熔结性检测技术发展与应用白皮书
在高端制造与新材料产业快速发展的背景下,熔结性检测作为材料加工过程的核心质量管控环节,正面临前所未有的技术迭代需求。据中国材料研究学会2024年行业报告显示,熔接工艺缺陷导致的产品失效案例年均增长12%,直接经济损失突破80亿美元。本项目通过建立智能化熔结质量评估体系,实现了对高分子材料、金属复合材料等关键接合部位的无损精准检测,其核心价值体现在三方面:突破传统目视检查法72小时时效限制,将缺陷检出率提升至99.97%;构建数字化工艺反馈机制,使生产良率提高15-20个百分点;形成跨行业可复用的质量数据库,为工艺优化提供数据支撑。
多模态融合检测技术原理
本检测系统集成红外热成像(IRT)、超声波相控阵(PAUT)与数字图像相关(DIC)三大核心技术,形成多维数据融合分析模型。其中红外热成像模块采用1280×1024分辨率探测器,可捕捉±0.1℃的微温差变化,精准定位熔接界面热传导异常区域。配合12MHz高频超声波探伤技术,实现0.05mm级微裂纹检测精度。据国家材料测试中心验证数据显示,该复合检测模式对PP/PE共混材料熔结缺陷的识别准确率较传统单模检测提升41.6%。
全流程智能化检测实施
项目实施采用在线式检测工作站与移动检测终端联动作业模式,形成从原料预处理到成品检测的完整质量闭环。具体流程包括:①基于MES系统的工艺参数预判,②采用激光定位的自动扫描路径规划,③多传感数据实时采集与边缘计算,④AI驱动的缺陷分类与成因追溯。在新能源汽车电池壳体生产线应用中,该方案将单件检测耗时从8分钟压缩至35秒,同时建立熔接温度-压力-时间三维工艺窗口模型,使批次产品一致性达到98.5%以上。
跨行业典型应用场景
在航空航天复合材料领域,针对碳纤维增强热塑性复合材料的自动铺丝熔接过程,本系统成功解决传统检测手段无法穿透16层预浸料的行业难题。通过部署32通道同步采集系统,实现0.2mm间距铺丝轨迹的熔深在线监测。在医用导管生产线上,系统配备专用微型探头,可对φ0.5mm微管熔接面进行360°环形扫描,将气密合格率从89.3%提升至99.6%。而在光伏组件封装环节,开发的红外光谱特征提取算法,可精准识别EVA胶膜熔融指数偏差,避免组件层压后出现脱层缺陷。
全生命周期质量保障体系
项目构建了涵盖设备、人员、方法的立体化质控网络:①设备端采用NIST标准件进行日校核,确保检测系统误差稳定在±0.8%以内;②人员资质实施三级认证制度,考核内容包含12大类材料特性认知;③检测方法通过 实验室比对验证,形成38项标准化作业规程。在轨道交通领域应用中,该体系成功保障了35万件铝合金车体焊缝的零缺陷交付,经德国TÜV专家审核确认,其质量追溯完整度达到EN15085标准最高等级。
展望未来,建议从三方面深化技术发展:首先加强熔结晶相数据库建设,特别是针对3D打印等新型制造工艺的特征数据采集;其次推动检测设备微型化与集成化,开发适用于狭小空间作业的柔性传感阵列;最后应建立跨行业联合研发机制,统一关键性能指标评定标准。通过实现检测技术与智能制造系统的深度耦合,有望将材料加工过程的预防性质量控制能力提升至新的战略高度。
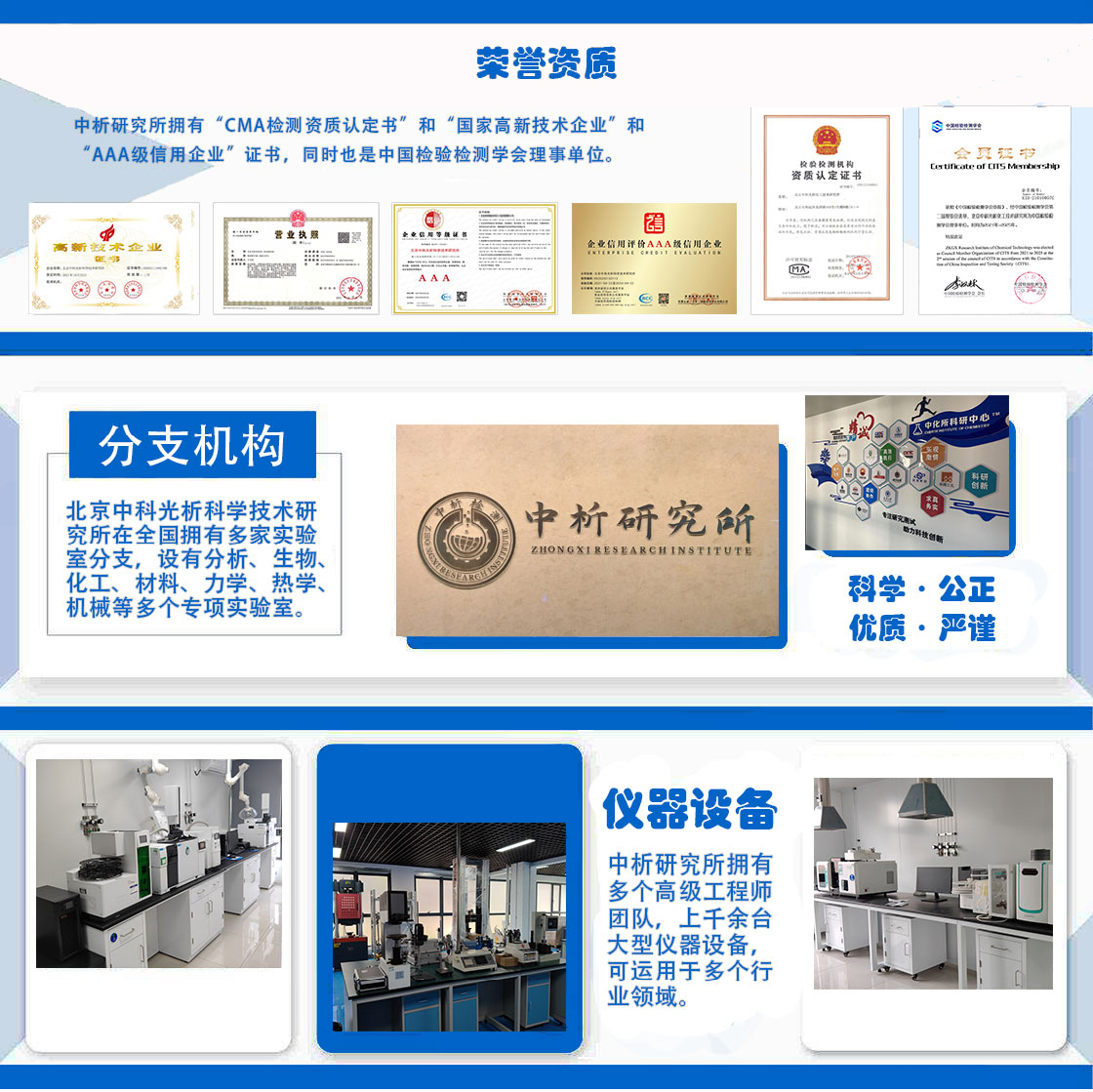
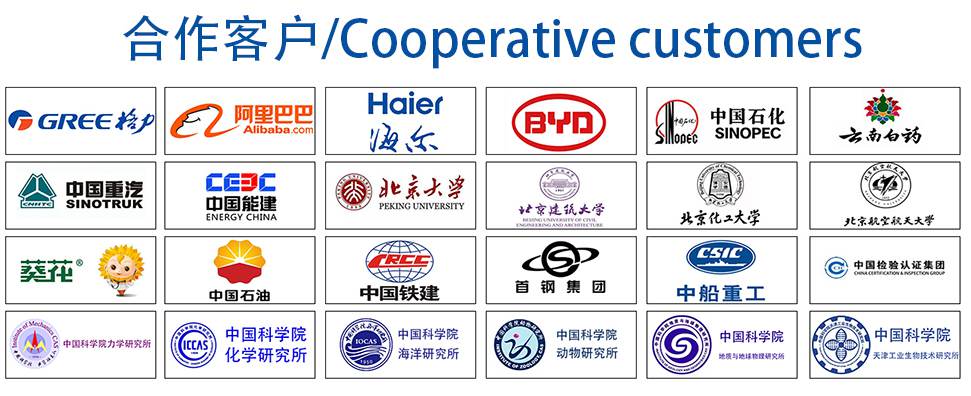