齿轮装置(参数)检测的重要性
齿轮装置作为机械传动系统的核心部件,其性能直接关系到设备运行的平稳性、传动效率及使用寿命。齿轮参数的准确性是确保啮合精度、降低振动噪音、避免早期失效的关键因素。随着工业设备向高速化、精密化方向发展,齿轮装置的参数检测已成为制造、装配及维护环节中不可或缺的流程。通过科学系统的检测手段,能够精准验证齿形、齿距、齿厚、齿向等关键参数的合规性,及时识别加工误差或磨损缺陷,从而保障传动系统的可靠性与安全性。
齿轮参数检测的核心项目
1. 齿形误差检测
齿形误差包括齿廓偏差、压力角误差及齿根过渡曲线异常等,直接影响齿轮的啮合特性。通过齿轮测量机或专用轮廓仪,采用接触式探针或非接触式激光扫描技术,可获取实际齿形与理论设计的偏差数据。检测时需关注渐开线形状的完整性,以及齿顶、齿根区域的圆角过渡是否符合标准(如ISO 1328)。
2. 齿向偏差检测
齿向偏差反映齿轮齿面沿轴向的平行度与螺旋角精度,影响载荷分布的均匀性。通常使用三坐标测量机(CMM)或齿轮啮合检测仪,结合螺旋线扫描功能,分析齿面实际螺旋线与理论值的偏移量。对于斜齿轮和人字齿轮,还需验证螺旋方向的一致性。
3. 齿距累积误差与单齿距误差
齿距误差是评价齿轮周向分布均匀性的重要指标。采用分度盘配合传感器或齿轮测量仪,逐齿测量相邻齿距差及整圈累积误差。该参数异常会导致传动冲击和噪声增大,尤其在高速重载工况下需严格控制(如AGMA 2000标准要求)。
4. 齿厚与齿槽宽检测
齿厚偏差直接影响齿轮侧隙和啮合刚度。传统方法使用齿厚卡尺或公法线千分尺进行接触式测量;现代方案则通过三维扫描技术重建齿面,结合软件计算齿顶圆至齿根的几何参数。需特别注意变位齿轮的修正系数对检测阈值的影响。
5. 表面粗糙度与硬度检测
齿面粗糙度影响摩擦磨损性能,通常采用轮廓仪或白光干涉仪进行微观形貌分析。硬度检测则使用维氏或洛氏硬度计,验证渗碳淬火、氮化等表面处理工艺的深度与均匀性,确保齿轮的抗点蚀和抗胶合能力。
6. 齿轮副综合性能测试
在装配状态下,通过双啮仪或传动误差测试台,对齿轮副进行空载/负载下的传动精度、振动噪声及温升测试。此阶段可发现安装偏心、轴线平行度偏差等系统性问题,并为动态参数优化提供数据支持。
检测技术的发展趋势
随着智能制造的推进,齿轮参数检测正朝着高精度、自动化和数字化方向发展。基于机器视觉的在线检测系统、结合AI算法的缺陷识别技术,以及多传感器融合的实时监控方案,显著提升了检测效率与可靠性。未来,检测数据与加工设备的闭环反馈机制将推动齿轮制造进入“零缺陷”时代。
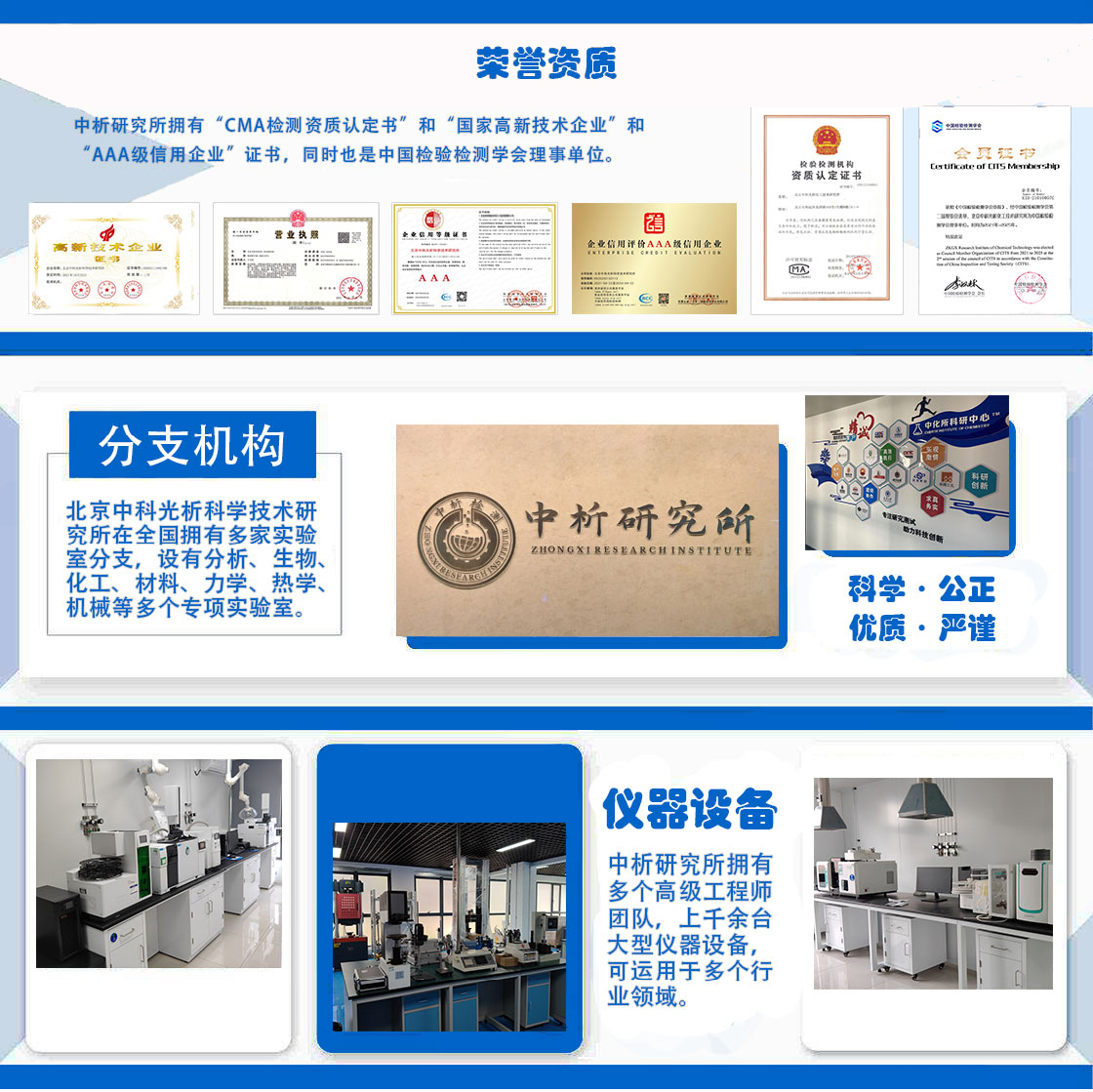
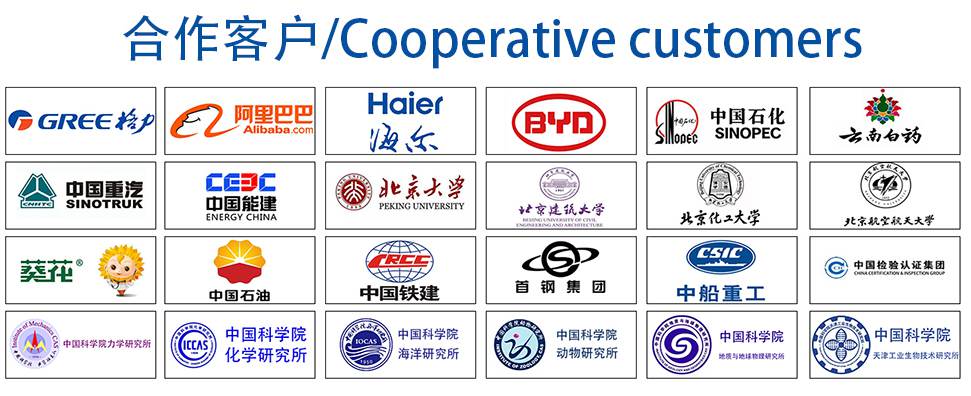