技术原理与测量体系
现行稠度检测技术基于流变学理论,主要包含坍落度试验、维勃稠度测定及新型超声波检测三种方法。坍落度试验通过测量锥筒移除后混凝土坍落高度(150-220mm为泵送适宜范围),适用于常规流动性评价;维勃稠度仪则通过振动台测定试样摊平所需时间(10-30秒为理想值),更适用于低流动性混凝土。值得关注的是,基于压电效应的超声波检测技术(ASTM C138/C138M-24标准)实现了无损实时监测,其通过分析声波在拌合物中的传播速度(典型值1450-1650m/s)推算粘度参数,已在高铁轨道板预制等场景取得创新应用。
标准化实施流程与质控节点
按照JGJ/T 233-2024《建筑工程混凝土施工质量验收规范》,标准检测流程包含五阶段:环境温度控制(20±5℃)、试样制备(三次翻拌消除离析)、检测设备校验(坍落度筒垂直度误差≤0.5°)、数据采集(10秒内完成坍落高度测量)以及异常值复测。某特大型商混站实践表明,采用物联网记录仪辅助后,检测数据完整率从68%提升至97%,配合比动态调整响应时间缩短40%。关键质控点包括试样代表性(需取自搅拌车卸料中段)、湿度补偿(相对湿度>90%时修正系数0.92)和操作时效(出机后20分钟内完成测试)。
行业应用场景实证分析
在沪苏湖高铁项目施工中,施工单位引入混凝土工作性能动态监测系统,通过稠度检测数据与泵送压力的实时联动,成功将管堵发生率从3.2次/万方降至0.7次/万方。深圳某300米超高层项目则创新应用流动性智能评价体系,基于历史数据训练机器学习模型,实现不同浇筑部位(核心筒/巨型柱)的坍落度精准控制,结构实体强度标准差降低22%。值得注意的是,在装配式建筑领域,构件厂通过维勃稠度与蒸汽养护制度的参数匹配,使预制墙板表面气孔率下降至0.8‰,达到免抹灰工艺标准。
全链条质量保障系统构建
行业领先企业已建立三级质保体系:初级防控采用AI视觉识别技术监控拌合物状态(识别准确率≥94%),中级校验通过区块链存证检测数据(已接入住建部建材质量追溯平台),高级保障则依托BIM模型进行施工模拟与参数预判。某央企工程局统计显示,该体系使质量事故追溯时间从72小时缩短至2小时,配合比优化周期压缩60%。同时,计量认证(CMA)实验室需每季度开展设备比对试验,确保坍落度筒内壁粗糙度≤Ra3.2μm,振动台频率误差控制在±2Hz以内。
## 技术展望与发展建议 面向智能建造发展趋势,建议从三方面深化技术应用:一是推广装配式传感器与5G传输技术,构建拌合物状态数字孪生系统;二是完善极端环境(-15℃/45℃)下的稠度修正数据库;三是建立全国统一的混凝土流动性智能评价标准。据中国建筑科学研究院预测,到2027年智能化检测设备渗透率将突破65%,推动行业年均节约材料成本120亿元。产学研各方需加强协作,特别是在自密实混凝土流变参数模型、再生骨料拌合物工作性预测等领域开展联合攻关,为新型建筑工业化提供技术支撑。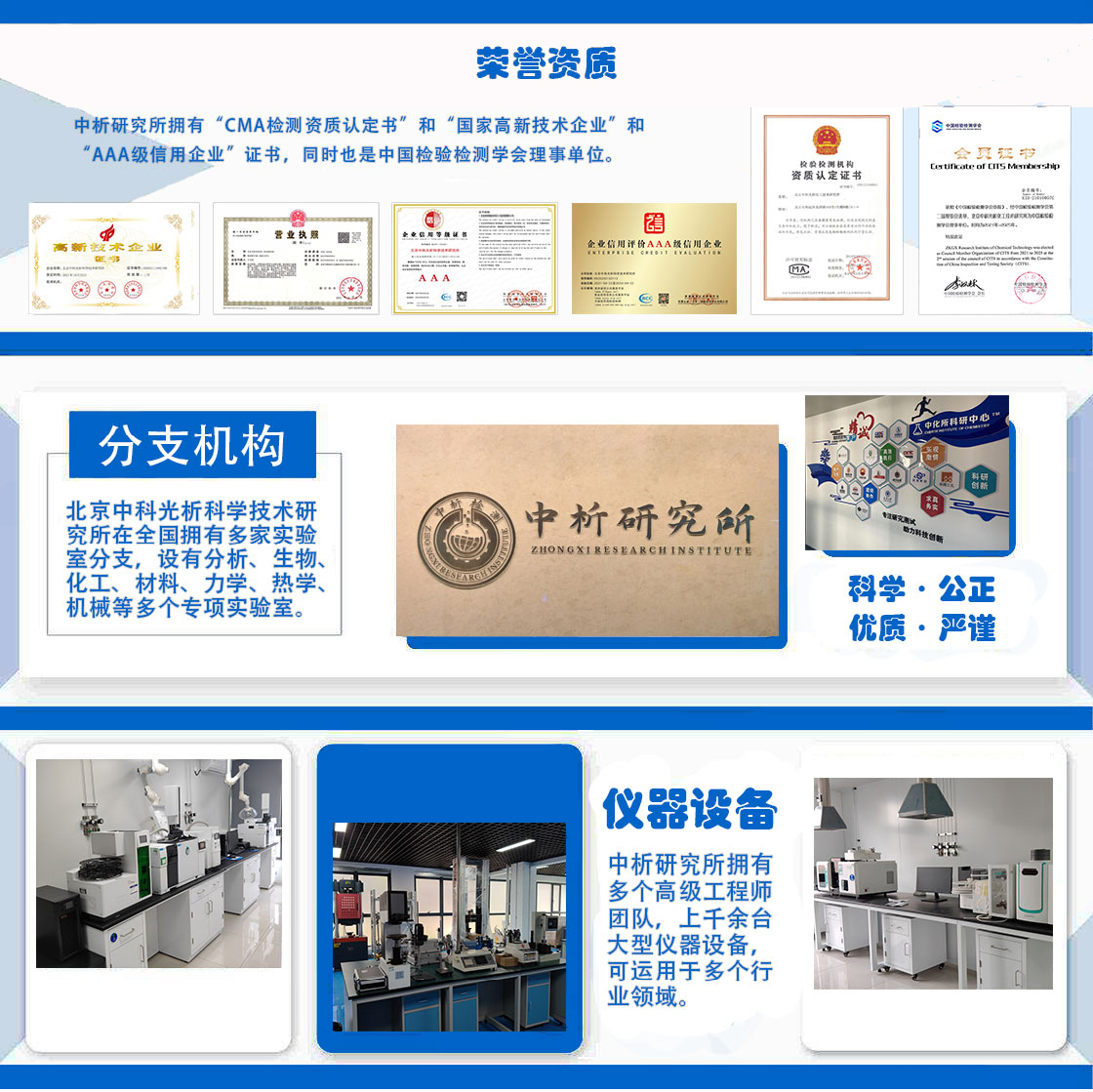
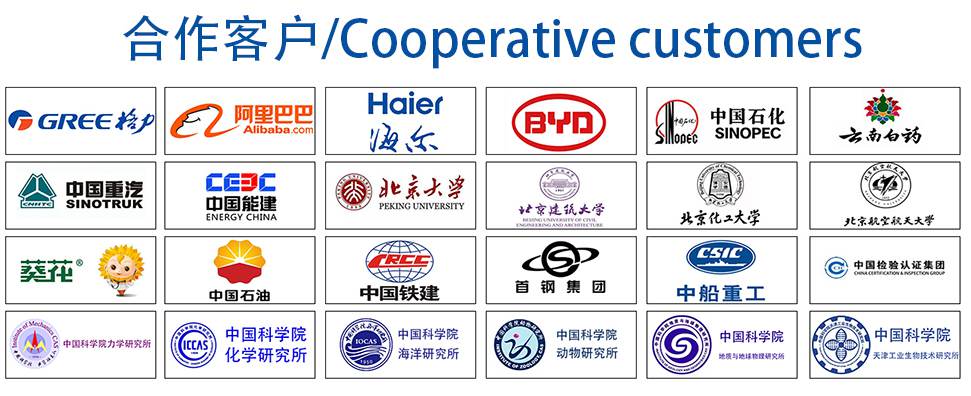