数控立式车床检测的重要性及核心项目分析
数控立式车床作为现代制造业中加工大型盘类、环类及复杂回转体零件的核心设备,其加工精度、稳定性和可靠性直接影响产品质量和生产效率。随着设备使用时间的增加或生产环境的变化,机床的几何精度、动态性能及控制系统可能发生偏移,导致加工误差增大甚至设备故障。因此,系统化的检测与校准是保障设备长期稳定运行的关键环节。
核心检测项目及技术要求
1. 几何精度检测
通过激光干涉仪、电子水平仪等高精度仪器,重点检测以下指标: - 工作台平面度误差(≤0.02mm/1000mm) - 立柱导轨与工作台面的垂直度(≤0.015mm/500mm) - 主轴径向跳动(≤0.005mm) - 刀架重复定位精度(±0.003mm)
2. 运动精度检测
采用球杆仪和动态误差分析系统评估机床动态性能: - X/Z轴直线运动定位精度(补偿后误差≤0.008mm) - 圆弧插补轮廓精度(圆度误差≤0.01mm) - 反向间隙补偿有效性验证 - 伺服系统响应特性测试
3. 电气与控制系统检测
通过示波器和专业诊断软件完成: - 主轴驱动器电流/电压波动监测(波动值≤±5%) - CNC系统I/O信号响应时效测试 - 急停回路、限位开关功能验证 - 热偏移补偿参数校准
4. 液压与气动系统检测
针对关键辅助系统开展: - 卡盘夹紧力稳定性测试(波动≤±10%) - 油路压力保持能力(30分钟压降≤0.3MPa) - 导轨润滑流量均匀性分析 - 气密封性检测(保压泄漏率≤5%)
5. 切削性能综合验证
通过标准试件加工进行实际验证: - 端面车削表面粗糙度(Ra≤1.6μm) - 阶梯轴直径一致性(公差±0.01mm) - 断续切削工况下的振动监测 - 刀具寿命与切削参数匹配性评估
检测周期与数据管理
建议每500小时运行后开展基础精度检测,每2000小时进行系统性综合检测。所有检测数据应建立数字化档案,通过趋势分析预判部件磨损周期,实现预测性维护。对于高精度加工场景,需在换型生产前追加工艺适应性检测。
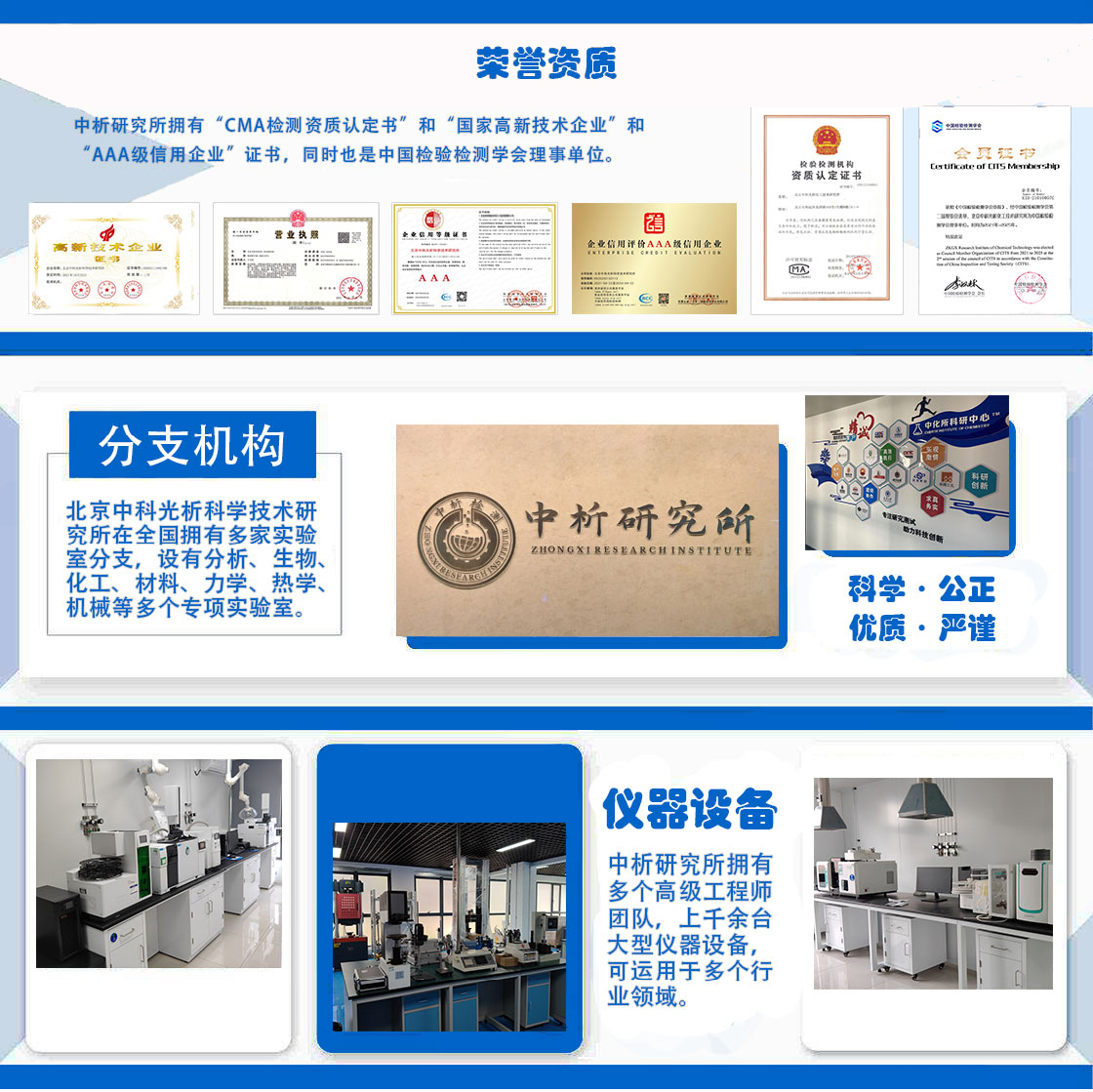
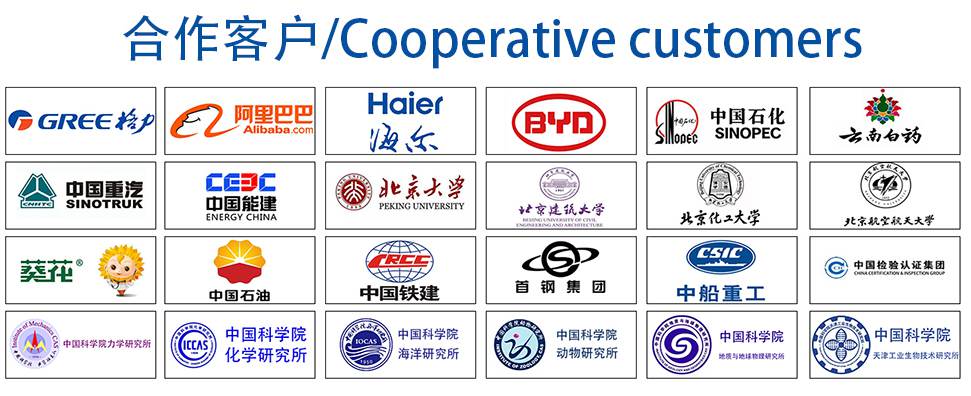