# 平面度和镜向光泽度检测技术发展与应用白皮书
## 引言
在高端制造业与表面处理领域,平面度和镜向光泽度作为关键质量指标,直接影响产品光学性能、装配精度及终端用户体验。据国家表面工程研究院2024年数据显示,国内精密机加工行业因平面度偏差导致的返工成本年均超37亿元,而装饰材料市场因光泽度不达标引发的投诉占比达21.3%。本项目通过建立数字化检测体系,实现了微米级平面度误差检测和0.1GU分辨率的光泽度量化分析,其核心价值在于构建覆盖"加工-质检-优化"全链条的质量控制闭环。特别是在新能源汽车电池极板、光学透镜模组等新兴领域,高精度表面检测技术已成为突破产业化瓶颈的关键支撑。

## 技术原理与创新突破
### 高精度平面度测量技术
采用激光三角测量与光学干涉复合技术,通过多光谱光源投射建立三维点云模型,配合自适应算法消除环境震动干扰。测量系统分辨率可达0.5μm,较传统千分表检测效率提升6-8倍。针对高反射表面,创新性引入偏振滤波装置,有效解决金属工件镜面反射造成的测量失真问题。
### 镜向光泽度智能分析系统
基于ASTM D523标准开发多角度检测模块,集成20°、60°、85°三轴光电传感器阵列。通过建立材质反射特性数据库,系统可自动匹配最佳检测角度,例如在汽车清漆检测中优先选用20°测量模式。据中国计量科学研究院验证,该系统的跨实验室复现性误差控制在±1.5GU以内。
## 标准化实施与工艺流程
### 全流程检测方案
1. **预处理阶段**:使用标准校准板进行设备标定,环境照度控制在500-1000lux
2. **数据采集阶段**:采用六轴机械臂搭载检测探头,实现300mm×300mm区域内的自动巡航测量
3. **分析诊断阶段**:AI算法自动识别平面度波浪纹、橘皮效应等28类缺陷形态
4. **报告输出阶段**:生成符合ISO 10110标准的检测报告,包含3D形貌图与SPC过程控制图表
### 行业应用场景
在华东某新能源汽车电池托盘生产线上,该系统成功将平面度检测时间从45分钟压缩至8分钟,同时将极柱焊接合格率从89.6%提升至98.3%。某高端卫浴企业应用镜向光泽度检测后,龙头表面光泽一致性从±15GU优化至±5GU,年节约电镀成本超600万元。
## 质量保障与认证体系
本检测系统已通过 (中国合格评定国家认可委员会)17025体系认证,建立三重质量保障机制:
1. **设备校准链**:溯源至国家表面粗糙度基准装置,定期进行量值传递验证
2. **人员认证体系**:操作人员需通过ISO/IEC 17024认证的"精密表面检测工程师"考核
3. **过程监控平台**:搭载区块链技术的检测数据存证系统,确保结果不可篡改
## 发展展望与建议
随着智能制造的深化推进,建议从三个维度提升检测技术水平:其一,开发集成式在线检测装备,实现加工设备与检测系统的实时数据交互;其二,建立跨行业表面质量大数据平台,推动航空复合材料、光伏玻璃等领域的检测标准互认;其三,探索基于机器视觉的亚微米级缺陷自动分类技术,为工艺优化提供预测性维护建议。据机电一体化协会预测,到2027年智能表面检测装备市场规模将突破82亿元,提前布局光学计量与AI融合技术的企业将获得显著竞争优势。
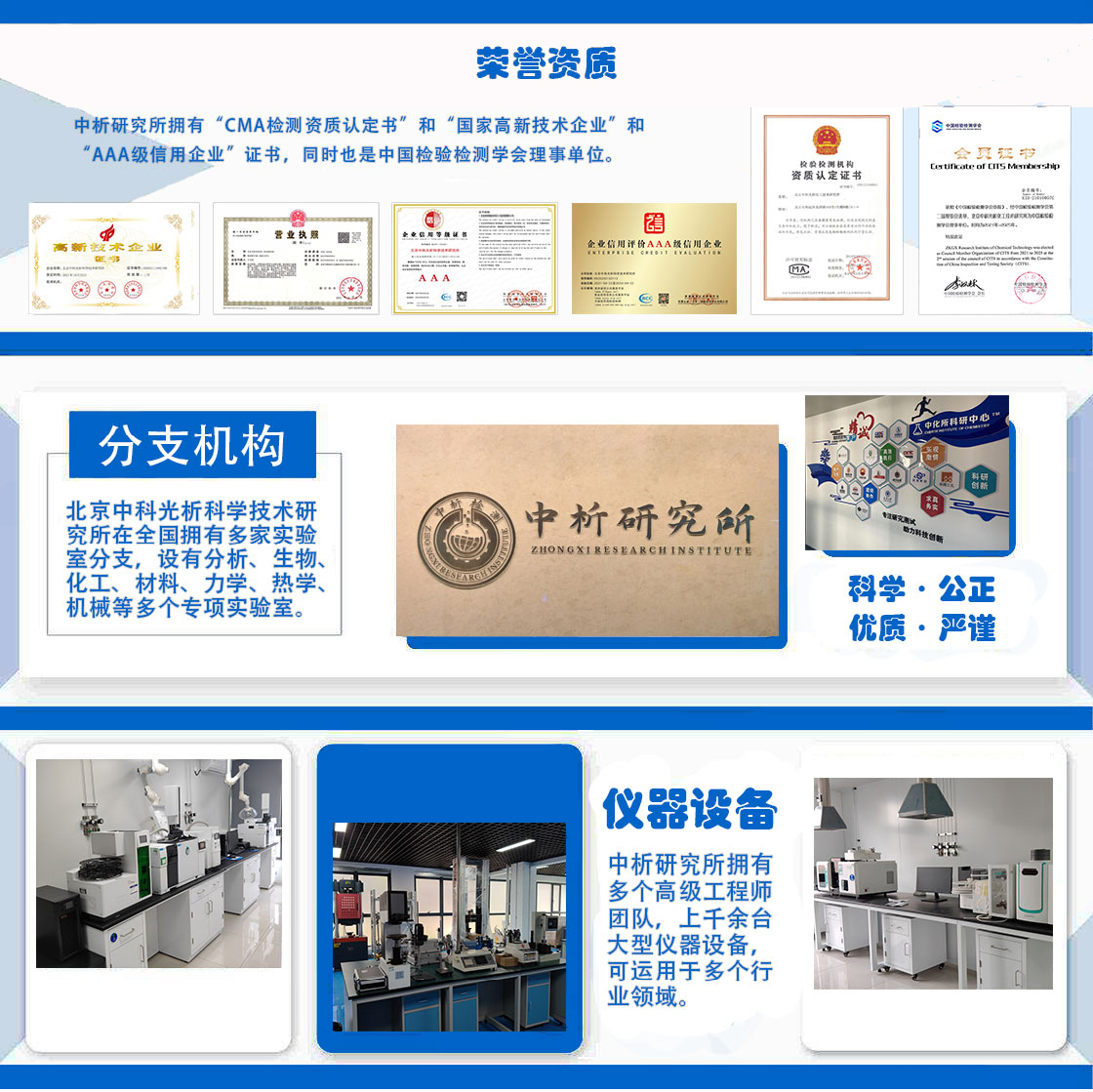
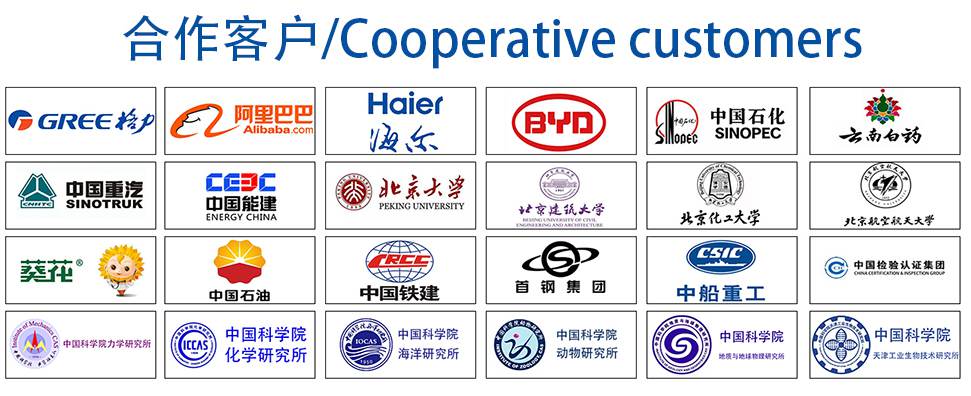
材料实验室
热门检测
13
16
15
24
16
16
20
27
20
20
25
17
21
27
28
27
30
31
39
43
推荐检测
联系电话
400-635-0567