汽车内饰非金属材料检测的重要性
随着汽车行业的快速发展,消费者对车辆安全性、环保性和舒适性的要求日益提高。汽车内饰作为驾乘人员直接接触的部件,其材料性能直接关系到车内空气质量、使用耐久性以及乘员健康。非金属材料(如塑料、皮革、织物、橡胶、粘合剂等)因其轻量化、可塑性强等优势,被广泛应用于汽车内饰中。然而,这些材料可能含有挥发性有机物(VOC)、重金属或其他有害物质,长期暴露可能对人体造成危害。因此,通过科学规范的检测手段对汽车内饰非金属材料进行全面评估,已成为汽车制造行业质量控制的重要环节。
核心检测项目及标准
1. 挥发性有机化合物(VOC)检测
VOC是汽车内饰材料释放的主要污染物之一,包括甲醛、苯、甲苯、二甲苯等。检测方法通常采用气相色谱-质谱联用(GC-MS)技术,依据国标GB/T 27630-2011《乘用车内空气质量评价指南》或国际标准ISO 12219系列,通过模拟高温环境(如60℃密闭舱)测定材料中VOC的释放量,确保其符合限值要求。
2. 阻燃性能测试
汽车内饰材料需具备良好的阻燃性能以降低火灾风险。根据GB 8410-2006《汽车内饰材料的燃烧特性》标准,采用垂直燃烧法或氧指数法评估材料的燃烧速率、自熄时间和燃烧残留物。例如,材料在明火撤离后应在30秒内自行熄灭,且燃烧长度不超过100mm。
3. 耐磨性与抗老化性检测
通过Taber耐磨试验、紫外老化试验(ASTM G154)及湿热循环测试,评估材料表面在长期使用中是否出现褪色、龟裂或粉化现象。例如,皮革材料需经过10万次摩擦后仍保持表面完整性,塑料件在85℃、85%湿度环境下持续测试500小时无显著性能退化。
4. 有害物质限量检测
针对铅、镉、汞、六价铬等重金属及多环芳烃(PAHs)、邻苯二甲酸酯(增塑剂)等物质,依据欧盟REACH法规、ELV指令或国标GB/T 30512-2014进行检测。例如,儿童可接触部件的铅含量需低于100ppm,多环芳烃总量不得超过10mg/kg。
5. 气味及雾化性能评价
通过嗅辨员主观评价(VDA 270标准)和雾化试验(DIN 75201),测定材料在高温下释放的气味等级及挥发性物质在玻璃表面的冷凝量。优质内饰材料应达到气味等级≤3级(无刺激性),雾化值低于2mg。
6. 力学性能测试
包括拉伸强度(ASTM D638)、撕裂强度(ASTM D624)和硬度测试(邵氏硬度),确保材料在装配和使用过程中具备足够的机械强度和韧性。例如,仪表板塑料的拉伸强度需≥20MPa,弹性体材料的撕裂强度需≥30kN/m。
总结与趋势
随着环保法规趋严(如中国《汽车有害物质和可回收利用率管理要求》)及消费者健康意识的提升,汽车内饰非金属材料的检测正向更高精度、更广覆盖的方向发展。未来,新型生物基材料、低VOC水性胶粘剂的检测技术开发,以及全生命周期环境影响的综合评价体系,将成为行业技术升级的重点领域。
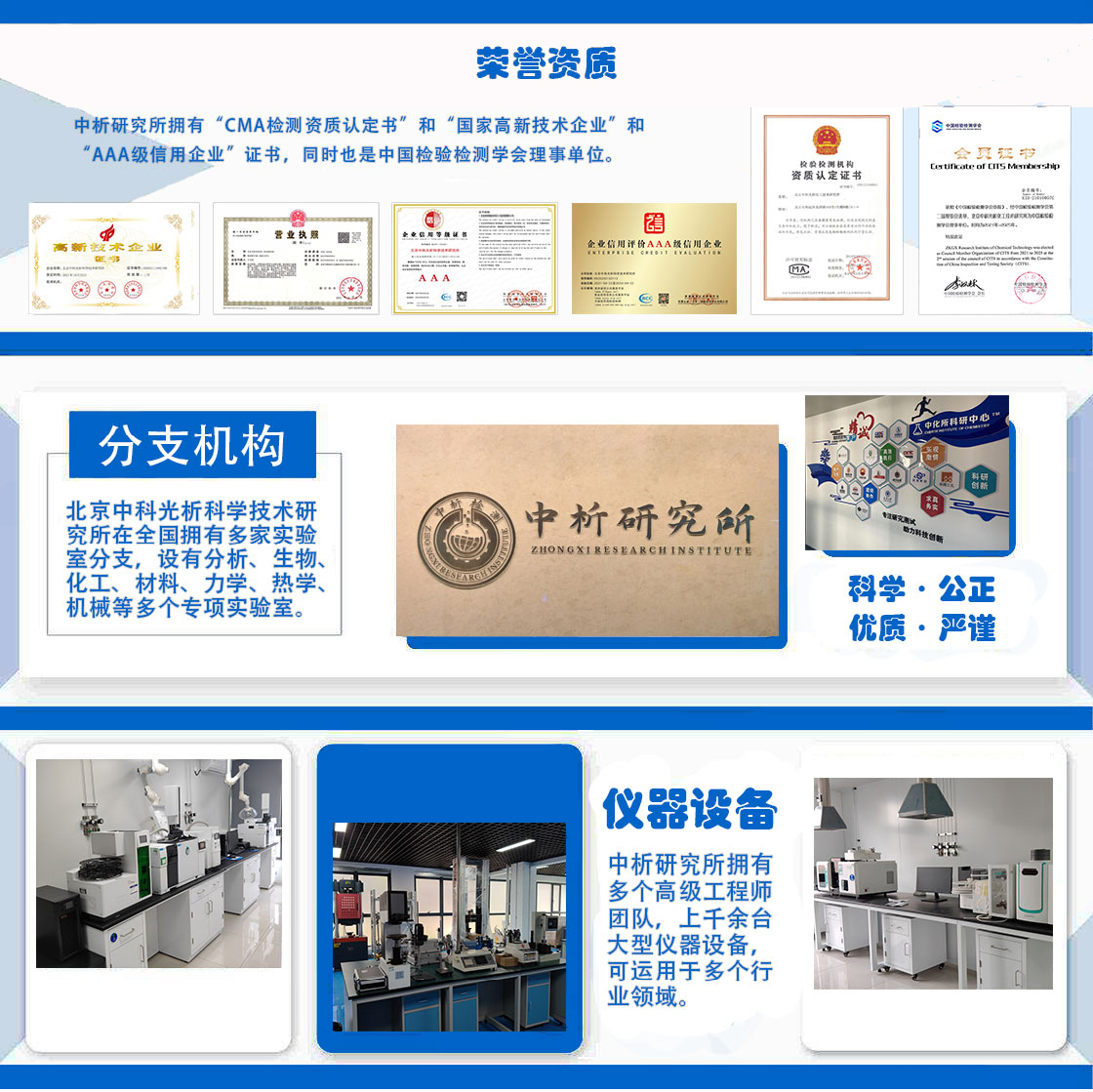
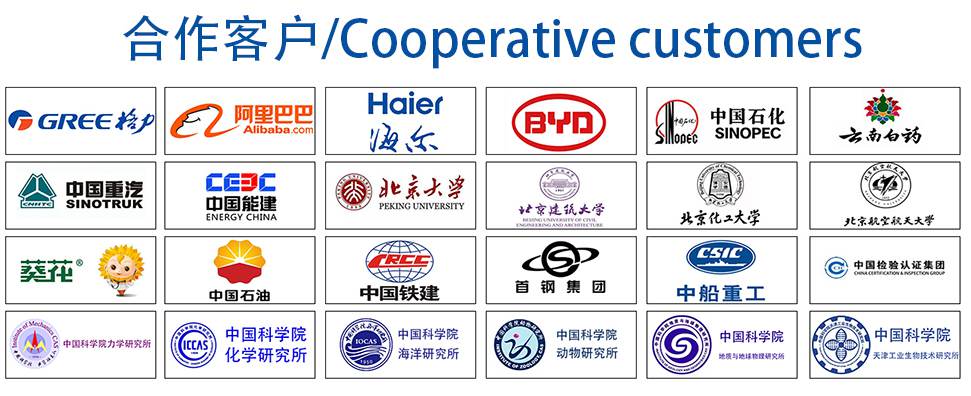