石英玻璃器皿坩埚检测的重要性
石英玻璃器皿(尤其是坩埚)作为实验室和工业生产中的关键耗材,广泛应用于高温熔融、化学分析、半导体材料制备等领域。其优异的热稳定性(软化点高达1730℃)、极低的热膨胀系数(0.54×10⁻⁶/K)以及卓越的耐腐蚀性能(可抵抗除氢氟酸外的多数酸碱),使其成为极端工作环境下的理想选择。但由于石英玻璃具有脆性大、加工难度高的特性,在制造、运输和使用过程中易产生微裂纹、气泡或尺寸偏差,可能造成安全隐患或实验数据失真。因此建立系统化的质量检测体系,对保障实验结果的准确性、延长设备使用寿命以及确保高温作业安全具有决定性意义。
核心检测项目与技术要求
1. 化学成分分析
采用X射线荧光光谱仪检测SiO₂纯度(≥99.95%),重点控制Al、Fe、K等杂质元素含量(总和≤30ppm)。依据GB/T 3284标准,使用电感耦合等离子体质谱法(ICP-MS)测定重金属残留,确保砷、铅含量符合ISO 3585:1998高纯石英玻璃规范要求。
2. 物理性能测试
通过三点弯曲法(依据ASTM C158-02)检测抗弯强度(≥50MPa),使用显微硬度计测定维氏硬度(≥650HV0.5),并采用激光散射法测量表面粗糙度(Ra≤0.8μm)。特别需关注坩埚底部与侧壁过渡区域的机械性能一致性。
3. 热学性能验证
在高温炉中进行梯度升温实验(20-1300℃),观察热膨胀系数变化(允许偏差≤5%)。通过热震试验(水淬法)验证抗热冲击性:按JIS R3106标准,将试样加热至1100℃后迅速投入25℃水中,循环次数≥3次无裂纹为合格。
4. 几何精度检测
使用三坐标测量仪(CMM)进行三维扫描,要求:容积公差≤±2%(参照标称值)、壁厚均匀度误差≤0.3mm、口部圆度偏差≤0.5mm。对于特殊设计的锥形坩埚,需额外检测锥角精度(±0.5°)。
5. 微观缺陷检测
应用工业CT断层扫描技术(分辨率≤5μm)排查内部气泡(直径≤0.2mm且分布密度<3个/cm³),使用电子显微镜(SEM)观察表面微裂纹(长度≤50μm)。特别注意熔制过程中产生的条纹状缺陷,其折射率变化应控制在不影响光学性能的范围内。
6. 耐腐蚀性测试
按照ISO 1776:1985标准进行酸腐蚀试验:将试样浸泡在沸腾的10%盐酸溶液中6小时后,质量损失率应<0.1mg/cm²。针对特殊应用场景,需增加氢氟酸蒸汽耐受性专项检测。
质量控制关键节点
建立从原料筛选到成品出厂的全程追溯体系,重点监控:熔制过程中的温度均匀性(±5℃)、退火工艺参数(降温速率≤5℃/min)、机加工刀具磨损量(更换阈值≤15μm)。建议每批次抽样比例不低于5%,对于高纯半导体级产品需实行100%在线检测。
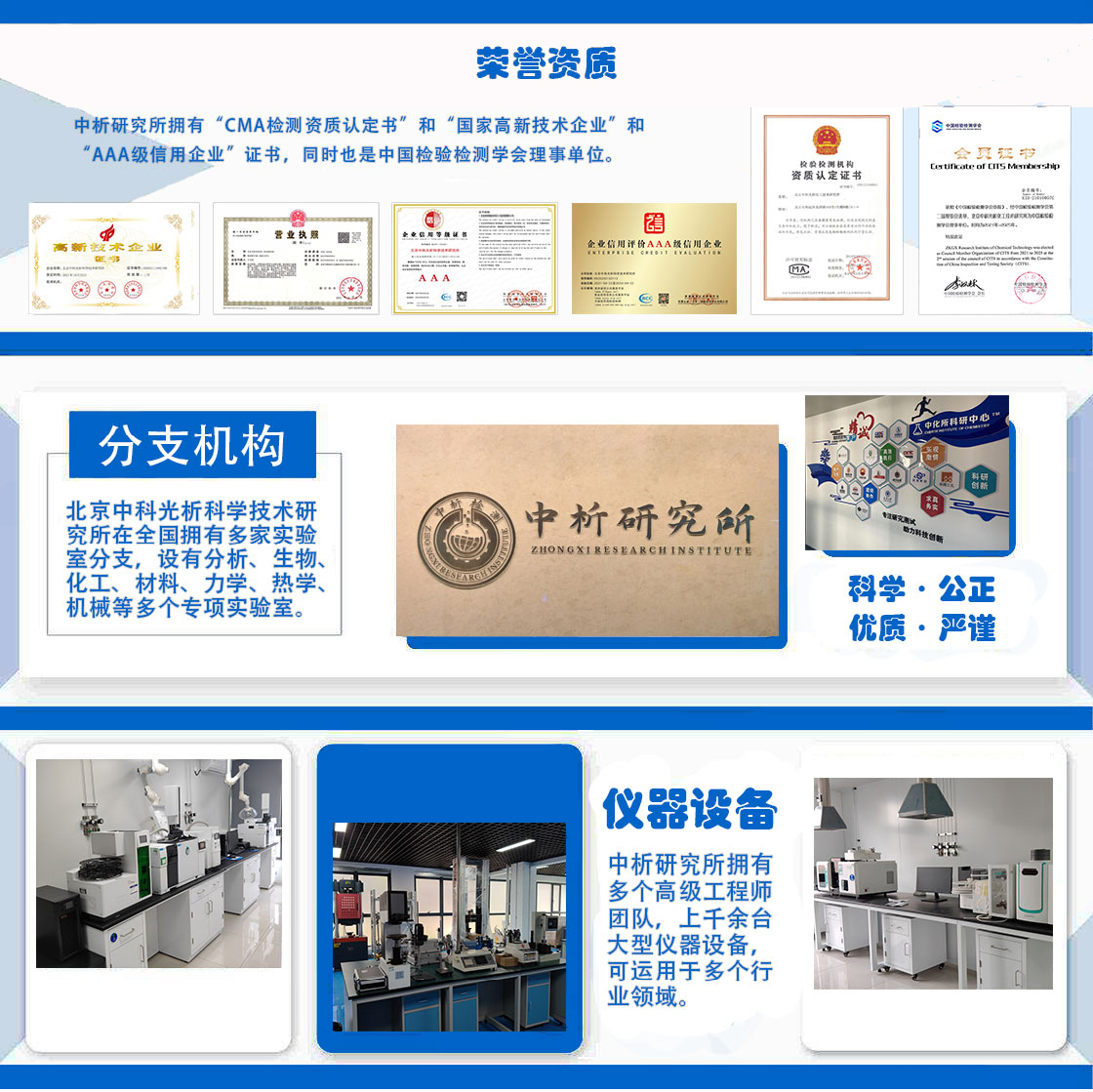
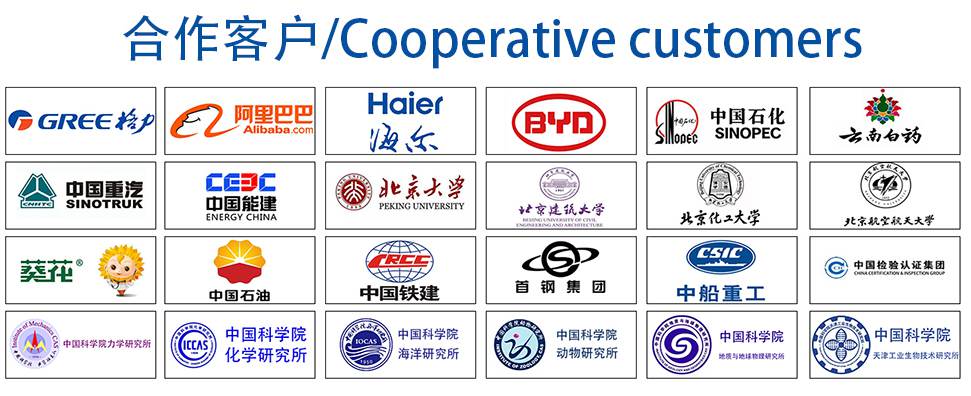