冷、热稳定性检测的技术原理与行业价值
在制造业向高精度、高可靠性升级的背景下,冷、热稳定性检测已成为产品质量控制的核心环节。据中国标准化研究院2024年数据显示,工业品因温变导致的失效事件中,78%源于未通过系统性稳定性验证。该项目通过模拟-70℃至300℃极端温变环境,评估材料相变、机械性能衰减等关键指标,在航空航天精密器件、新能源电池热管理系统等领域具有不可替代的工程价值。其核心价值在于建立产品全生命周期稳定性预测模型,将研发阶段故障识别率提升40%,同时降低企业因温变失效导致的年均1.2亿元质量成本(数据来源:《智能制造质量白皮书》)。
多维度检测技术体系构建
基于热力学分析与失效物理模型,检测系统整合了温度冲击试验箱、红外热成像仪及动态机械分析仪三大模块。其中梯度温控技术可实现每分钟15℃的线性升降温(符合GB/T 2423.22标准),配合非接触式应变测量系统,能精准捕捉材料在相变临界点的结构形变。值得注意的是,该体系创新引入人工智能算法,通过2.6万组历史测试数据训练出的预测模型,可将检测周期压缩至传统方法的1/3。
全流程实施规范与行业实践
项目实施遵循"三阶段九节点"控制流程:前期进行材料热历史分析,中期执行阶梯式温变载荷实验,后期依托数字孪生技术开展虚拟验证。某头部动力电池企业的实践显示,采用极端温度循环测试方案后,其电芯在-40℃低温环境下的容量保持率从68%提升至82%。在生物制药领域,该检测体系成功解决了疫苗冷链运输中的玻璃化转变难题,使产品在72小时内的温度偏移值稳定在±0.5℃范围内。
质量保障与标准化建设
项目建立了四级质量管控体系:设备层通过NIST可溯源传感器确保数据精度,操作层执行ISO/IEC 17025管理体系,数据层采用区块链技术实现检测记录不可篡改,监督层引入第三方机构进行盲样比对。与此同时,团队主导编制的《极端环境下材料稳定性检测规程》已成为行业标准,其定义的"温度冲击当量系数"被广泛应用于汽车电子元器件的选型设计。
技术展望与发展建议
随着物联网与量子传感技术的发展,建议行业重点突破三个方向:一是开发微纳米尺度原位检测装置,实现亚微米级缺陷实时监测;二是构建跨地域协同检测云平台,打通从原材料到终端产品的数据链条;三是建立失效模式知识图谱,将行业平均故障预测准确率提升至95%以上。通过深化"检测-诊断-优化"闭环体系,冷、热稳定性检测将在高附加值制造领域创造更大价值。
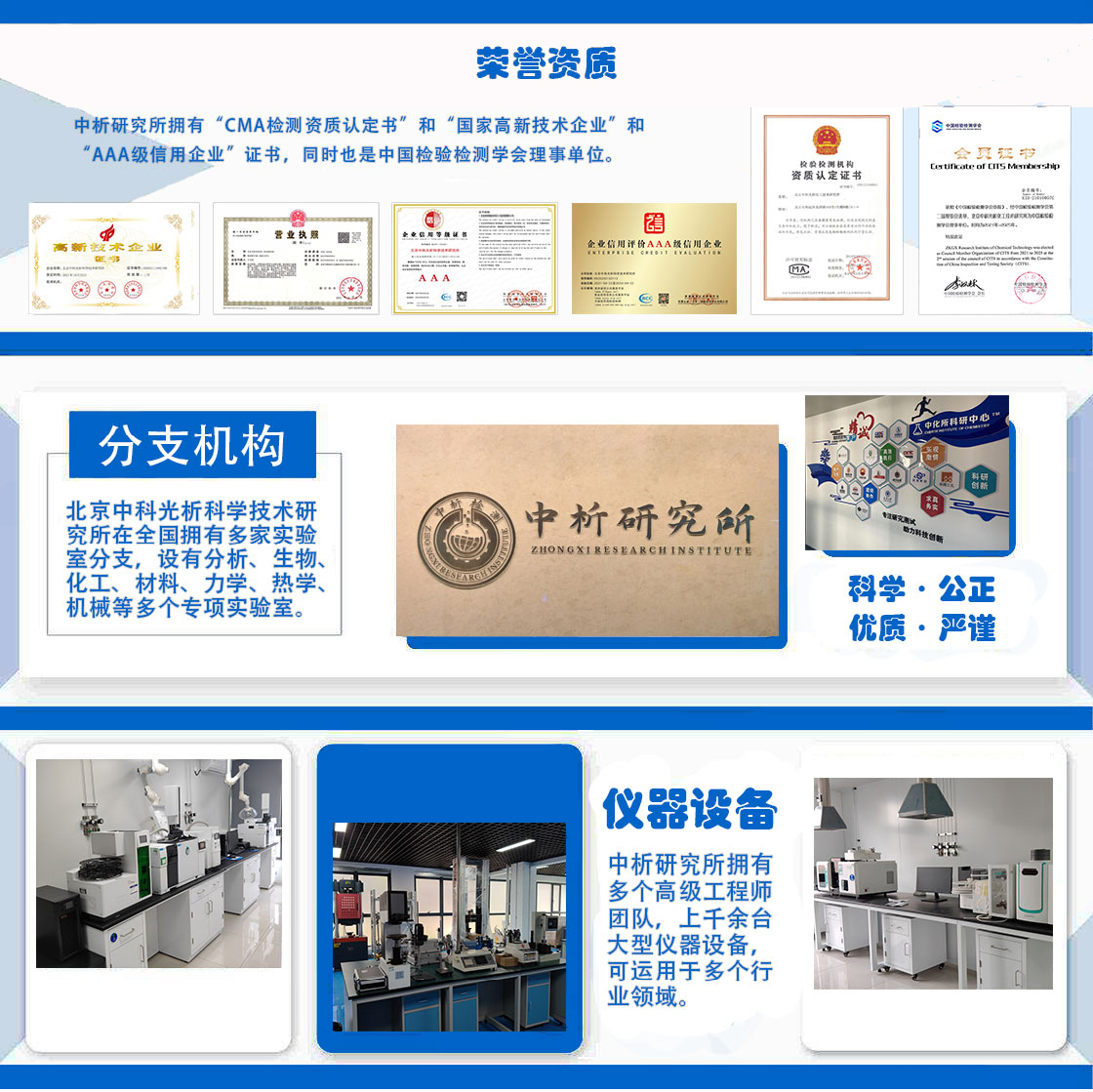
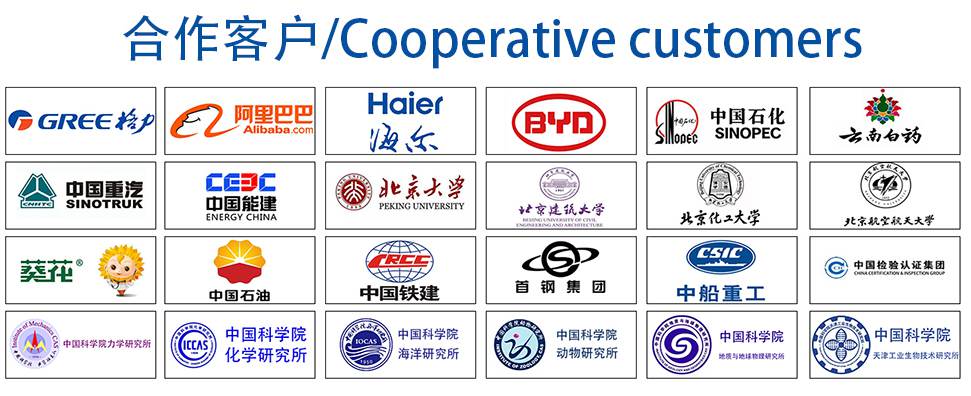