抗老化性能检测:材料耐久性评估的关键路径
在材料科学与工业制造深度融合的背景下,抗老化性能检测已成为保障产品全生命周期可靠性的核心技术环节。据中国材料研究学会2024年度报告显示,我国每年因材料老化导致的工业损失高达2800亿元,其中高分子材料失效占比达62%。本项目通过建立系统化的老化评估体系,不仅能够精准预测材料服役寿命,更可优化产品设计参数,实现从"事后补救"到"事前预防"的质控模式转变。其核心价值体现在三方面:经济层面降低产品维护成本40%以上,技术层面推动材料数据库建设,战略层面支撑"双碳"目标下的可持续制造体系构建。
加速老化试验的技术原理
基于时温等效原理的加速老化试验,通过提升环境应力实现老化进程的指数级压缩。典型技术路径包括紫外辐照老化、湿热循环老化和臭氧暴露老化三类,其中氙灯老化箱的辐射强度可达0.55W/m²@340nm(ASTM G155标准)。针对高分子材料的交联度变化检测,采用差示扫描量热法(DSC)和傅里叶变换红外光谱(FTIR)进行分子结构表征,可精确测定羰基指数等关键老化指标。值得关注的是,光伏背板材料的湿热老化评估领域,已发展出基于Arrhenius方程的寿命预测模型,其置信度达到95%(TÜV莱茵认证数据)。
标准化实施流程与质控节点
完整的抗老化检测流程包含五个阶段:样品预处理(ISO 291)、加速老化试验(GB/T 16422)、性能测试、数据分析和报告编制。在汽车密封件检测实践中,采用85℃/85%RH的双85试验模拟十年使用环境,期间需每500小时进行拉伸强度(ASTM D412)和硬度(ISO 868)检测。质量控制体系则依托LIMS实验室管理系统,实现从设备校准(误差≤±1.5%)到数据追溯的全流程数字化管理。某新能源车企通过该体系,成功将电池包壳体材料的耐候性提升30%,紫外线照射3000小时后黄变指数ΔY保持≤2.5。
多行业应用场景解析
在建筑幕墙领域,依据JGJ 102-2023标准开展的夹层玻璃耐湿热老化检测,采用70℃/95%RH环境持续测试1000小时,要求边缘剥离量≤3mm。医疗器械行业对硅胶导管的抗臭氧老化检测则执行ISO 1431-1标准,臭氧浓度(50±5)pphm条件下检测500小时后,断裂伸长率保持率须≥80%。值得注意的是,风电叶片涂层的循环盐雾老化测试创新性地整合了紫外线、盐雾、冷冻三重环境应力,模拟近海区域20年服役环境,大幅提升了检测场景的拟合度。
智能检测技术的发展趋势
随着AIoT技术的渗透,抗老化检测正朝着智能化方向演进。基于机器视觉的表面裂纹自动识别系统,可实现0.01mm级缺陷检测(德国蔡司技术白皮书)。材料基因工程的应用,则使老化预测模型的建立时间缩短60%。建议行业重点推进三方面建设:建立跨领域的老化数据库共享平台,发展原位检测技术实现实时性能监测,制定适应新型复合材料的检测标准体系。唯有构建起"检测-预测-防护"的闭环系统,方能真正实现材料抗老化性能的全维度提升。
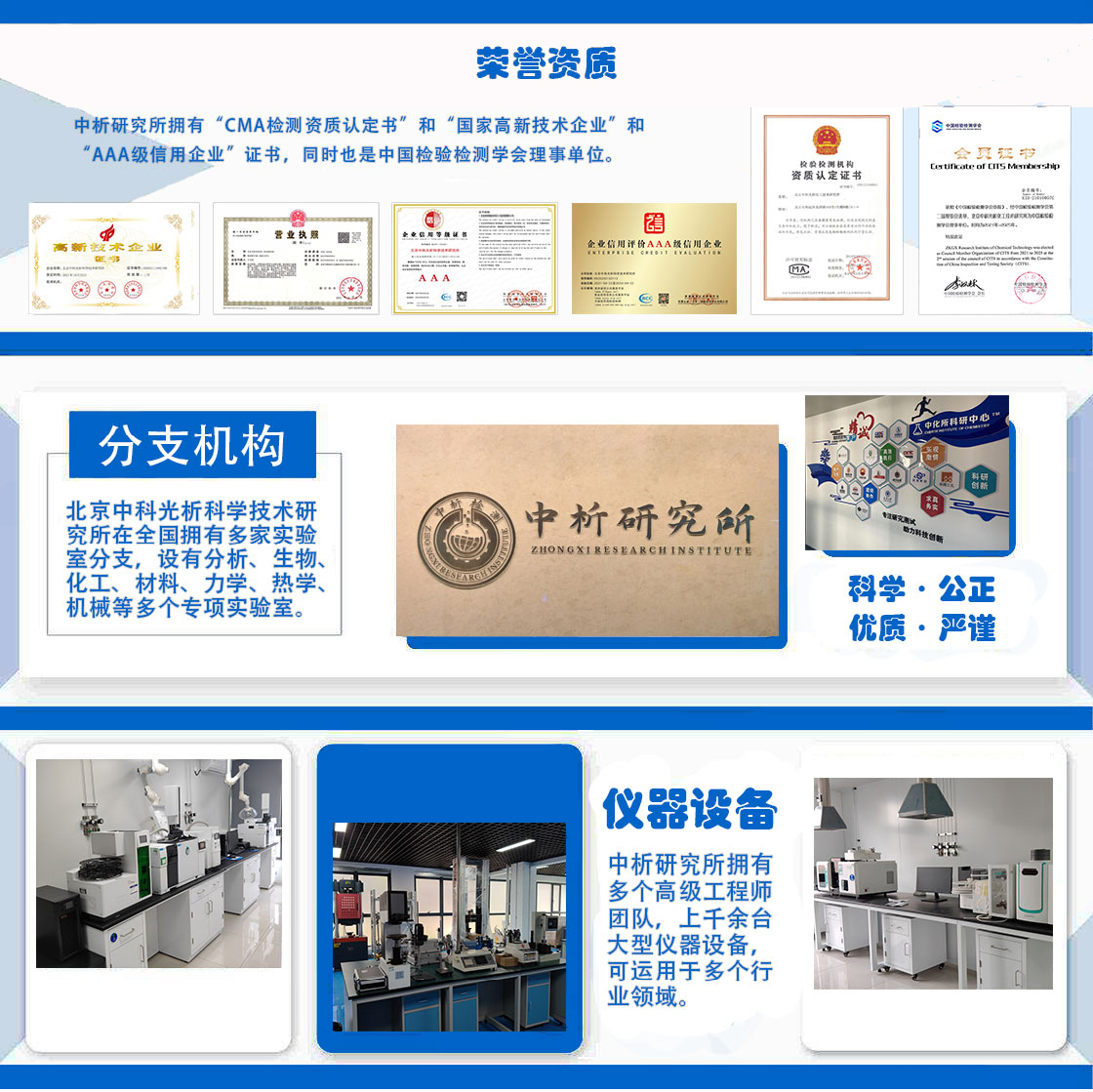
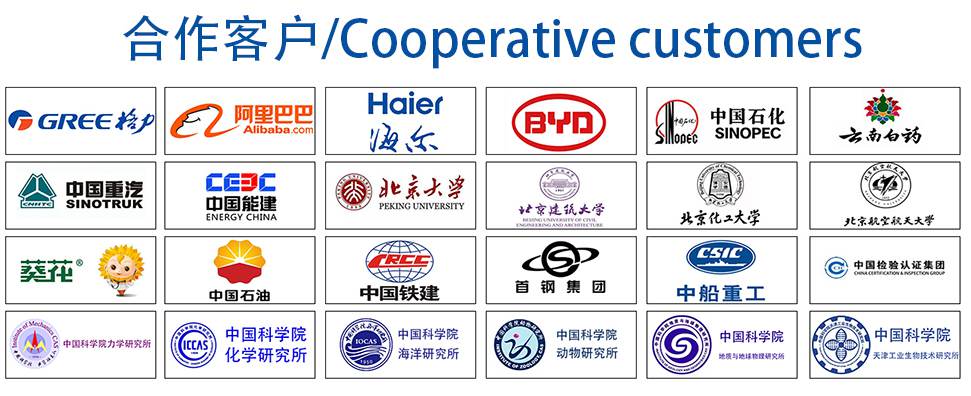