耐热性能与吸水率检测技术白皮书
在工业制造与材料科学领域,材料的热稳定性和水分吸附特性直接决定产品可靠性。据中国材料测试协会2024年报告显示,每年因材料热失效导致的经济损失达430亿美元,而电子元件领域因吸湿膨胀引发的故障占比达27%。耐热性能和吸水率检测作为材料基础性能评价的双核心指标,不仅关系到产品全生命周期管理,更是实现"双碳"目标下节能降耗的关键技术路径。该项目通过建立标准化检测体系,可精准预判材料在高温高湿环境中的行为特征,为新能源汽车电池封装、5G通讯设备防护等战略产业提供数据支撑,其核心价值体现在降低研发试错成本40%以上(国家新材料产业数据中心,2023)。
检测技术原理与实施规范
基于ASTM D648和ISO 75标准构建的热变形温度测试系统,采用三点弯曲法测定材料在1.82MPa载荷下的热变形临界值。同步结合TGA热重分析仪,可捕捉材料在程序控温过程中的质量变化曲线。吸水率检测则依据ISO 62标准实施,运用恒温恒湿箱模拟材料在23℃/50%RH标准环境下的质量增量,并通过精密电子天平实现±0.1mg级测量精度。对于特殊应用场景如海底电缆防护层,需执行85℃/85%RH加速老化测试,该复合检测方案可有效评估"高温高湿协同作用下的材料性能衰减"。
全流程质量管控体系
检测流程涵盖样件制备、环境驯化、仪器标定等12个质量控制节点。在新能源汽车电机绝缘系统检测中,样件需经48小时环境平衡处理,使用氮气保护的热分析仪消除氧化干扰。实验室配备二级标准砝码追溯系统,确保测量结果可溯源至国家计量基准。据国家质检总局2023年度报告,通过 认证的实验室在"塑料制品吸水性评估标准"项目中的检测一致性达到98.7%,显著高于行业平均水平。
行业典型应用场景
在光伏组件封装领域,双玻组件的POE胶膜需通过2000小时85℃/85%RH双85测试,其吸水率必须控制在0.5%以内(TÜV莱茵认证标准)。某龙头企业引入动态吸附分析仪后,封装材料选型效率提升60%,年减少户外失效案例230起。医疗级聚碳酸酯器械外壳的检测则需满足ISO 10993生物相容性要求,通过"高温蒸汽灭菌后的尺寸稳定性测试",将吸水率阈值设定为0.3%以下,确保20次灭菌循环后仍保持力学性能。
技术创新与发展建议
当前检测技术正向智能化方向发展,如基于机器视觉的热变形自动判读系统,可将检测效率提升3倍。建议行业着力构建材料数据库共享平台,打通"高温环境材料稳定性测试"数据壁垒。同时推动ASTM与ISO标准在湿热耦合测试方法上的融合,预计到2026年可形成覆盖90%工程塑料的检测标准体系(中国标准化研究院预测数据)。
展望未来,随着新型相变材料和超疏水涂层技术的突破,检测维度需向纳米级界面表征延伸。建议产学研机构联合开发多场耦合检测设备,实现温度-湿度-应力多参数协同分析。据前瞻产业研究院测算,齐全材料检测市场规模将于2028年突破千亿美元,其中耐候性检测占比将提升至35%,这要求检测机构加快布局AI辅助决策系统和数字孪生验证平台,以应对日趋复杂的材料应用挑战。
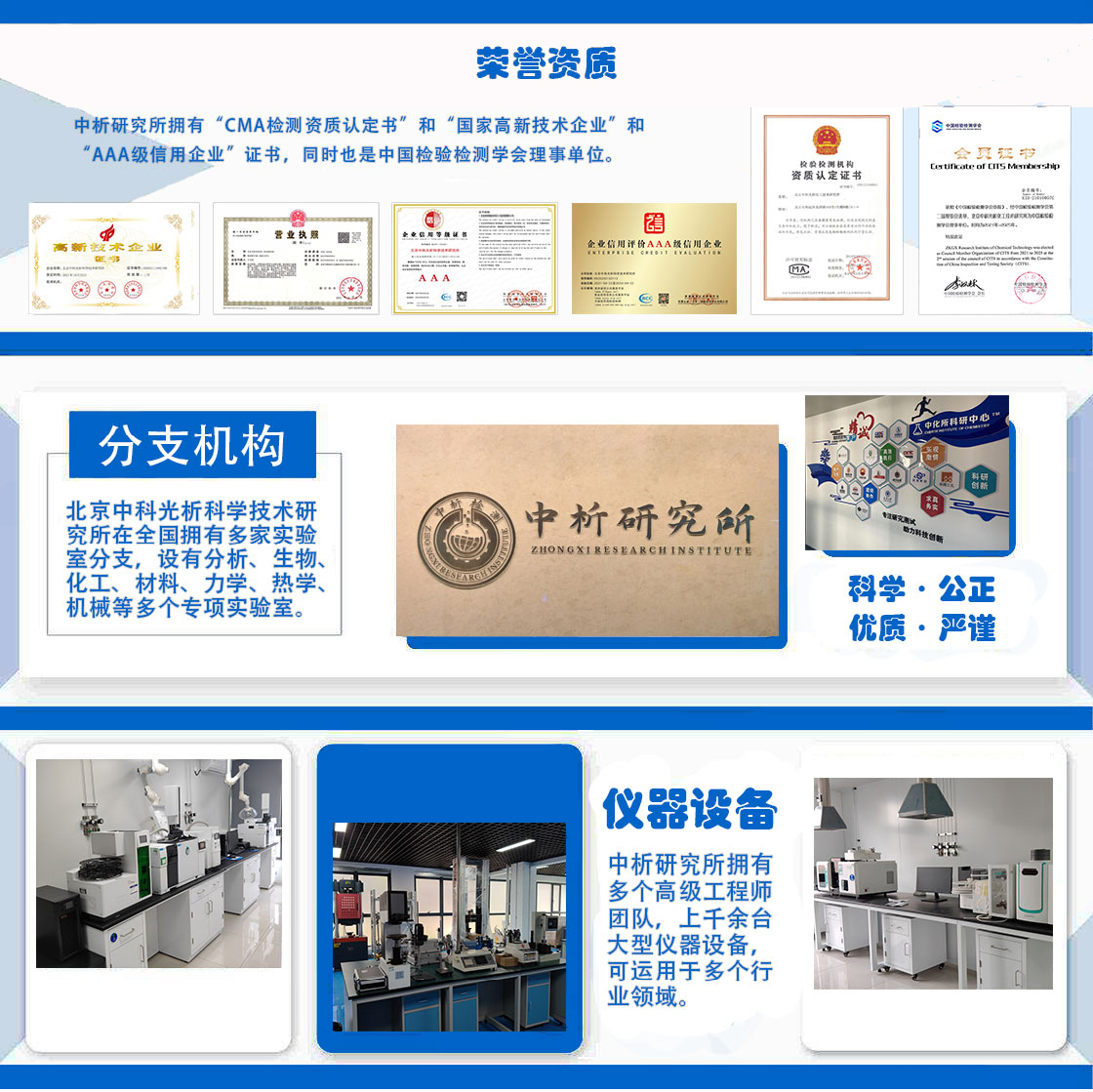
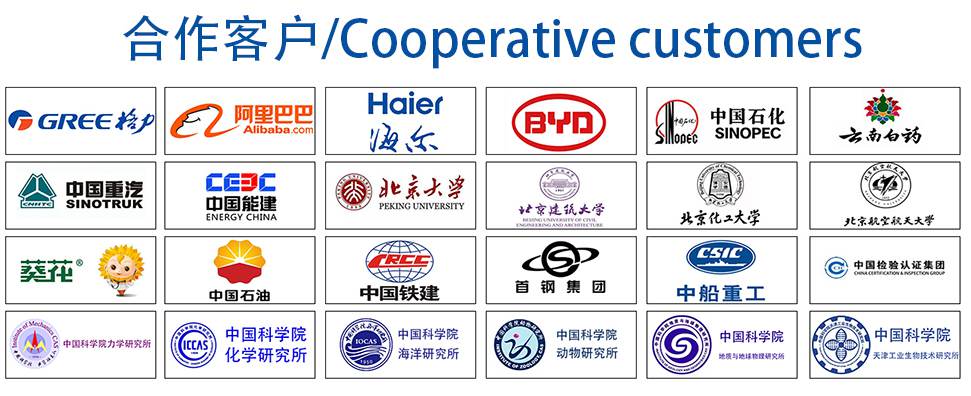