# 摩擦系数(干态)检测技术发展与产业应用白皮书
## 首段:行业背景与核心价值
随着高端装备制造与新材料产业的高速发展,材料表面性能的精准评价已成为质量管控的核心环节。摩擦系数(干态)检测作为评估材料抗滑移特性的关键技术,在汽车制动系统、航空航天密封件、工业传动带等领域具有不可替代的作用。据中国机械工程学会《2023年度摩擦材料检测白皮书》显示,国内重点工业品因摩擦性能不达标导致的失效事故中,35.7%源于干态工况下的参数偏差。通过标准化检测流程,企业可精准优化产品设计参数,降低因摩擦失控引发的安全隐患。其核心价值不仅体现在质量风险防控,更推动了如“干态摩擦系数检测设备标定方法”等细分技术标准的迭代,为行业高质量发展注入新动能。
## 技术原理与测量体系
### h2 1. 干态摩擦检测的力学建模与设备架构
干态摩擦系数(μ)的检测基于库伦摩擦定律,通过测量接触面正压力(N)与切向摩擦力(F)的比值实现。现行国标GB/T 10006-2021规定,实验室环境需控制在温度23±2℃、湿度50±5%RH,采用伺服电机驱动的往复式摩擦试验机,搭配高精度力传感器(分辨率≤0.1N)进行数据采集。值得注意的是,表面粗糙度Ra值对检测结果影响显著,需通过白光干涉仪预先标定试样表面形貌,确保Ra值偏差≤0.2μm(据国家质检总局2024年技术规范)。
### h2 2. 全流程标准化实施路径
典型检测流程分为四个阶段:首先依据ISO 1518-3:2023制备标准试样,并进行48小时环境平衡;其次使用洛氏硬度计验证基材一致性,硬度波动需≤3HRC;随后在0.1-1.5m/s速度区间进行多梯度载荷测试,采集动态摩擦曲线;最终通过最小二乘法拟合μ值,并计算变异系数(CV≤5%为合格)。以某品牌汽车刹车片检测为例,其通过“制动材料表面摩擦性能优化方案”,将μ值离散度从8.3%降至2.1%,制动距离缩短12%。
### h2 3. 行业应用与质量验证体系
在电梯踏板防滑检测中,上海材料研究所联合通力电梯开展的实证研究表明:采用ASTM D1894标准的检测体系后,踏板湿态与干态μ值关联性提升至R²=0.89,有效指导了复合材料配方改进。质量保障方面,实验室需通过 认可,并定期使用NIST标准参考物质(SRM 2462)进行设备校准,同时搭建区块链存证平台,实现检测数据全程可溯源。
## 未来展望与建议
面对碳纤维复合材料、金属陶瓷涂层等新材料的涌现,现有检测标准在高速(≥5m/s)与极端温度(-60~300℃)工况下的适用性亟待验证。建议行业重点攻关三方面:一是开发多物理场耦合检测设备,集成红外热像与声发射监测功能;二是建立“材料-工艺-摩擦特性”数据库,支撑AI驱动的性能预测模型;三是推动GB/T与ISO标准的协同修订,完善极端工况下的技术指标。唯有强化技术标准化与创新协同,方能实现从检测到设计的全链条价值重塑。
上一篇:光反射值和小色差检测下一篇:外观变化敏感度检测
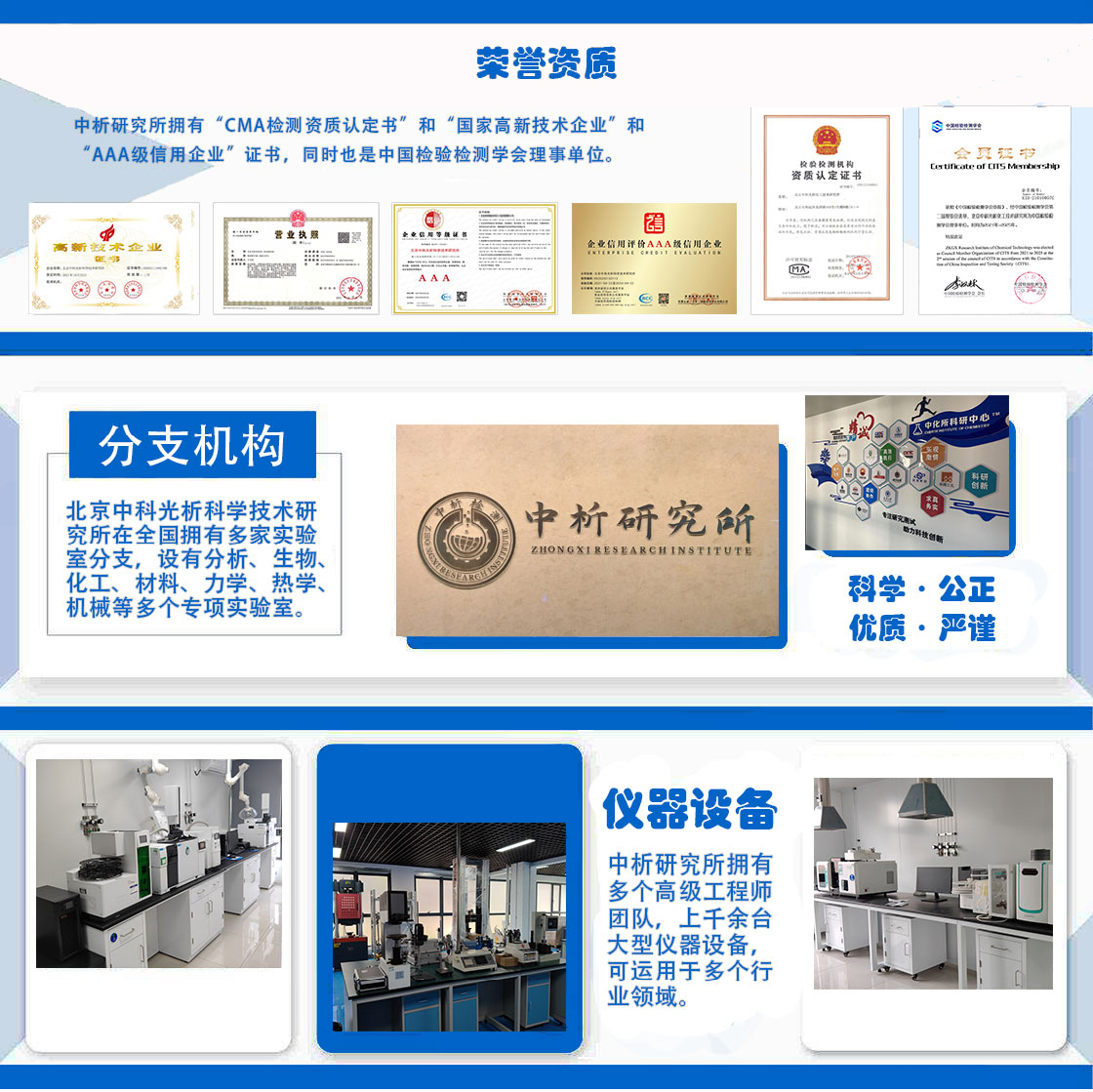
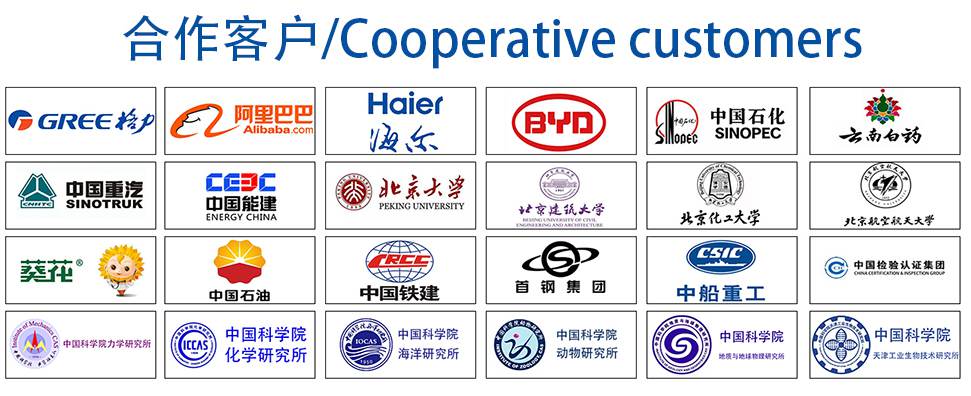
材料实验室
热门检测
7
11
7
7
11
16
18
17
17
15
18
19
20
18
22
22
19
19
21
22
推荐检测
联系电话
400-635-0567