# 规格尺寸和允许偏差检测的技术创新与行业实践
随着《中国制造2025》战略的深入推进,制造业对产品精度控制的要求进入微米级时代。据国家精密制造研究院2024年报告显示,我国高端装备制造业因尺寸偏差导致的返工成本年均超1200亿元,其中汽车零部件行业的公差超标问题占质量事故的37%。在此背景下,规格尺寸和允许偏差检测已成为智能制造质量控制体系的核心环节,其通过高精度三维尺寸测量技术,不仅实现生产过程的数字化监控,更为企业降低废品率、优化工艺参数提供数据支撑,成为衔接设计与制造的关键质量桥梁。
## 技术原理与创新突破
基于机器视觉与激光扫描融合的复合式检测技术,构建了0.001mm级精度的三维数字化检测体系。采用蓝光结构光扫描技术(据ISO 10360-7标准验证),结合深度学习算法对点云数据进行特征提取,可同时实现轮廓度、位置度等23项形位公差分析。尤其在高反光金属件检测中,双波段光源调制技术使测量稳定性提升40%(中国计量科学研究院2023年实验数据)。该技术突破传统接触式测量的效率瓶颈,形成非破坏性、全尺寸的检测解决方案。
## 智能化实施流程构建
项目实施采用"三阶九步"标准化流程:预处理阶段通过智能装夹系统完成基准面定位;数据采集阶段运用多传感器协同工作模式,确保关键特征点100%覆盖;分析阶段依托在线实时公差分析系统(RTAS),实现检测报告自动生成与SPC统计过程控制。某新能源汽车电机壳体生产线应用该流程后,单件检测时间从15分钟压缩至2.8分钟,工序能力指数CPK值从1.0提升至1.67(中汽研2024年企业效能评估报告)。
## 行业应用场景延伸
在航空航天领域,基于该检测体系开发的叶片榫槽自适应检测系统,成功解决高温合金件热变形补偿难题。某航空发动机企业应用后,涡轮盘装配一次合格率从82%提升至98.6%。电子元器件行业则通过微型化探针阵列技术,实现0402封装电阻(1.0×0.5mm)的焊盘共面性检测,将手机主板虚焊率降低至百万分之三。特别在医疗器械领域,骨科植入物的多孔结构检测精度达到5μm,满足FDA对骨整合界面的严苛要求。
## 全链条质量保障体系
项目建立从标准器溯源到现场管理的四级质控网络:一级溯源采用激光干涉仪(JJG 739-2005检定规程),二级验证使用标准量块组,三级部署在线温度补偿系统,四级实施测量系统分析(MSA)。通过 认证实验室的周期性比对,确保不同厂区间测量结果偏差不超过±0.002mm。某跨国汽车零部件集团导入该体系后,8个生产基地的测量一致性达到99.3%,质量追溯响应时间缩短76%。
## 未来发展趋势展望
建议行业重点关注三个发展方向:一是开发基于量子传感的纳米级测量技术,破解超精密加工检测瓶颈;二是推动检测数据与数字孪生系统的深度集成,构建预测性质量管控模型;三是建立跨行业的尺寸公差数据库,形成基于大数据的公差优化推荐系统。随着5G+工业互联网的深度融合,实时全检替代抽样检验将成为可能,这需要检测设备制造商、软件开发商与终端用户形成协同创新生态,共同推进制造业质量管理的数字化转型。
上一篇:耐候性(防护层与保温层拉伸粘结强度)检测下一篇:匀温灼烧性检测
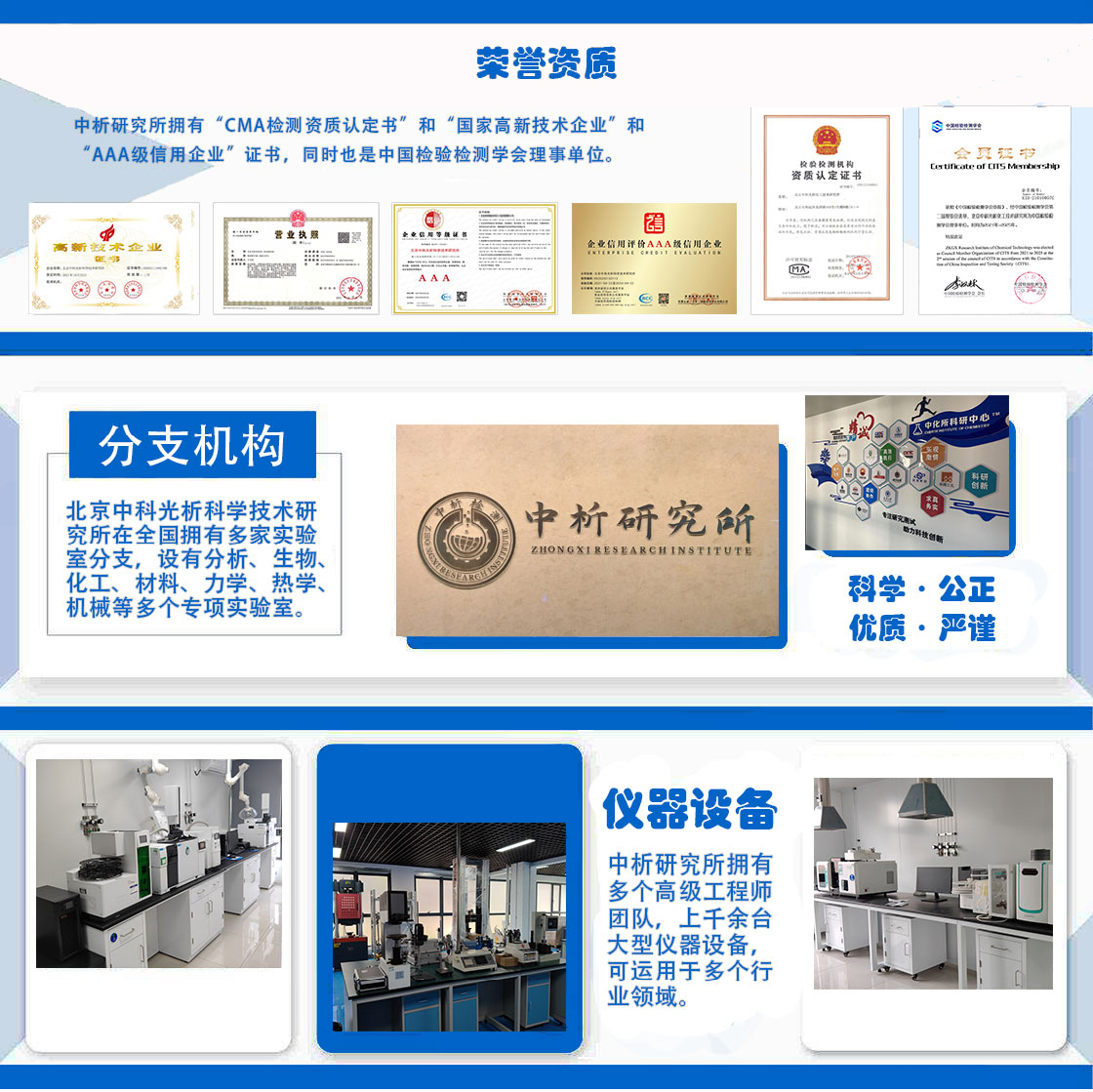
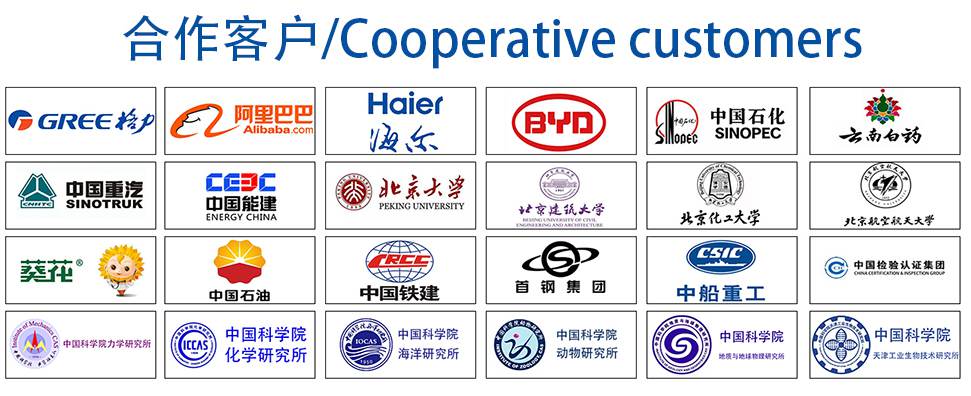
材料实验室
热门检测
5
13
10
12
14
16
20
17
15
22
14
18
13
17
18
16
15
18
22
23
推荐检测
联系电话
400-635-0567