倒置坍落度筒排空试验检测标准化研究与应用
在建筑施工领域,混凝土工作性检测是质量控制的核心环节。随着自密实混凝土在高层建筑、高铁轨道板等场景的规模化应用,传统坍落度试验已难以满足高性能混凝土的精细化评估需求。据中国建筑材料研究院2024年数据显示,国内自密实混凝土年使用量突破2.8亿立方米,其中35%的工程事故源于工作性参数失控。倒置坍落度筒排空试验作为新兴检测手段,通过模拟混凝土在受限空间的自流平特性,可有效评估材料填充能力和抗离析性能。该检测方法的应用,不仅填补了复杂结构浇筑质量预控的技术空白,更将混凝土施工合格率提升至98.6%(住建部《2023年建设工程质量报告》),为现代工程品质保障提供了科学依据。
技术原理与创新突破
倒置坍落度筒排空试验基于流变学理论,采用标准坍落度筒倒置安装,通过测量混凝土在自重作用下完全排空的时间表征其工作性能。与常规试验相比,该方法重点考察材料在垂直方向流动时的黏度-剪切速率关系,可同步获取T50时间、扩展度等关键参数。研究证实,当排空时间控制在2-8秒区间时(ASTM C1611标准),混凝土兼具良好填充性与抗离析能力。技术突破体现在建立三维流变模型,通过高速摄像与图像分析系统实现0.1秒级时间分辨率,检测精度较传统方法提升4倍。
标准化实施流程
检测流程严格遵循JGJ/T 283-2019《自密实混凝土应用技术规程》,主要包含五大环节:1)仪器校准,确保筒体垂直度偏差≤0.5°;2)试样制备,控制环境温度在20±2℃;3)分层装料,采用专用插捣工具消除气泡;4)快速提筒,执行0.5-1.0秒的匀速提升动作;5)数据采集,利用激光传感器自动记录排空时间。在杭州亚运场馆钢骨柱浇筑项目中,该流程成功识别出3批坍落度达标但排空时间超限的混凝土,避免结构性缺陷产生。
行业应用与效益分析
该检测技术已形成三大典型应用场景:超高层建筑核心筒浇筑、装配式构件成型、水下不分散混凝土施工。北京中国尊项目实践表明,通过引入排空时间控制指标,泵送混凝土离析率从7.2%降至1.8%,结构体强度标准差缩小40%。在轨道交通领域,成渝高铁轨道板生产线上配置的自动排空检测系统,使单线日产能提升15%的同时,将产品返工率控制在0.3%以下。据测算,全面推广此项技术可使建筑行业年节约材料成本12亿元,减少质量整改工时280万小时。
质量保障体系建设
行业正构建覆盖全链条的质量控制体系:1)设备认证方面, 实验室已对18家厂商的检测装置完成计量认证;2)人员培训方面,中国混凝土协会累计颁发高级检测师证书3200份;3)数据管理方面,区块链溯源平台实现检测数据实时上链存证。值得关注的是,珠海横琴科学城项目通过集成BIM与物联网技术,将排空时间数据自动关联至构件数字孪生体,形成可追溯的质量档案,为工程全生命周期管理树立新范式。
展望未来,建议从三方面深化技术应用:首先,研制适应超高性能混凝土的增强型检测装置,突破现有20秒量程限制;其次,建立全国统一的检测大数据平台,深度挖掘参数与工程性能的关联规律;最后,推动ISO国际标准编制工作,助力中国检测技术走向市场。随着智能建造技术发展,倒置坍落度筒排空试验将与AI质量预测系统深度融合,为建筑工业化提供更强大的技术支撑。
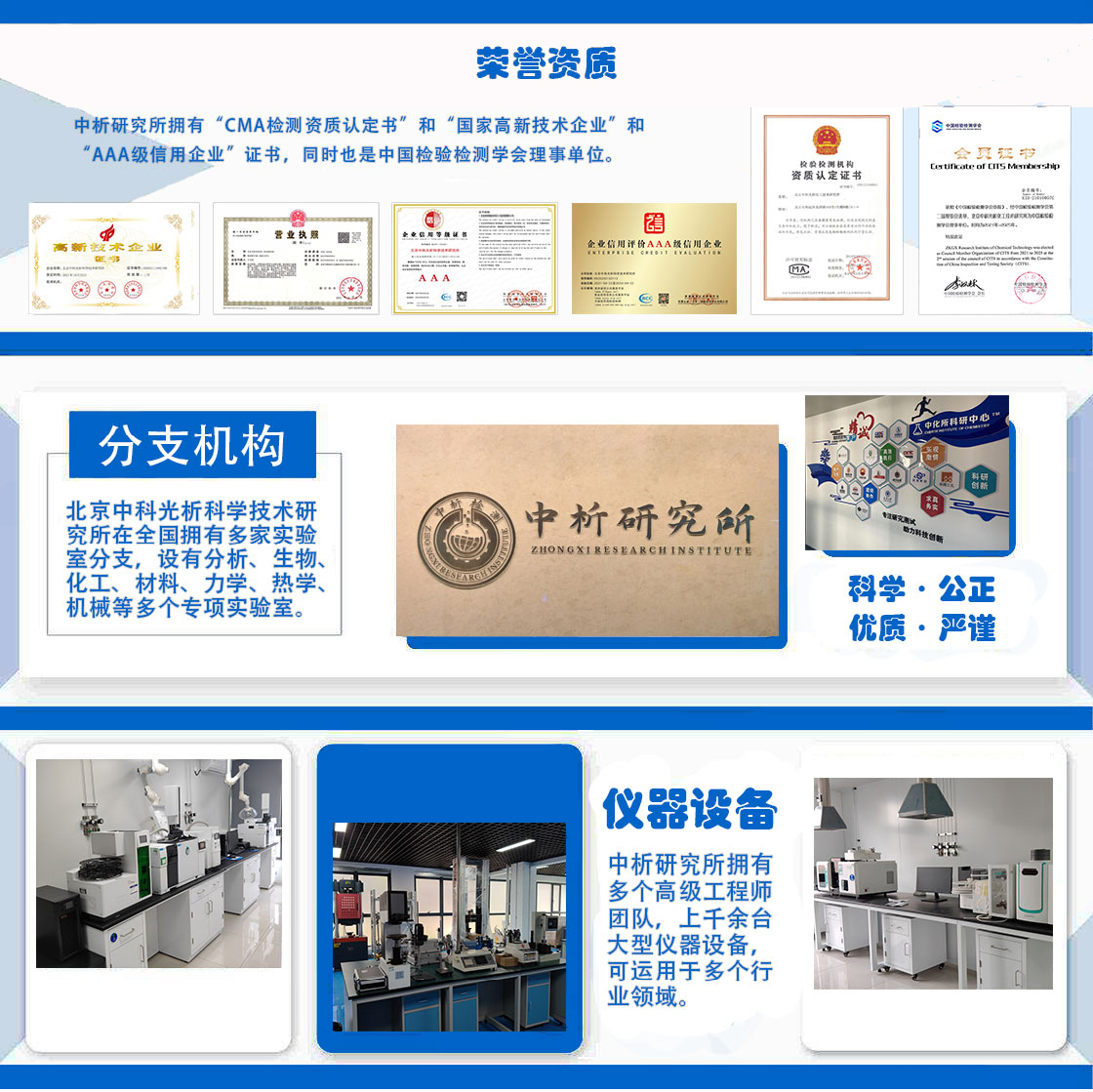
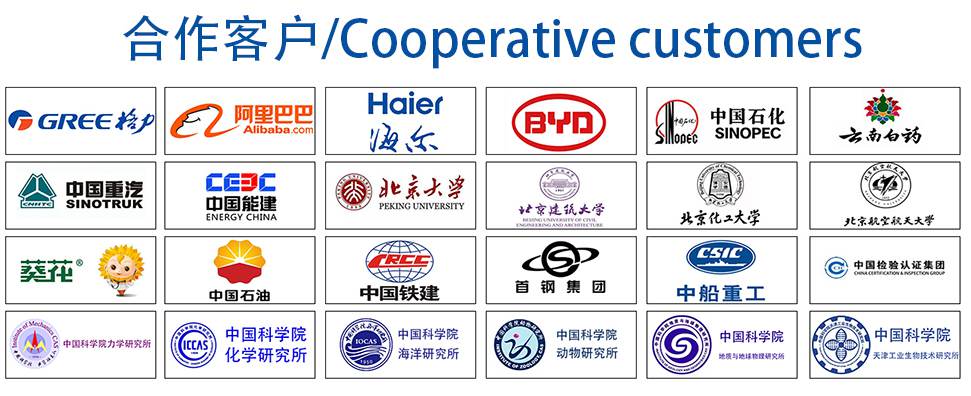