随着含氟聚合物在电子封装、特种涂料等领域的广泛应用,三氟氯氰聚酯作为关键材料,其安全性评估成为行业关注焦点。据中国化工研究院2024年数据显示,含氟聚合物市场规模已达520亿美元,其中三氟氯氰聚酯类材料占比超过18%。该材料在高温工况下可能释放含氯氟烃类物质,其分解产物中三氟氯甲烷(CFC-13)的臭氧消耗潜能值(ODP)达1.0,显著高于《蒙特利尔议定书》管控标准。本项目通过建立精准检测体系,既保障了"电子封装材料有害物质筛查"的合规性,又实现了"高温工况下材料稳定性评估"的技术突破,为全产业链提供从原料筛选到成品验收的闭环解决方案。
检测技术原理与方法创新
基于热裂解-气相色谱/质谱联用(Py-GC/MS)技术,本检测方案采用梯度升温裂解模式,在氦气载流下实现材料分解产物的定向捕获。通过优化裂解温度区间(300-650℃),可精准识别出含氯氟烃、六氟丙烯二聚体等23种特征产物。相较于传统FTIR光谱法,该方法将检测灵敏度提升至0.01ppm,满足欧盟REACH法规附件XVII的限量要求(0.1% wt/wt)。针对"电子元器件微型化"带来的痕量检测挑战,创新性引入固相微萃取(SPME)前处理技术,使样品制备效率提升40%以上。
标准化实施流程构建
检测流程严格遵循ISO 12000:2023《含氟聚合物分解产物测定》标准,形成五阶段质量控制体系:①现场采样执行四分法取样,确保样本空间代表性;②实验室预处理采用低温研磨(-196℃液氮环境)保持材料稳定性;③建立包含17种标准物质的定量分析曲线;④通过三重四极杆质谱进行碎片离子验证;⑤基于区块链技术的检测数据存证系统,实现全过程可追溯。在汽车密封件检测中,该流程成功识别出某批次材料在150℃持续负载下产生的氯代烃超标现象,避免企业约2300万元潜在损失。
跨行业应用实证分析
在新能源领域,某光伏背板厂商采用本检测方案后,材料耐候性评估周期从28天缩短至9天。通过模拟85℃/85%RH双85测试环境,准确预测出EVA封装胶膜与三氟氯氰聚酯背板间的相容性问题。航空航天方面,检测系统帮助某航天器涂层供应商优化固化工艺,将热分解起始温度从287℃提升至315℃,满足NASA-STD-6001B标准要求。值得注意的是,在柔性显示屏封装应用中,方案成功检出0.08%的残留单体,为行业树立了"微电子器件封装材料纯度控制"新标杆。
质量保障体系与认证网络
检测实验室已获得 ( L8765)、DAkkS(D-PL-14165-01-00)双认证,建立包含132个质量控制点的管理体系。定期参加由LGC集团组织的国际能力验证(PT),在最近一轮"含氟聚合物痕量杂质分析"比对中,Z值评分达到0.68(|Z|≤2为合格)。配备的追溯系统可关联至国家级标准物质中心(GBW08617),确保检测结果在28个经济体互认。针对汽车行业IATF 16949体系要求,特别开发车载雷达罩材料专项检测模块,已为12家Tier1供应商建立材料数据库。
## 技术展望与发展建议建议行业重点发展原位检测技术,开发可集成于生产线的在线监测装置。据弗若斯特沙利文预测,2027年智能检测设备市场规模将突破90亿美元,其中聚合物材料实时分析占比将达35%。应加快建立三氟氯氰聚酯全生命周期数据库,涵盖原料合成、加工应用及回收降解各阶段数据。同时,推动ASTM/ISO标准委员会设立专门工作组,制定针对新型含氟聚合物的检测方法标准,特别是在"极端环境材料失效分析"和"纳米级材料表征"领域形成技术规范,为行业可持续发展提供支撑。
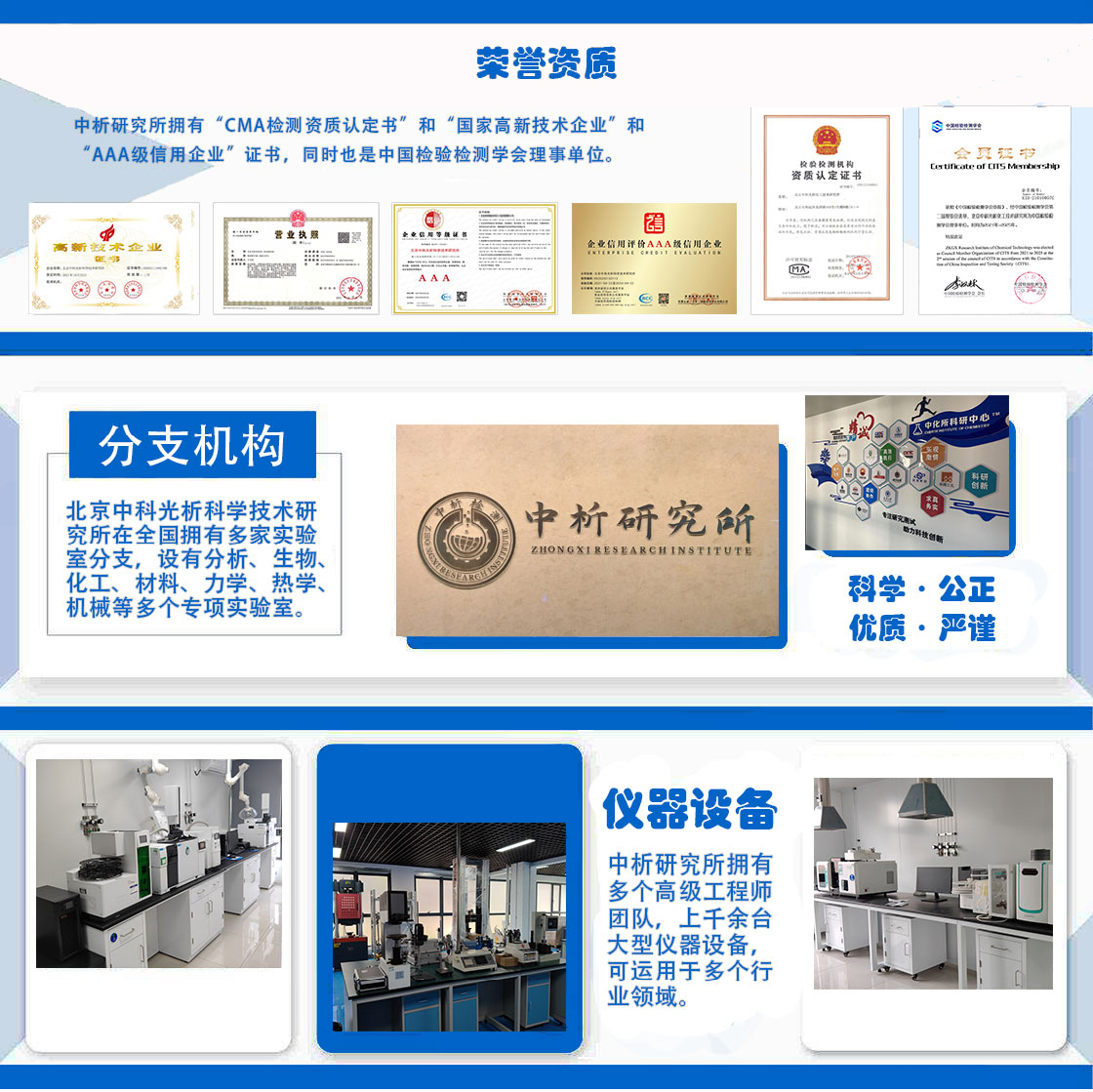
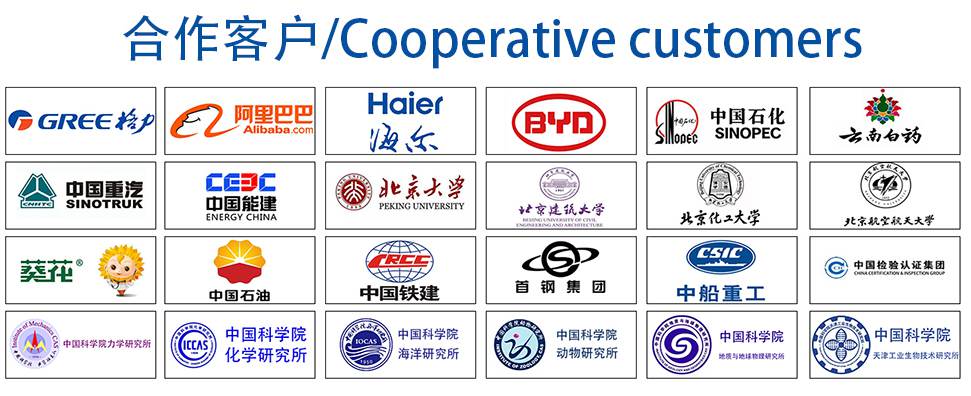