一、检测前的准备工作
- 设备停机与安全锁定
- 切断电源并挂牌上锁,确保设备处于静止状态。
- 清理磨片表面残留物料,避免污染测量工具。
- 工具校准
- 使用精度达±0.001mm的激光测距仪、塞尺或千分尺。
- 校验工具的基准值,确保测量误差<0.5%。
二、核心检测项目与操作规范
1. 静态间隙精度检测
- 检测目标:测量上下磨片间的最小距离与设定值的偏差。
- 方法:
- 三点测量法:在磨片圆周120°均布位置插入标准塞尺,取平均值。
- 激光扫描:通过非接触式激光仪生成间隙3D分布图,识别局部异常点。
- 标准:允许误差范围通常为±0.02mm(精加工设备需≤±0.01mm)。
2. 平行度检测
- 检测目标:确保磨片工作面在运转中保持平行。
- 方法:
- 使用千分表固定于主轴,旋转一周读取径向跳动值。
- 对角四点法:测量磨片四角间隙,偏差应<0.03mm/100mm。
- 修正措施:通过液压微调系统或垫片补偿非平行区域。
3. 动态间隙稳定性测试
- 检测目标:验证设备负载运行时间隙的波动。
- 方法:
- 空载启动设备至额定转速,用高速摄像仪记录磨片振动幅度。
- 模拟负载运行,监测间隙变化率(如波动>10%需停机调整)。
4. 磨片表面磨损评估
- 检测项:
- 厚度均匀性:用超声波测厚仪检测边缘与中心厚度差(>0.05mm需修复)。
- 表面粗糙度:触针式轮廓仪测量Ra值,粗糙度突变区域需标记。
- 处理建议:累计磨损量超过初始厚度5%时,建议更换磨片。
三、环境与工艺影响因素校准
- 温度补偿
- 金属磨片需按膨胀系数(如钢:11.7×10⁻⁶/℃)修正高温工况下的间隙。
- 物料特性匹配检测
- 硬质物料(如石英)需加大间隙0.05-0.1mm,软质物料(如塑料)则缩小间隙。
- 轴向预紧力测试
- 通过扭矩扳手检测轴承预紧力,避免因松动导致间隙偏移。
四、检测周期与数据管理
- 高频检测:连续生产的设备每8小时抽检1次关键点。
- 大数据分析:记录历史数据并建立趋势模型,预测下次调整时间(如间隙月均扩大0.03mm时,设定预警阈值)。
五、常见故障诊断案例
- 案例1:某粉碎机出料粒度不均
- 检测发现:磨片南侧间隙较北侧大0.08mm,平行度超标。
- 解决方案:调节液压缸压力分配,校正后产品合格率提升32%。
- 案例2:设备异常振动
- 检测发现:动态测试中某转速下间隙周期性突变0.05mm。
- 原因定位:主轴轴承磨损导致径向跳动,更换后振动值下降70%。
六、行业标准参考
- ISO 12100: 机械安全设计规范(间隙安全阈值)。
- GB/T 11347: 旋转机械振动测量标准(动态检测部分)。
- 企业定制标准:如食品级设备需满足间隙残留率<0.01%的清洁度要求。
结语
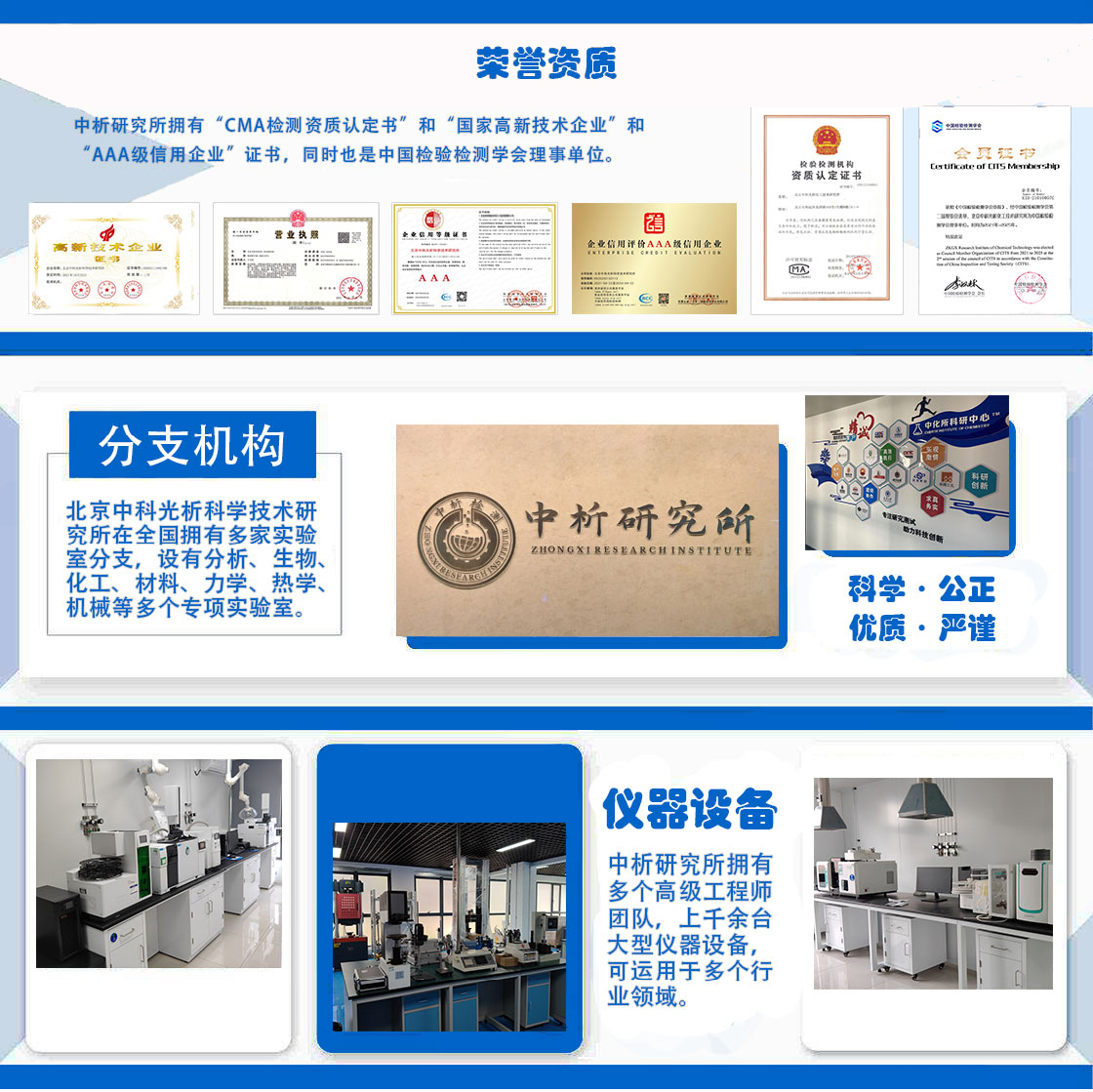
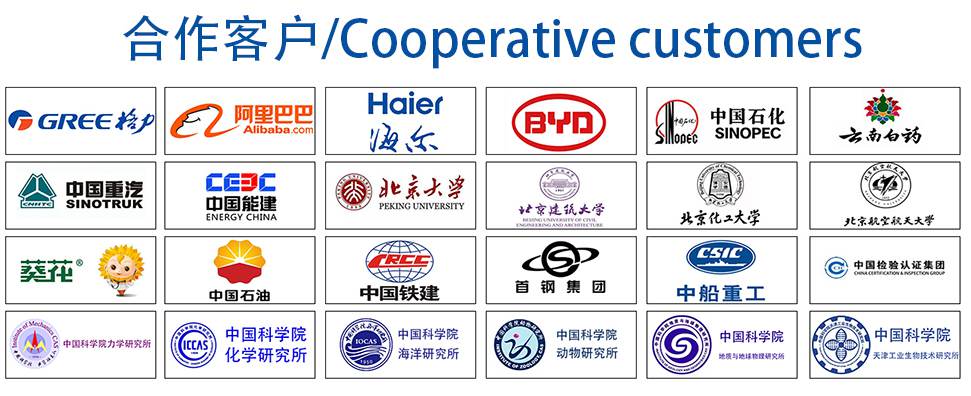
材料实验室
热门检测
推荐检测
联系电话
400-635-0567