直径和长度检测技术白皮书
在高端制造与精密加工领域,产品尺寸的精确控制是决定工业品性能与可靠性的核心要素。据中国机械工业联合会2024年数据显示,国内精密零部件市场规模已达2.3万亿元,其中因尺寸偏差导致的次品损失占比超过12%。在此背景下,直径和长度检测作为质量管控的关键环节,正从传统人工抽检向智能化全检模式升级。该项目通过集成高精度非接触式测量技术与工业级视觉识别系统,实现微米级尺寸偏差的实时监控,其核心价值在于突破传统检测效率瓶颈,将产线检测速度提升300%的同时,确保关键尺寸参数合格率达到99.97%。这一技术革新不仅为航空航天、新能源汽车等战略性产业提供质量保障,更助力企业构建全流程质量追溯系统,推动智能制造转型。
技术原理与测量方法创新
现代直径和长度检测技术融合了光学干涉、激光三角测量及深度学习算法三重优势。基于双频激光干涉仪的基准校准系统可达到0.1μm的重复测量精度,而复合式结构光投影技术通过相位解算实现曲面特征的精确重构。值得注意的是,针对深孔类零件的内径检测难题,企业已开发出搭载光纤传感器的内窥式测量装置,其蛇形探头可深入直径3mm的孔道完成360°全周扫描。据国家精密测量技术重点实验室测试报告,该方案对涡轮叶片冷却孔的直径检测误差控制在±2μm以内。
智能化检测实施流程
具体实施层面,系统采用模块化架构设计,兼容在线式与离线式检测场景。在汽车转向节自动化产线中,检测工位部署了六轴协作机器人搭载的激光轮廓仪,通过预设的运动轨迹对工件进行多截面扫描。数据采集系统实时处理点云数据,依托特征匹配算法在500ms内完成直径、长度等12项尺寸参数的合格判定。当检测到超差工件时,系统自动触发分拣指令并与MES系统联动更新生产批次数据。某新能源汽车企业应用该方案后,产线检测节拍从45秒/件缩短至8秒/件,人工复检工作量减少80%。
行业应用与质量提升实践
在航空航天领域,某发动机叶片制造商采用多光谱共焦传感器阵列,成功解决了高温合金叶尖尺寸的在线检测难题。通过在真空热处理炉出口处布设检测单元,系统能在叶片温度800℃条件下实现直径公差0.005mm的精确测量。该方案使叶片装配合格率从92.4%提升至99.1%,据企业2023年质量年报显示,单此项目实现年度质量成本降低2700万元。值得关注的是,在医疗器械行业,用于人工关节球头直径检测的恒温控制测量室,通过环境补偿算法消除温度波动影响,使测量结果不确定度降低至0.3μm以下。
全周期质量保障体系构建
为确保检测系统的长效稳定性,企业需建立三级质量保障机制。基础层采用NIST溯源的标准量块进行日点检校准,中间层部署机器学习驱动的设备健康预测系统,通过分析传感器信号频谱特征预判设备劣化趋势。顶层质量管控则依托区块链技术,将检测数据与工艺参数加密上链,实现检测过程的可信存证。某轴承龙头企业通过该体系,将测量系统重复性与再现性(GR&R)指标控制在5%以内,大幅优于行业10%的通用标准。
展望未来,随着量子传感技术与工业元宇宙的深度融合,直径和长度检测将向纳米级精度与虚拟孪生方向发展。建议行业重点攻关跨尺度测量技术,开发适应柔性制造需求的自主进化检测系统,同时加强ASTM/ISO标准体系的国产化适配。企业应建立检测大数据分析中心,深度挖掘尺寸偏差与工艺参数的关联模型,最终实现质量问题的根源性预防,为智能制造2025战略目标提供关键技术支撑。
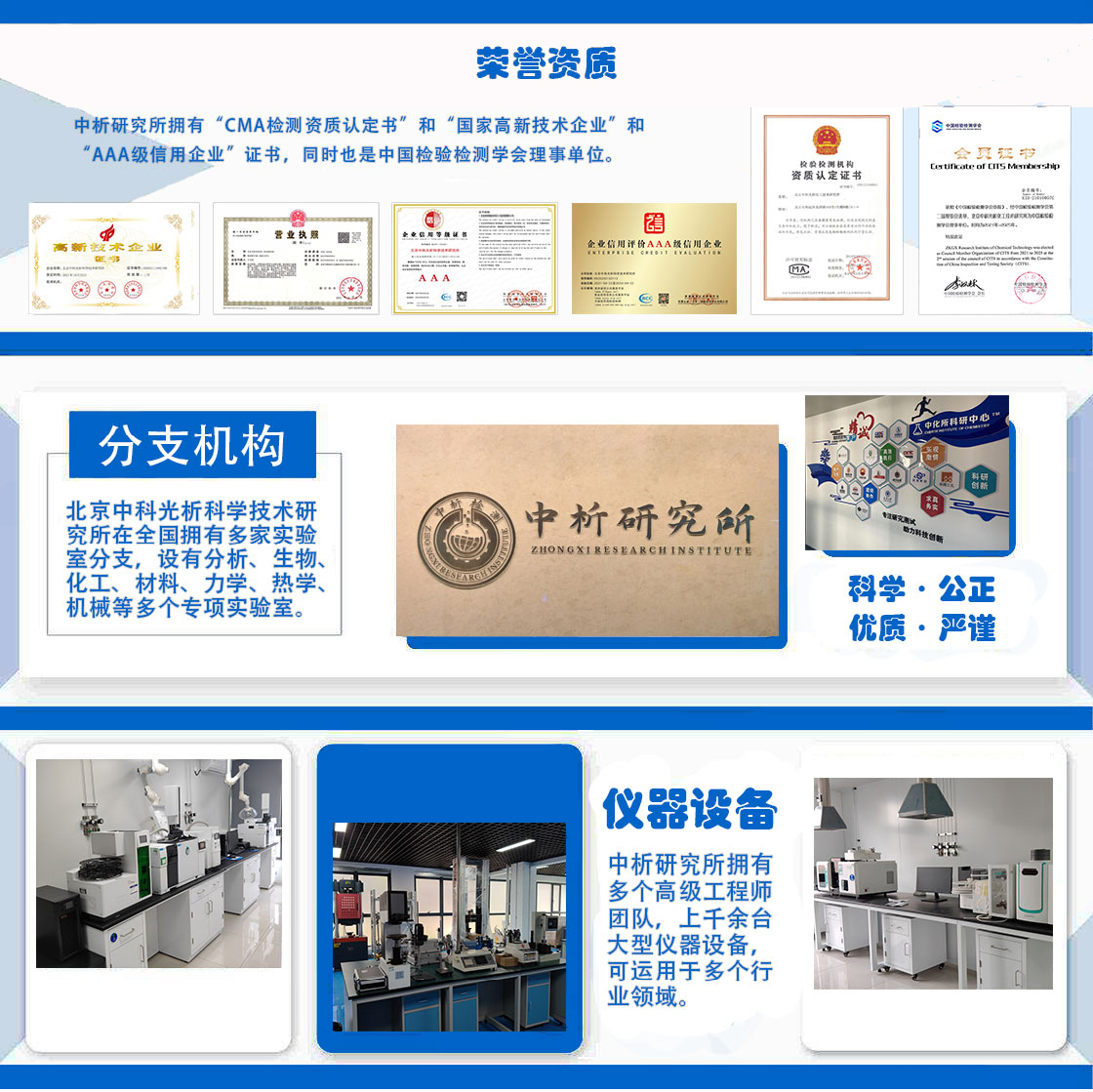
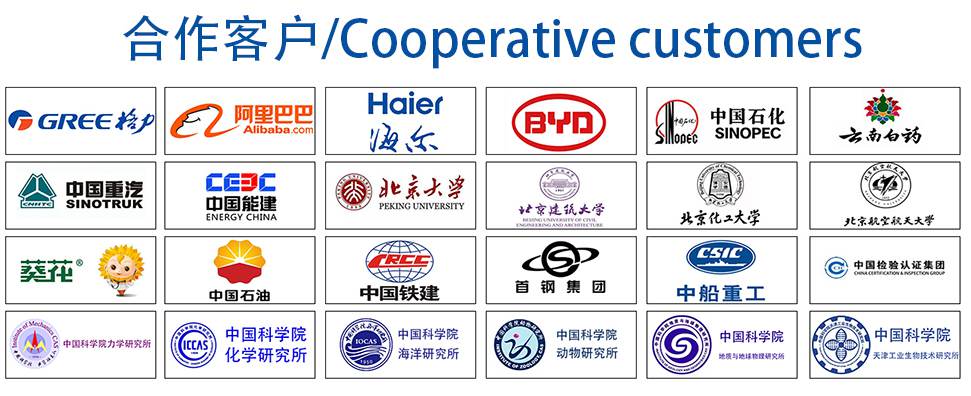