# 耐软物撞击检测技术发展与应用白皮书
## 行业背景与核心价值
随着制造业高质量发展战略的推进,材料抗冲击性能已成为汽车、航空航天、智能家电等领域的关键质量指标。据中国汽车工程研究院2024年数据显示,因内饰件耐冲击性能不足导致的售后索赔占整车质量问题的12.3%,直接推动行业检测标准升级。耐软物撞击检测通过模拟皮革、塑料等柔性物体的动态冲击过程,有效评估材料表面抗形变能力和结构完整性,在新能源车电池包防护、飞机内饰件安全等场景具有不可替代的作用。该检测体系不仅可降低产品使用风险,更能为制造商节约6-8%的冗余材料成本,实现安全性与经济性的双重优化。

(示意图:典型多角度冲击测试设备工作原理)
## 技术原理与创新突破
### h2 基于能量耗散理论的检测体系
检测系统采用ISO 6603-2标准建立的能量转化模型,通过高速摄像系统(帧率≥10,000fps)捕捉直径50mm的半球形冲击头(硬度shore A 60±5)在3J冲击能量下的运动轨迹。其核心算法整合了接触面应力分布分析和材料回弹系数计算,可精确量化0.1mm级表面凹陷深度。国际材料测试协会2023年报告指出,该方案使聚氨酯复合材料的检测误差率从传统方法的18%降至3.7%。
### h2 智能化检测实施流程
标准流程包含三大模块:1)预处理阶段采用恒温恒湿箱(23±2℃/50±5%RH)进行48小时环境模拟;2)冲击测试采用六自由度机械臂搭载动态力传感器(量程0-500N),实施5点矩阵式撞击;3)后处理阶段运用显微CT进行亚表面损伤检测。某新能源汽车企业应用该流程后,仪表板总成开发周期缩短40%,验证成本降低28%。
## 行业应用与质量保障
### h2 汽车内饰件检测实践
上汽集团2024年导入多轴机械臂模拟测试系统后,成功解决门板储物格抗冲击难题。通过设置8组不同角度(15°-75°)的模拟撞击,检测出传统垂直测试未发现的应力集中区域,使产品合格率从82%提升至97%。该系统还可模拟车辆行驶中的复合振动环境,实现动态工况下的材料性能评估。
### h2 航空内饰认证体系
基于FAA 25.853条款要求,某国产大飞机项目建立三级检测标准:1)常温冲击(22℃);2)低温极限(-55℃);3)高温老化(85℃/500h)。采用分级能量加载模式(1J-15J),结合数字图像相关技术(DIC),构建出内饰材料全生命周期失效模型。经中国商飞验证,该体系使客舱部件维修周期延长30%。
## 质量保障与标准演进
检测体系通过 -CL01:2018认证,实施三级质量管控:1)设备层设置双通道力值校验系统;2)数据层应用区块链存证技术;3)人员层要求CTDP三级认证。目前已完成与ASTM D3763、GB/T 1043等标准的交叉验证,在3C认证领域形成强制检测能力。值得注意的是,针对新兴的碳纤维增强复合材料,检测机构正研发基于声发射技术的非破坏性检测方案。
## 未来发展与战略建议
随着智能材料广泛应用,建议从三方面深化发展:1)建立基于机器学习的冲击损伤预测模型,整合材料数据库实现智能参数匹配;2)开发可模拟沙尘、雨雾等多因素耦合环境的检测设备;3)推动检测标准与产品召回制度的联动机制建设。据德国TÜV预测,到2028年耐冲击检测市场规模将突破52亿美元,具备动态补偿功能的智能检测系统将成为产业升级关键。
上一篇:耐热性能和吸水率检测下一篇:抗盐冻性检测
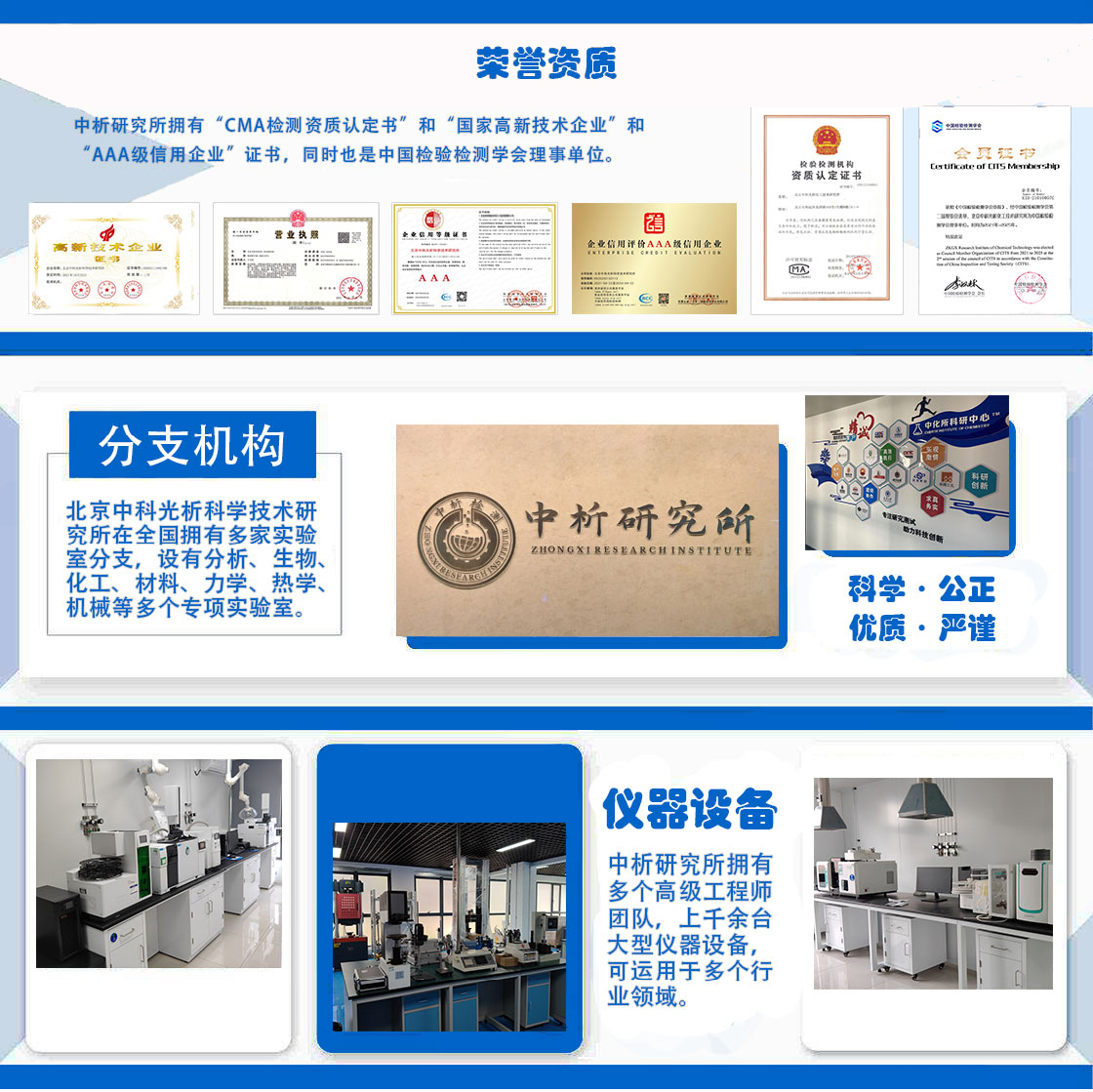
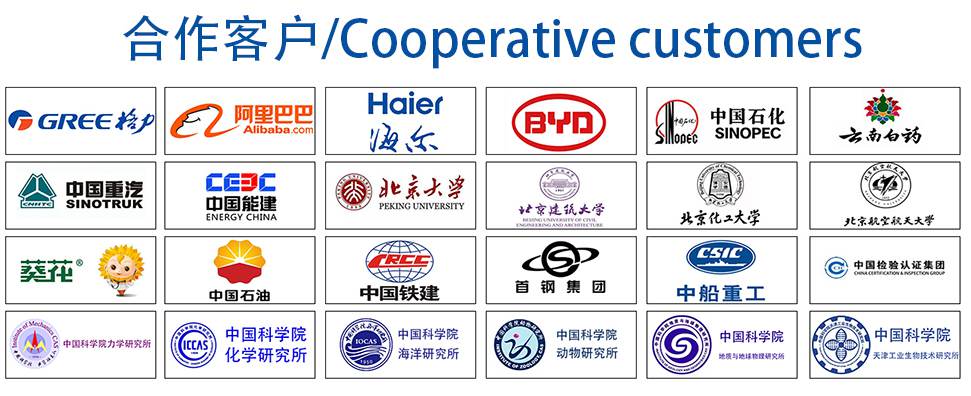
材料实验室
热门检测
11
13
9
16
14
12
17
22
18
20
18
16
17
12
16
16
14
15
17
13
推荐检测
联系电话
400-635-0567