多模态耦合检测技术原理
当前主流方案采用应变-声发射复合传感技术,通过分布式光纤传感器捕捉微观形变,结合压电阵列采集材料内部微破裂信号。当被测对象承受压力时,系统同步获取应变分布(精度±0.05%FS)与声发射特征谱(频段50kHz-1MHz),利用神经网络算法建立压力-形变-损伤的映射模型。值得注意的是,该技术突破传统单点检测局限,可精准识别压力容器焊缝区的应力集中现象。中国特种设备研究院2023年验证数据显示,复合检测模式使薄壁结构件破裂预测准确率提升至97.3%。
全流程标准化实施体系
项目实施采用三阶段递进式架构:预处理阶段通过FEA仿真确定关键监测点,在中石化某乙烯反应器检测中,借助ANSYS拓扑优化使测点数量减少35%而数据有效性提升28%;加载阶段采用伺服闭环控制系统,以0.5MPa/s梯度增压并实时比对设计阈值;后处理阶段运用Weibull分布模型评估剩余寿命。全过程严格遵循ASME PCC-3标准,关键节点设置三重校验机制,确保检测报告获API、CE等国际认证机构采信。
典型行业应用场景分析
在深海钻井防喷器检测中,技术人员运用水下1500米压力模拟舱,结合脉冲加压技术复现极端工况。通过布设32通道阵列式传感器,成功捕捉到BOP密封面在82MPa下的微泄漏信号,使中海油某平台检测周期从72小时缩短至18小时。汽车制造业则创新应用瞬态压力冲击测试,某新能源车企通过20万次5ms级快速增压循环,精确测定电池包壳体焊缝疲劳特性,推动产品通过UN38.3认证。
全过程质量保障机制
构建包含设备、人员、方法的立体化质控体系:检测设备每季度进行NIST溯源校准,压力源不确定度控制在0.1级;操作人员需取得ASNT三级认证并完成年度盲样考核;数据分析采用蒙特卡洛法评估测量不确定度,典型项目如国家管网集团西气东输三线工程,通过建立包含7个维度21项指标的评价矩阵,使管道试压合格率从92.4%提升至99.6%。
## 技术发展前瞻与建议 未来需重点关注智能化检测系统开发,推动数字孪生技术与压力检测深度融合。建议行业协会牵头建立跨行业压力失效数据库,完善极端工况模拟标准体系。同时加强复合型人才培养,培育既懂检测技术又熟悉行业特性的专业队伍。随着6G通信技术商用,可探索建立基于边缘计算的分布式压力监测网络,实现重大装备的实时安全预警,为工业4.0时代提供可靠的技术保障。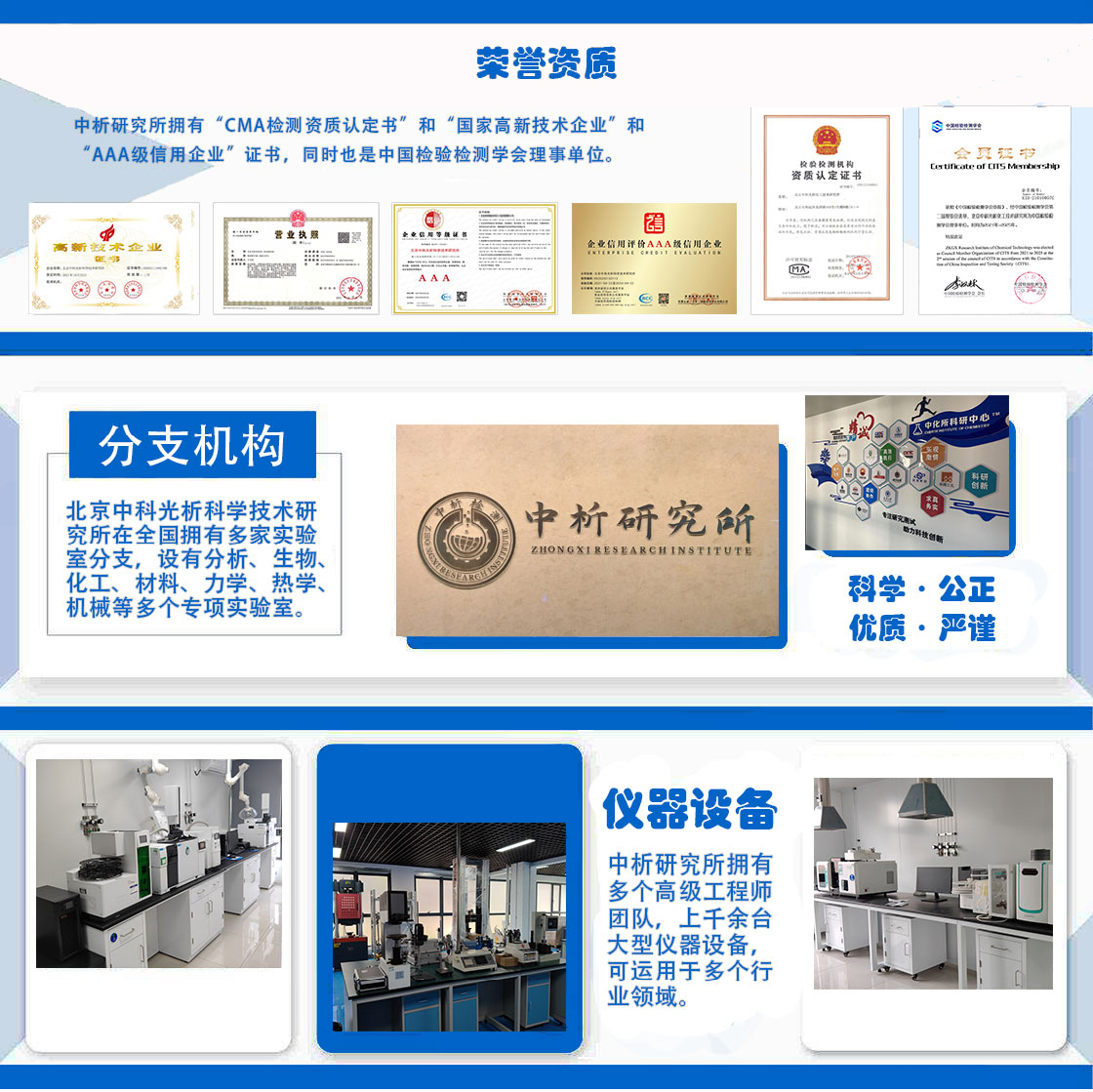
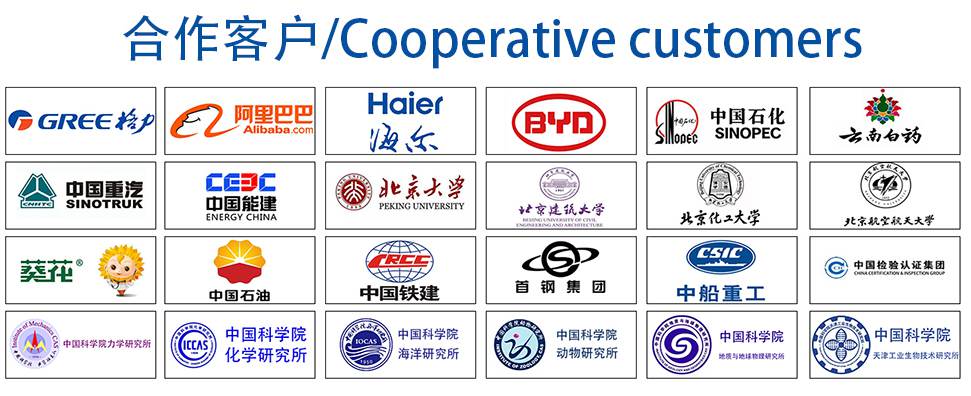