放电电流控制检测的关键项目解析
一、基础参数检测
-
- 检测内容:对比传感器(如霍尔传感器、分流器)的采样值与高精度标准仪器(如安捷伦万用表)的测量值。
- 关键指标:误差需≤1%(高精度场景要求≤0.5%),采样频率≥1kHz以确保动态捕捉能力。
- 测试方法:通过可编程电子负载模拟不同放电工况,记录BMS反馈值与真实值的偏差。
-
- 验证策略:设定目标电流(如100A)后,检测系统能否长期稳定在设定值,波动范围是否达标(如±2%)。
- 应用场景:储能系统需通过72小时连续放电测试,验证无漂移问题。
二、动态性能测试
-
- 测试条件:电流从10A瞬间切换至200A(或满负荷),记录系统调整至目标值的时间(典型值<50ms)。
- 评判标准:超调量需<5%,避免对电池造成冲击。
-
- 模拟场景:周期性或随机性负载变化(如变频驱动的电机),分析电流跟踪能力。
- 工具:使用双向直流电源模拟动态负载,搭配示波器观测波形稳定性。
三、异常工况保护检测
-
- 分级保护测试:逐级触发不同阈值的过流(如120%、150%额定电流),验证硬件保护电路与软件逻辑的协同响应时间(典型值<10ms)。
- 失效模式分析(FMEA):注入超出设计范围的电流(如200%),确保熔断器或MOSFET能可靠切断回路。
-
- 瞬时短路测试:在输出端制造硬短路(电阻<1mΩ),记录保护动作时间(需<5ms)。
- 软短路测试:模拟线路绝缘失效导致的渐变短路,验证系统预测能力。
四、环境与系统级测试
-
- 温箱测试:在-30℃至65℃范围内,验证电流传感器和控制算法的温度补偿能力。
- 案例:低温下电解液阻抗增加,可能导致实际输出电流低于设定值,需修正控制策略。
-
- 并联系统检测:在电池组并联场景中,监测各支路电流差异(要求<5%),避免环流问题。
- 解决方案:通过动态调整MOSFET的导通电阻或采用主从控制器同步策略。
五、通信与安全机制验证
-
- 模拟通信中断:切断BMS与主控单元的CAN总线,检测系统是否切换至硬件保护模式。
- 数据完整性:校验电流数据的CRC校验机制,防止传输错误导致误判。
-
- 双传感器交叉校验:当主传感器失效时,备用传感器能否无缝接管,并触发预警信号。
- 案例:航空航天领域要求三重冗余,需模拟两路传感器同时故障的极端情况。
六、长期稳定性与寿命测试
-
- 累计循环次数:模拟电池全生命周期(如2000次充放电),定期检测电流控制精度衰减情况。
- 关键参数:重点关注MOSFET导通电阻的变化对功耗的影响。
-
- 85℃/85%RH环境测试:持续500小时后,检测PCB板是否腐蚀导致采样电阻漂移。
检测标准与工具推荐
- 标准参考:
- 电动汽车:ISO 12405-3、GB/T 31486
- 工业储能:IEC 62619、UL 1973
- 工具清单:
- 高精度电流源:Keysight B2900系列
- 高速数据采集卡:National Instruments PXIe-5162
- 环境模拟箱:ESPEC PVS-3系列
转成精致网页
上一篇:输入和输出之间的隔离电阻检测下一篇:高温下的截止电流检测
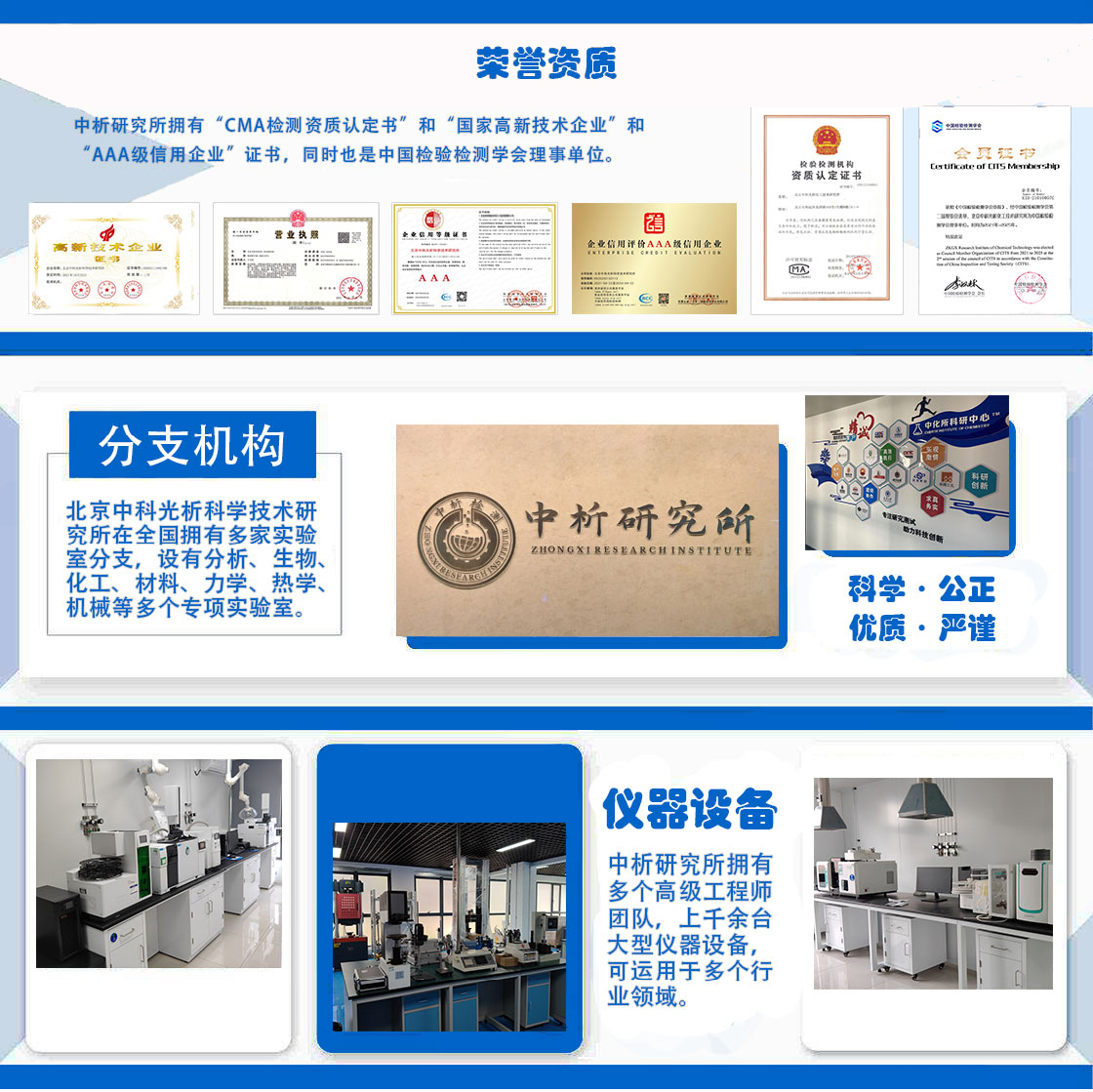
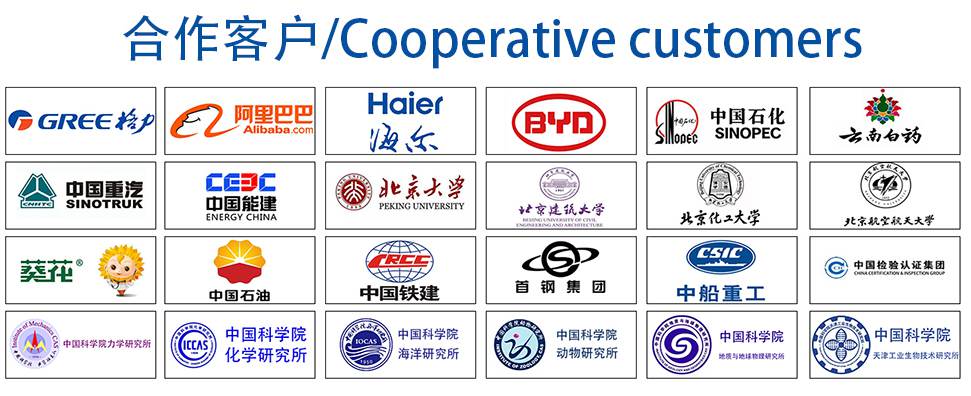
材料实验室
热门检测
6
7
6
8
13
15
10
13
13
12
13
13
16
16
14
13
13
12
12
14
推荐检测
联系电话
400-635-0567