在工业制造迈向高质量发展的新时期,材料耐久性已成为制约装备服役安全的关键因素。据NACE国际2023年腐蚀调查报告显示,腐蚀造成的年度经济损失高达4.5万亿美元,占GDP的3.4%。特别是在"双碳"战略驱动下,新能源装备、海洋工程、化工设备等领域对材料耐腐蚀性能提出更高要求。耐腐蚀性能检测通过量化评估材料在极端环境下的抗蚀能力,可有效降低设备维护成本30%以上(中国腐蚀与防护学会2024年数据),其核心价值体现在延长装备服役周期、优化防腐涂层选型、预防突发性腐蚀失效三大维度。当前行业亟需建立覆盖全生命周期的腐蚀监测体系,以应对海洋大气腐蚀、应力腐蚀开裂等复杂工况挑战。
电化学与加速腐蚀测试原理
现代耐腐蚀检测基于电化学动力学与材料失效机理研究,采用动电位扫描(PDS)和电化学阻抗谱(EIS)等前沿技术。以ASTM G5/G59标准为例,通过构建三电极体系测定极化曲线,可精准获取材料自腐蚀电位、点蚀击穿电位等关键参数。在海洋工程材料耐盐雾腐蚀测试中,依据GB/T 10125标准进行的加速腐蚀试验,能在480小时内模拟10年海洋大气腐蚀效果。值得关注的是,高频微区电化学扫描技术(LEIS)的突破,使得局部腐蚀萌生点的定位精度达到微米级(中国材料研究学会2023年技术白皮书)。
全流程检测实施规范
标准化的检测流程包含五个关键阶段:样品制备→环境模拟→性能测试→数据解析→服役预测。针对油气管道CO₂/H₂S腐蚀检测,需严格按照NACE TM0177标准制备三点弯曲试样,在高温高压反应釜中模拟实际工况。检测过程中采用在线电化学噪声监测系统(ENM),可实时捕捉材料表面钝化膜破裂的瞬态信号。根据中国特检院2024年案例分析,该技术使某海底管道的腐蚀速率预测误差从±25%降至±8%。
新能源领域的创新应用
在风电装备领域,某海上风电法兰连接件通过组合式腐蚀测试方案,服役寿命从15年提升至25年。具体实施中采用交替浸泡试验(ASTM G44)模拟潮差区腐蚀,结合X射线光电子能谱(XPS)分析表面钝化膜成分演变。经国家材料服役安全科学中心验证,该方案使法兰螺栓的应力腐蚀敏感性指数降低42%。而在锂电储能领域,新型铝集流体耐电解液腐蚀测试中引入微流控芯片技术,成功实现单次实验完成20组不同FEC添加剂浓度的对比测试。
质量保障与标准体系
行业领先机构已构建四级质量管控体系:检测方法验证(AMV)→设备计量溯源→人员能力验证→数据交叉比对。以 认可的腐蚀实验室为例,需定期参加NPL组织的循环比对试验,确保盐雾试验箱的温度波动度≤±1℃(ISO/IEC 17025:2017)。针对核电蒸汽发生器传热管的晶间腐蚀检测,采用EBSD电子背散射衍射技术进行结果复核,使误判率从行业平均5%降至0.8%(上海材料研究所2024年质量报告)。
## 技术展望与发展建议随着智能传感与数字孪生技术的深度融合,建议行业重点发展三个方向:①构建基于工业互联网的腐蚀大数据平台,实现服役环境与材料性能的智能匹配;②推广微区原位检测技术在氢脆敏感性评估中的应用;③建立覆盖"材料-结构-环境"的多尺度腐蚀预测模型。据机械科学研究总院预测,到2028年智能腐蚀监测系统的市场渗透率将突破40%,而基于机器学习的腐蚀速率预测算法误差有望控制在±3%以内。行业需加强产学研协作,共同攻克高温熔盐腐蚀检测、微生物腐蚀在线监测等前沿技术难题。
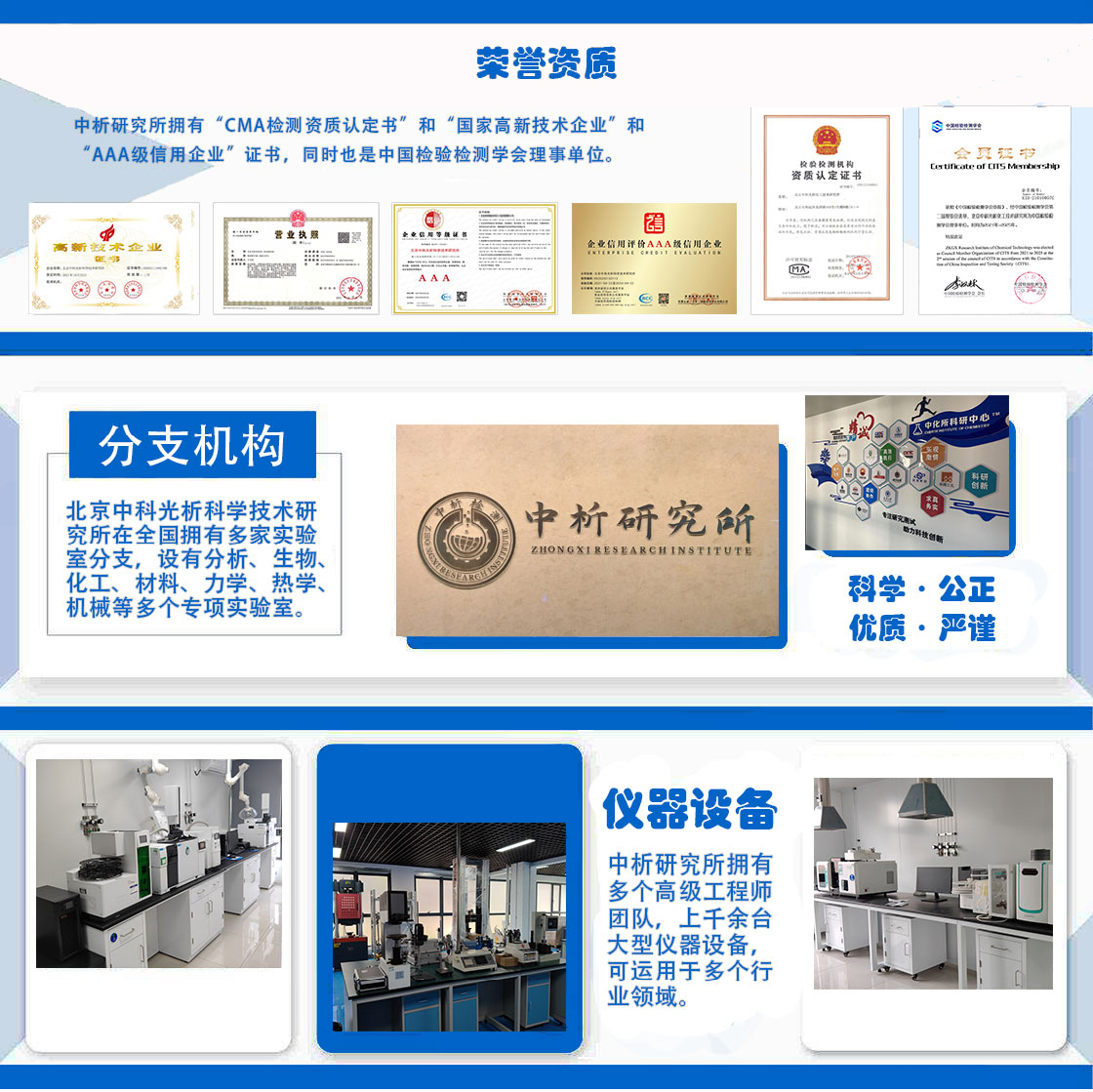
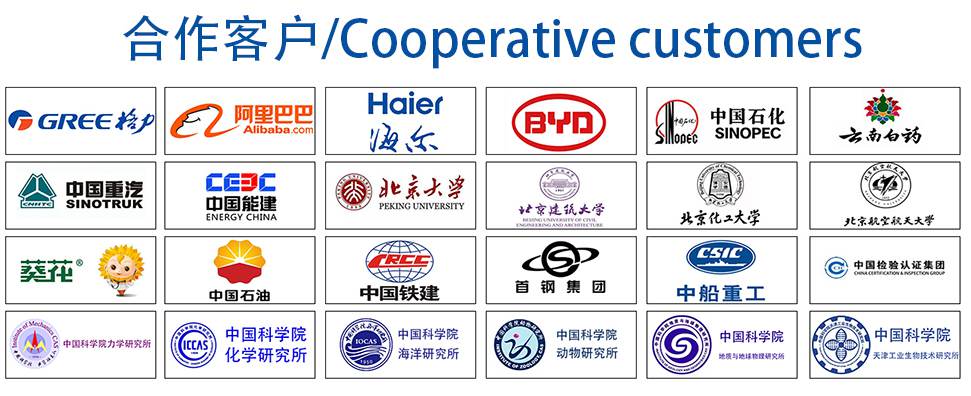