吨压力小时生产率检测
一、检测前的准备工作
-
- 检查设备润滑系统、液压系统、电气控制系统是否正常。
- 验证压力表、传感器、计时器等检测工具的校准状态。
-
- 明确额定压力(吨位)、行程长度、工作速度等工艺参数。
- 记录模具型号、材料类型及工件规格(如厚度、尺寸)。
二、核心检测项目及方法
1. 设备基础性能检测
-
- 方法:使用压力传感器或测力计测定实际输出压力与设定值的偏差(通常要求≤±5%)。
- 标准:参考ISO 7500-1(金属材料静态单轴向试验机的校准)。
-
- 方法:连续记录10次完整作业周期(从加压到复位),计算平均值。
- 关键指标:单次循环时间(秒),直接影响小时产能。
2. 小时生产率计算验证
-
- 公式: 理论产能(件/小时)=3600单次循环时间(秒)理论产能(件/小时)=单次循环时间(秒)3600
-
- 方法:连续运行设备1小时,统计合格工件数量,剔除故障停机时间(如卡料、维修)。
- 影响因素:设备稳定性、操作人员熟练度、物料供应节奏。
3. 质量关联性检测
-
- 检测项:尺寸精度、表面无开裂/变形、装配兼容性。
- 方法:每小时随机抽取10~20件样品,按工艺标准判定合格率。
-
- 检测项:压力波动是否导致工件厚度不均或强度差异。
4. 能耗效率检测
- 单位产量能耗
- 公式: 能耗比(kW\cdotph/件)=设备总耗电量(kW\cdotph)实际产量(件)能耗比(kW\cdotph/件)=实际产量(件)设备总耗电量(kW\cdotph)
- 优化方向:降低空载能耗、优化液压系统效率。
5. 设备稳定性与故障率
- 连续运行测试
- 方法:持续运行4~8小时,记录异常停机次数与原因(如油温过高、压力泄漏)。
- 指标:平均无故障工作时间(MTBF)。
三、数据分析与改进建议
- 效率瓶颈诊断
- 对比理论产能与实际产能,识别时间损耗环节(如上料延迟、模具更换耗时)。
- 优化方案示例
- 调整压力曲线参数,缩短空行程时间;
- 采用自动化送料装置,减少人为干预;
- 定期保养液压系统,避免压力泄漏导致的重复加压。
四、检测报告模板(摘要)
检测项目 | 标准值 | 实测值 | 偏差分析 |
---|---|---|---|
压力吨位精度 | 1000吨 | 975吨 | -2.5% |
单次循环时间 | 12秒 | 14秒 | +16.7% |
实际小时产能 | 300件 | 250件 | -16.6% |
合格率 | ≥98% | 95% | 模具磨损 |
五、注意事项
- 检测需模拟实际生产条件,避免实验室环境与车间工况差异;
- 长期监测数据更可靠,建议结合物联网(IoT)技术实现实时采集。
上一篇:沙拉洛菌素(拉沙里菌素、沙拉洛西钠)检测下一篇:玉米粉质量检测
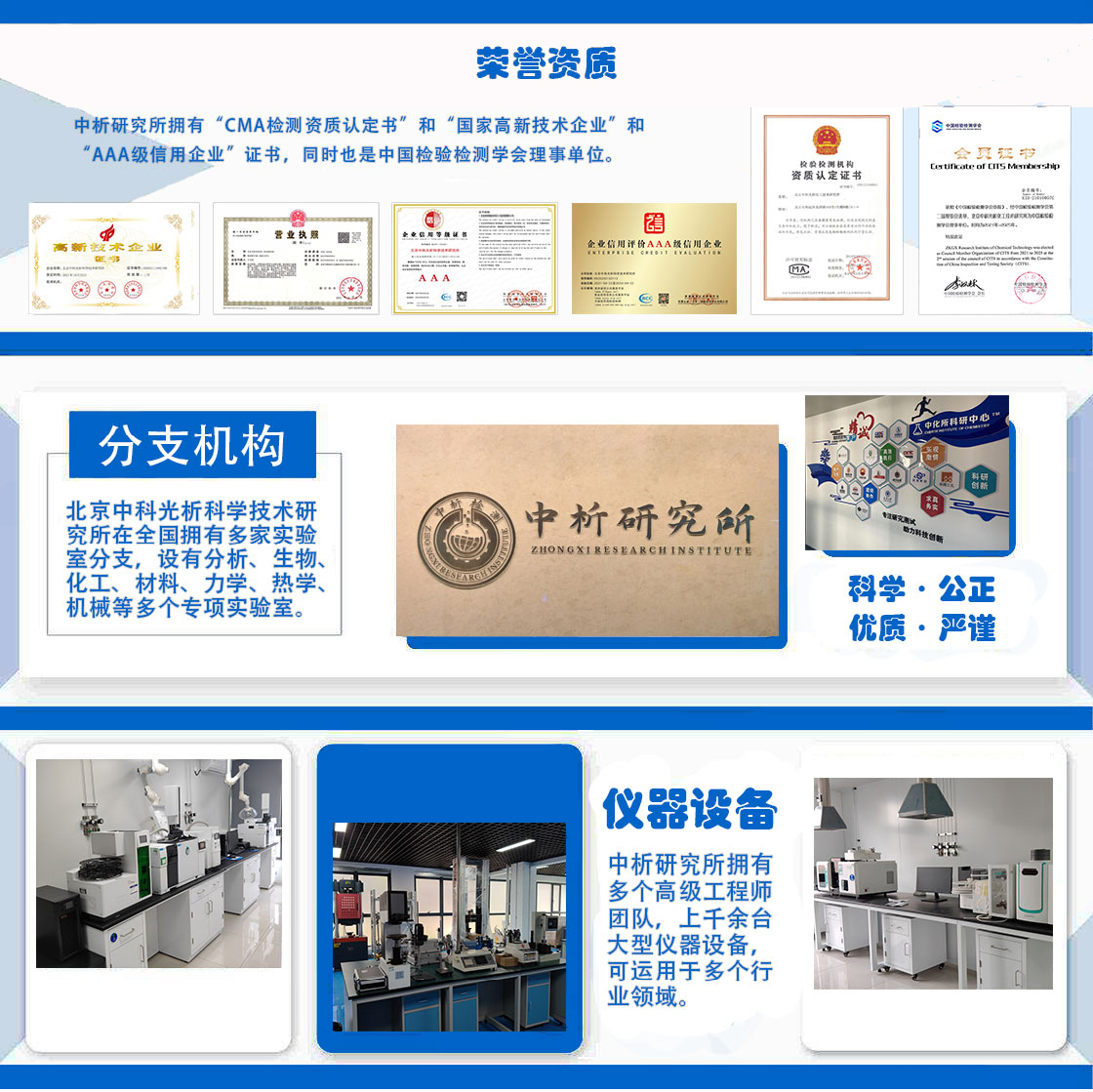
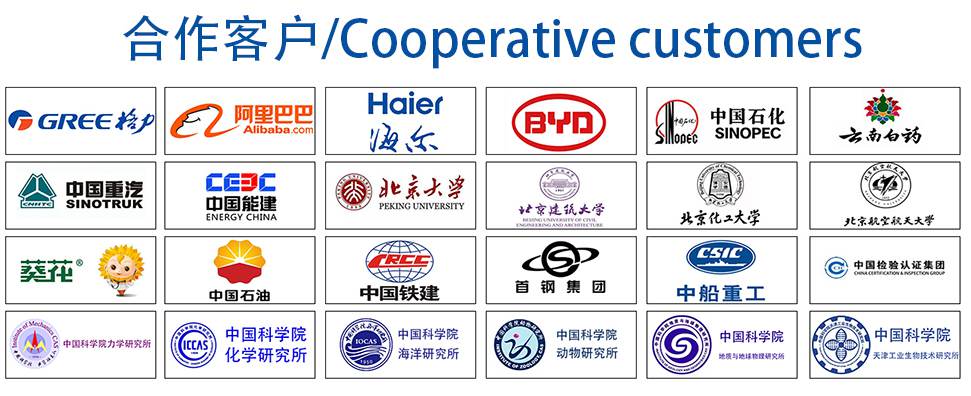
材料实验室
热门检测
推荐检测
联系电话
400-635-0567