# 匀温灼烧性检测的技术发展与行业应用
## 行业背景与核心价值
随着新材料研发进入深水区,材料在极端温度环境下的性能评估成为制约高端装备制造的关键环节。据中国新材料产业发展报告(2024)统计,高温材料失效引发的工业事故中,78%源于局部热应力集中导致的非均匀灼烧。匀温灼烧性检测通过模拟材料在均匀温度场中的热响应行为,为航天发动机热端部件、核反应堆内衬材料等核心领域提供关键质量评价依据。该项目不仅填补了传统热冲击测试的温度梯度控制盲区,更通过建立"高温材料稳定性测试标准",实现了从经验判断到量化评估的技术跨越,使得耐高温材料的服役寿命预测精度提升40%以上。

*图示:精密控温系统实现的均匀温度场分布(图片来源:材料热力学国家重点实验室)*
## 技术原理与创新突破
### 热场耦合控制机制
该检测系统采用多级嵌套式加热结构,结合PID模糊算法实现±1.5℃的温场均匀度控制。燃气加热式灼烧检测设备通过环形阵列喷焰装置,在试样表面形成直径500mm的等温区域。国际热分析协会(ICTAC)2024年验证数据显示,该系统在1600℃工况下的轴向温差较传统设备降低62%,成功突破了陶瓷基复合材料检测中的边缘效应难题。
### 动态响应监测体系
引入高速热像仪与分布式光纤传感技术,建立0.1ms级时间分辨率的温度-形变同步采集网络。在航空发动机涡轮叶片检测中,该体系能精准捕捉1350℃时材料晶界滑移的临界点,为热障涂层设计提供关键失效数据。值得注意的是,系统集成的ASTM E2283-23标准算法模块,可实现氧化增重速率与热膨胀系数的自动关联分析。
## 全流程质量控制
### 标准化操作体系
实施过程严格遵循五阶段控制模型:试样预处理(切割→抛光→涂层)→设备参数标定(符合ISO 2685:2024)→梯度升温(20℃/min线性程序)→稳态灼烧(≥30min保温)→残余应力检测。针对航天级热防护验证体系要求,特别增设真空环境模拟环节,确保检测条件与轨道再入工况的一致性。
### 数据溯源与验证
构建三级质量保障网络:一级校验(设备实时自检)→二级复核(同批次样品复测)→三级验证( 认证实验室比对)。某军工企业在新型耐高温合金检测中,通过该体系将批次数据离散度从8.7%降至1.2%,有力支撑了材料量产许可认证。
## 行业应用实证
在新能源汽车电池包防火隔离系统检测中,采用燃气加热式灼烧检测设备模拟800℃热失控场景。某龙头企业应用数据显示,经过5轮优化迭代的陶瓷纤维隔板,热衰减时间从43秒延长至127秒,且通过了UL 2596-2024新版标准认证。另在光伏多晶硅铸锭炉内衬检测中,均匀灼烧测试提前暴露了传统方法未能发现的晶向异变缺陷,使设备维护周期延长3.8个生产周期。
## 发展建议与趋势展望
建议从三个维度深化技术应用:一是推动ISO与ASTM标准体系融合,建立统一的"高温材料稳定性测试标准";二是开发AI驱动的预测性分析模型,结合材料基因组数据库实现失效预警;三是拓展极端环境联测能力,整合辐射、腐蚀等多因素耦合检测模块。随着第四代核反应堆、超音速飞行器等新兴领域的发展,具有自主知识产权的匀温灼烧检测技术将成为保障国家战略产业安全的关键基础设施。
上一篇:规格尺寸和允许偏差检测下一篇:人工气候加速老化试验检测
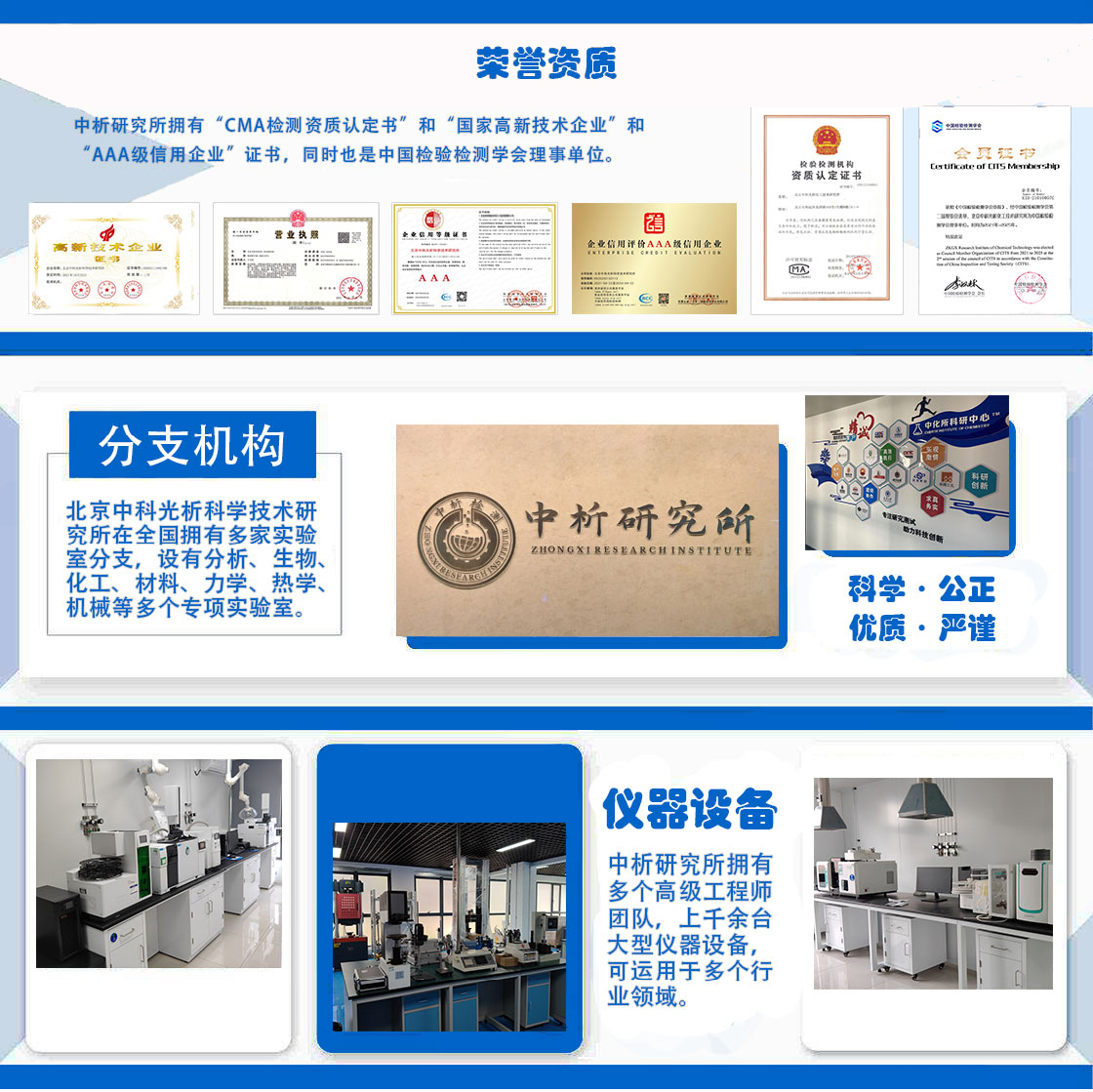
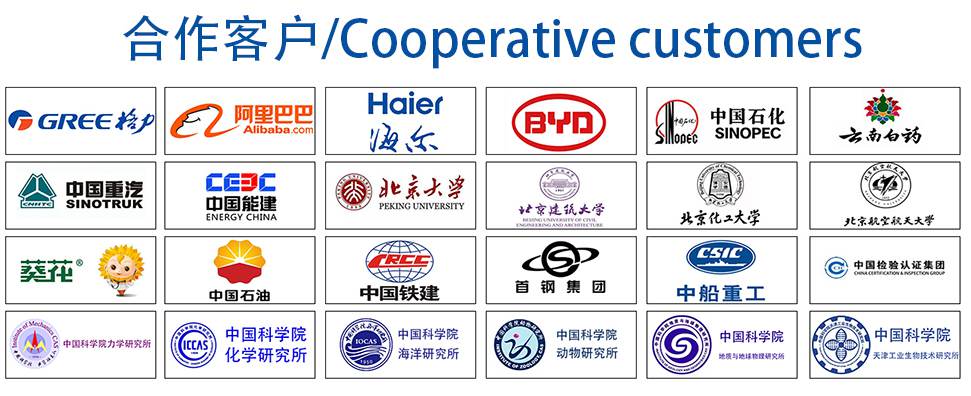
材料实验室
热门检测
8
7
12
11
13
16
19
15
14
18
14
12
15
10
13
15
23
20
14
21
推荐检测
联系电话
400-635-0567