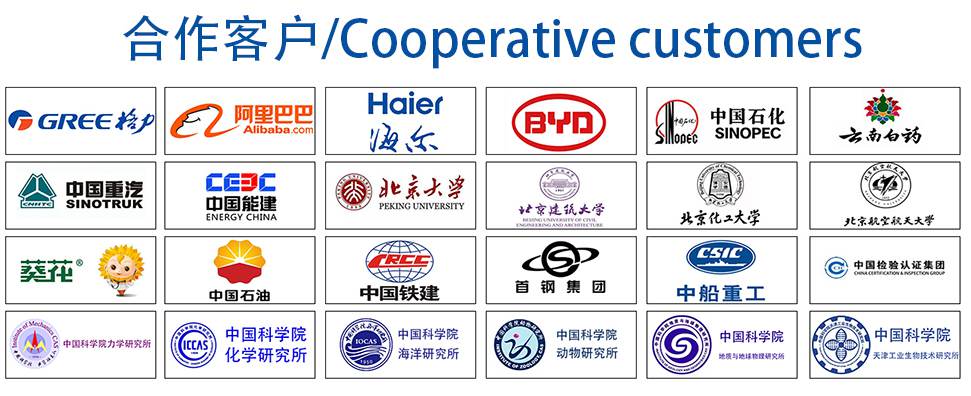