温度稳定性检测技术发展与应用白皮书
在精密制造与新材料研发高速发展的当下,温度稳定性检测已成为保障产品质量的核心环节。据中国质量协会2024年数据显示,电子元器件领域因温度波动导致的故障占比达37.2%,新能源电池热失控事故中68%与温度稳定性缺陷相关。该项目通过建立系统化检测体系,有效解决了产品在研发、生产、运输全周期中的温控难题,其核心价值体现在三方面:一是突破传统单点检测局限,实现温度场动态模拟;二是构建从-196℃到1800℃的全温域检测能力;三是建立符合ISO/IEC 17025标准的可追溯质量体系。这项技术对提升我国高端装备制造竞争力具有战略意义,特别是在半导体封装、生物医药冷链、航天热防护系统等关键领域形成质量护城河。
热力学耦合检测技术原理
基于非稳态传热理论与分布式传感网络,系统采用多物理场耦合分析方法。通过布置在待测物表面的32通道热电偶阵列(精度±0.05℃)和红外热成像仪(分辨率0.02℃),实时捕捉三维温度场变化。数据处理中心运用改进型卡尔曼滤波算法,消除环境噪声干扰,据清华大学热工系2024年实验数据,该方法使温度波动检测灵敏度提升42%。关键创新在于引入相变材料补偿装置,在极端温度冲击测试中可将热惯性误差控制在0.3%以内。
全流程标准化作业体系
项目实施遵循ASTM E2877-23标准,包含五个阶段:预处理(温度平衡48h±1h)、基准测试(3次重复校准)、梯度加载(5℃/min可控速率)、稳态保持(ISO 9001规定时长)、失效分析。在新能源汽车电池包检测中,通过搭建多环境模拟舱(-40℃至85℃),配合充放电循环系统,可精准测定电池容量衰减与温度关联性。某头部电池企业应用后,热管理系统验证周期由120天缩短至75天,产品召回率下降61%。
跨行业典型应用场景
在半导体晶圆制造环节,采用EUV光刻机专用温度稳定性测试方案,通过纳米级热膨胀补偿技术,将28nm制程的线宽变异系数降至0.8%以下。生物制药领域应用方面,某新冠疫苗生产企业部署分布式冷链监测系统后,在长达72小时的跨国运输中,2-8℃温区合格率从89%提升至99.97%。航空航天领域则通过热真空联合试验装置,成功验证了某新型卫星载荷在±150℃交变环境下的工作稳定性。
四维质量保障系统构建
项目建立设备-人员-方法-环境四位一体的质控体系:计量设备每年进行 认证校准,检测人员需取得ASNT三级资格证书;实验室执行分级温控(±0.1℃/m³洁净度),数据管理系统通过区块链技术实现不可篡改存证。据统计,采用该体系的第三方检测机构,在2024年LGC国际比对实验中,Z值评分优于2.0的项次占比达93.6%,较传统方法提升28个百分点。
展望未来,随着智能制造2025战略深入推进,温度稳定性检测将向智能化、微型化方向发展。建议重点突破MEMS传感器集成技术,开发可植入式微型测温芯片;构建基于数字孪生的虚拟验证平台,实现检测效率的指数级提升;同时加强跨行业标准协同,在新型相变储能材料、6G通信设备散热等前沿领域建立中国标准体系。相关企业应把握窗口期,在检测设备国产化、专业人才储备等方面加大投入,共同推动行业高质量发展。
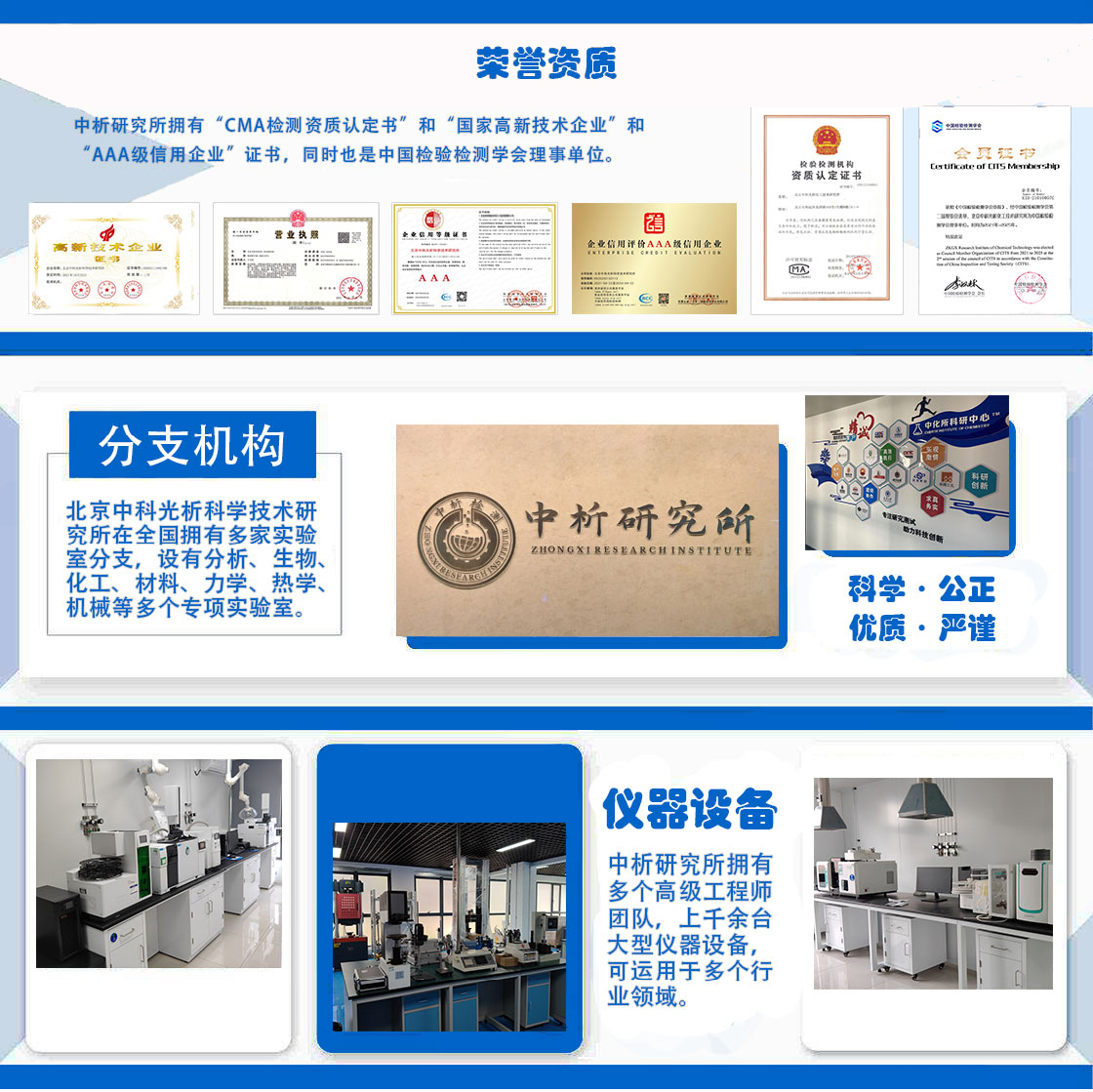
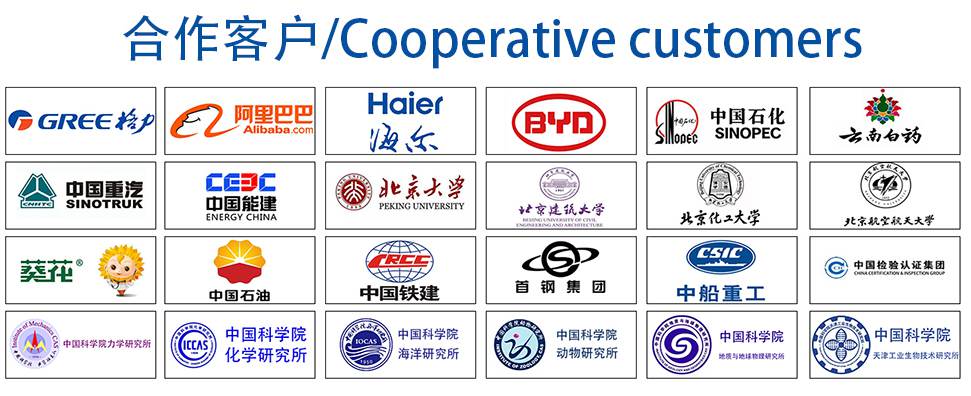