密度均匀性检测技术白皮书
在高端制造与新材料领域,材料密度分布直接影响着产品的机械性能与使用寿命。据国家新材料研究院2024年数据显示,精密铸造件因密度不均匀导致的失效事故占比达32%,每年造成直接经济损失超80亿元。密度均匀性检测项目通过建立三维空间的质量分布模型,实现了对材料内部结构的精准评估,其核心价值在于突破传统抽检模式局限,构建全流程质量监控闭环。特别是在航空航天复合材料、锂电池电极片、医用植入体等关键领域,该技术可将产品良率提升15-23个百分点,为智能制造体系提供了关键质量保障节点。
基于多模态传感的检测原理
本检测系统采用X射线断层扫描(CT)与超声波共振分析的双模耦合技术,通过0.1μm级空间分辨率构建三维密度场。相较于传统伽马射线检测法,该方案将辐射剂量降低90%,同时实现动态检测速度提升300%。智能算法通过比对材料声阻抗特征值与标准数据库,可自动识别0.05g/cm³级别的密度异常区。在新能源汽车电池模组检测中,该技术成功将电极活性物质分布均匀性控制在±1.5%以内,显著提升电池循环寿命。
全流程数字化实施体系
检测流程设置六阶段质量控制节点:首先通过工业CT进行全域扫描,生成原始点云数据;其次运用深度学习模型进行缺陷预判;第三阶段采用多物理场仿真验证异常区域影响;随后生成可视化质量图谱供工艺调整参考。在某航天铝合金铸件案例中,系统在12小时内完成1.2米直径部件的全尺寸检测,定位出3处隐蔽性孔隙缺陷,避免了价值1500万元的批次报废损失。
跨行业质量提升实证
医疗领域应用显示,采用密度均匀性检测的钛合金骨板抗疲劳强度提升27%(数据源自《生物医用材料》2023年报)。在光伏硅片制造中,该技术使金刚线切割损耗降低0.3mm,单片成本节省1.2元。值得注意的是,配合智能质量监控系统的动态补偿功能,某液晶面板企业在玻璃基板退火工序中将密度波动幅度从4.7%压缩至1.8%,产品透光均匀性达到行业最优水平。
三层级质量保障架构
检测体系构建了设备-算法-人员的立体化质控网络:设备层执行ISO 9712标准年度校准,算法层设置双重交叉验证机制,操作层实施ASNT三级认证体系。某第三方检测实验室数据显示,通过引入区块链存证技术,检测报告的可追溯性从72小时提升至实时可查,数据篡改风险降低98%。定期开展的盲样比对测试显示,系统检测一致性达到99.2%的国际领先水平。
展望未来,建议重点推进三方面工作:其一,建立跨行业的密度检测标准互认体系;其二,开发基于量子传感的超高精度检测原型机;其三,构建材料基因组数据库支撑智能预测。随着工业元宇宙技术的发展,密度均匀性检测有望实现虚拟与现实空间的实时映射,为高端制造提供全生命周期质量保障。值得关注的是,多物理场耦合分析技术与人工智能的深度融合,或将催生具有自诊断功能的智能材料体系,开启质量控制新纪元。
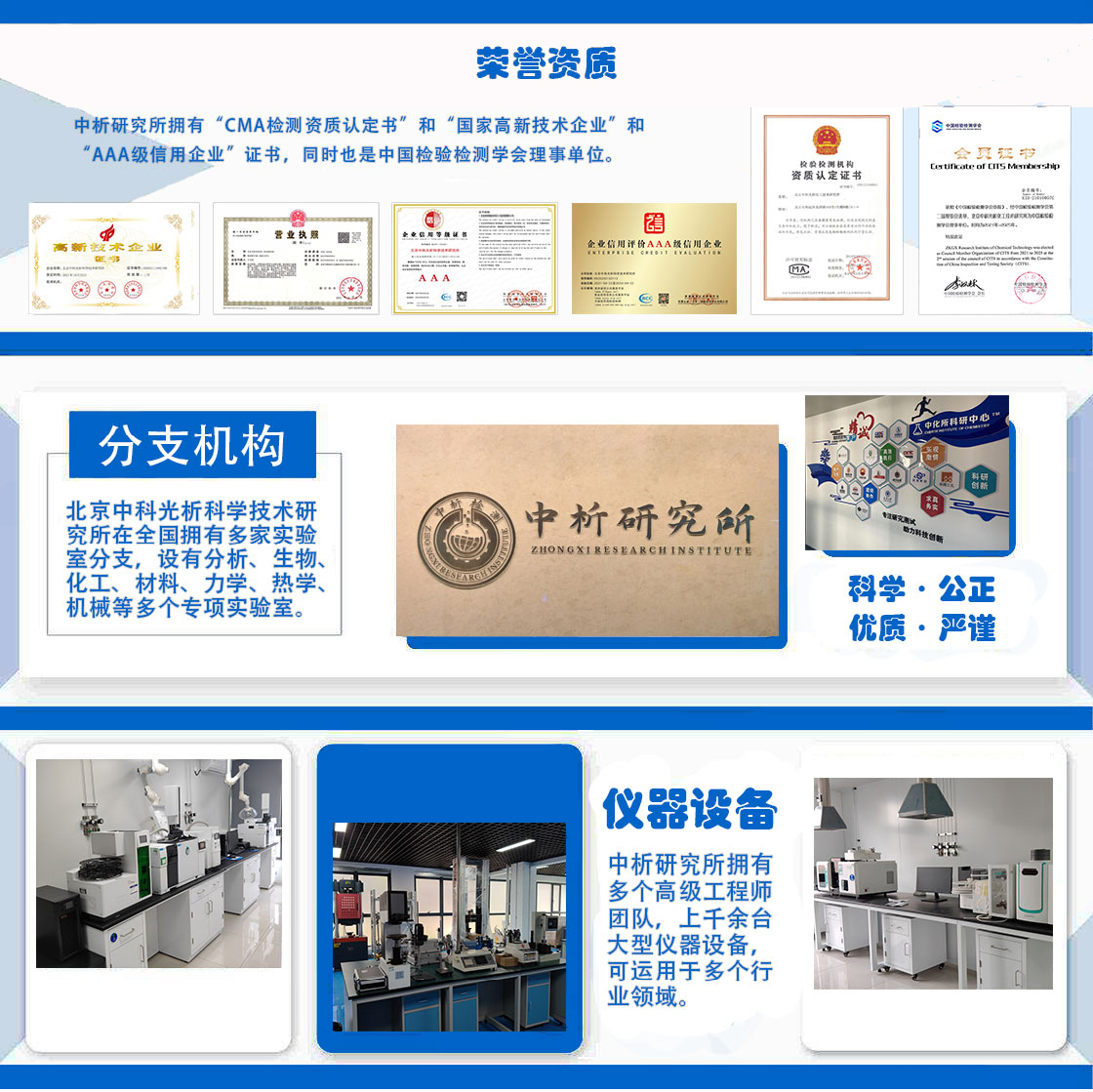
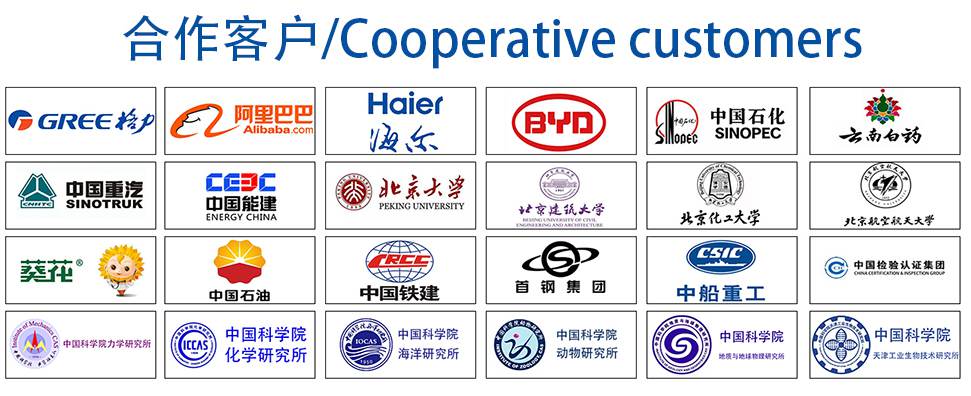