光反射值和小色差检测:精密制造中的色彩质量控制实践
在高端制造领域,表面色彩一致性已成为衡量产品品质的核心指标之一。据中国表面工程研究院2024年数据显示,因色差问题导致的工业品退货率高达2.3%,直接经济损失超过120亿元/年。光反射值和小色差检测技术通过量化分析材料表面光学特性,为汽车漆面、电子产品外壳、包装印刷等场景提供了精准的质量控制手段。其核心价值在于突破人眼辨色极限,实现ΔE≤0.5的工业级色差控制,配合智能化检测系统可将产线良率提升18%以上(数据来源:《智能检测技术白皮书2024》)。该技术体系正推动制造业从经验判断向数据驱动的质量管控模式转型。
技术原理与光谱分析体系
基于CIE Lab色彩空间理论,检测系统通过分光光度计获取物体表面380-780nm光谱反射率曲线,结合标准光源D65模拟人眼视觉响应。采用双光束差分技术消除环境光干扰,测量精度可达反射率±0.1%、色度坐标±0.0005。通过建立色差公式ΔE=(ΔL²+Δa²+Δb²)^½实现量化评价,其中ΔL表征明度差异,Δa、Δb对应红绿、黄蓝轴偏移量。针对金属漆、珠光粉等特殊材质,系统搭载多角度测量模块,可在15°、45°、110°观测角下同步采集数据。
智能化检测工艺流程
完整的检测流程包含设备校准、标准样板建立、在线检测三大环节。首先使用NIST溯源的标准白板进行仪器校准,确保测量偏差≤0.2ΔE。在汽车漆面检测场景中,工程师通过MES系统导入色板LAB值,设置允许波动范围ΔE≤0.8。产线集成机器人搭载的非接触式探头可在0.8秒内完成单点检测,配合机器学习算法自动识别色差分布规律。某日系车企应用该方案后,整车外观缺陷率从3.1%降至0.7%(丰田技术报告2024Q1)。
跨行业应用实践
在消费电子领域,某头部手机厂商采用"手机壳体同色异谱分析技术",成功解决铝合金阳极氧化件的批次色差问题。通过建立200组工艺参数与色度值的对应关系模型,将色差合格率从78%提升至96.5%。包装印刷行业应用"专色油墨自动校色系统"后,校色时间缩短60%,材料浪费减少45%。值得关注的是,3C产品表面处理工艺正向纳米级精度发展,这对检测设备的分辨率提出更高要求。
全生命周期质量保障
检测体系构建需遵循ISO 17025实验室管理规范,实施三级校验机制:每日进行标准色板比对,每周开展设备间交叉验证,每季度参与ILAC国际比测。数据管理系统采用区块链技术存储检测记录,实现10年可追溯性。某德系汽车涂料供应商通过该体系,将客户投诉率降低至0.03ppm(2023年度质量报告),并成功通过IATF 16949认证。
随着新材料和新工艺的不断涌现,行业亟待建立跨领域的色差检测标准体系。建议从三方面突破:一是开发适应柔性屏、微弧氧化等新型表面的检测方法;二是推动光谱数据库的行业共享;三是探索AI赋能的预测性色差控制技术。通过将光学检测深度嵌入智能制造系统,有望实现从"缺陷检测"到"缺陷预防"的范式转变,为工业4.0时代的精密制造提供核心质量保障。
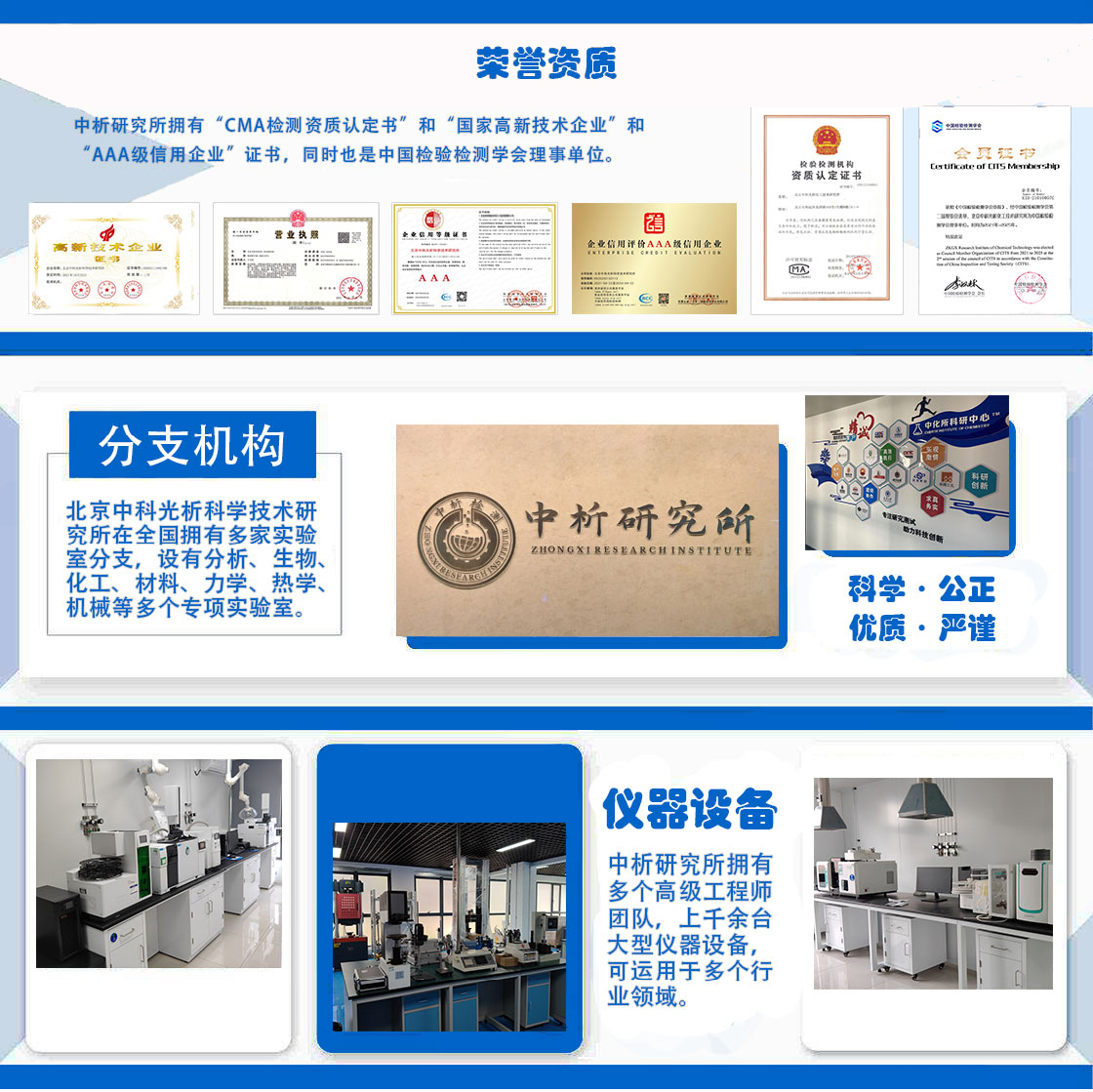
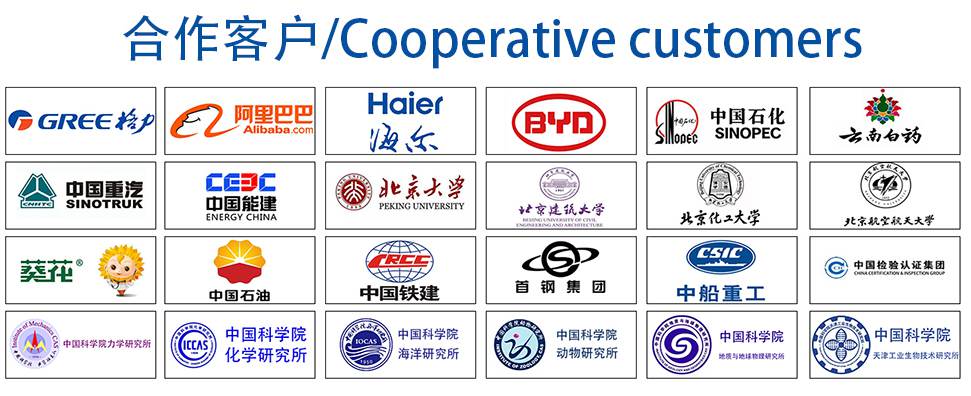