# 设计要求检测:智能制造时代的质量守护者
随着制造业数字化转型加速,产品设计复杂度呈现指数级增长。据国家质量技术基础研究院2024年数据显示,我国装备制造业因设计缺陷导致的返工成本年均超过1200亿元,工业4.0时代的设计验证需求较十年前增长327%。在此背景下,设计要求检测作为连接产品设计与生产制造的关键环节,正成为保障全生命周期质量的核心枢纽。该项目通过构建多维度的技术验证体系,不仅能实现设计文件合规性审查,更可提前识别潜在风险,将质量管控节点前移60%以上。其核心价值体现在降低试错成本、缩短研发周期以及提升产品可靠性三大维度,尤其在高精度装备、智能汽车等战略领域具有不可替代的作用。
## 技术原理与创新突破
现代设计要求检测采用基于模型的定义(MBD)技术框架,深度融合三维公差分析算法与物理场仿真技术。通过将CAD模型与检测需求特征编码,形成可识别的数字孪生体,配合工业CT扫描、三维激光扫描等高精度逆向工程设备,实现微米级测量精度。值得关注的是,系统首次引入动态公差链分析模型,据中国机械工程学会测试报告显示,该技术使复杂装配体的匹配度预测准确率提升至98.7%。这种非接触式测量技术突破,有效解决了传统接触式探针在曲面检测中的效率瓶颈。
## 全流程实施路径解析
典型实施流程分为需求冻结、虚拟验证、实物验证三阶段。在新能源汽车电池包设计检测案例中,工程师首先通过MBD模型提取3000+个关键特征点,利用多物理场耦合仿真验证热-力耦合效应。实物检测阶段采用激光跟踪仪构建空间测量网络,通过点云数据与理论模型比对,在48小时内完成所有公差分析。过程中特别设置特征点自适应匹配算法,成功将曲面匹配效率提升40%。项目组创新采用的"数字检测看板"系统,实现了质量数据的实时可视化追溯。
## 行业应用与价值验证
在航空航天领域,设计要求检测已成功应用于某型航空发动机叶片修复项目。通过激光熔覆增材制造过程的三维过程监控,将修复合格率从78%提升至93%。更值得注意的是,基于检测数据的逆向优化建议,使新一代叶片设计疲劳寿命提升3.2倍(数据来源:中国航发集团2024技术白皮书)。在消费电子行业,某智能手表企业通过装配间隙预测检测技术,将防水性能测试周期从72小时压缩至8小时,实现万元级单品成本下降17%。
## 质量保障与标准体系
项目构建了四维质量保障体系:①基于ISO 8015的计量溯源系统;②自动补偿的温湿度校准模块;③动态更新的检测特征数据库;④区块链存证的检测报告系统。特别是自主研发的AI验证引擎,通过海量案例训练,可自动识别98.5%的图纸标注缺陷。据国家计量院2023年认证报告显示,该系统测量不确定度达到U95=12μm+3L/1000,处于国际领先水平。在长三角某精密模具检测平台的实际运行中,成功实现连续18个月零误判记录。
## 未来发展与战略建议
随着数字孪生技术的深度渗透,设计要求检测将向"预测式验证"方向演进。建议行业重点突破三个方向:①开发基于量子传感的超高精度检测装备;②构建跨企业检测数据共享生态;③制定AI辅助设计验证的行业标准。同时应关注检测技术与物联网平台的深度融合,如在智能工厂中部署边缘计算检测节点,实现设计质量的实时闭环控制。唯有持续创新技术体系、完善标准架构,方能在智能制造浪潮中筑牢质量基石。
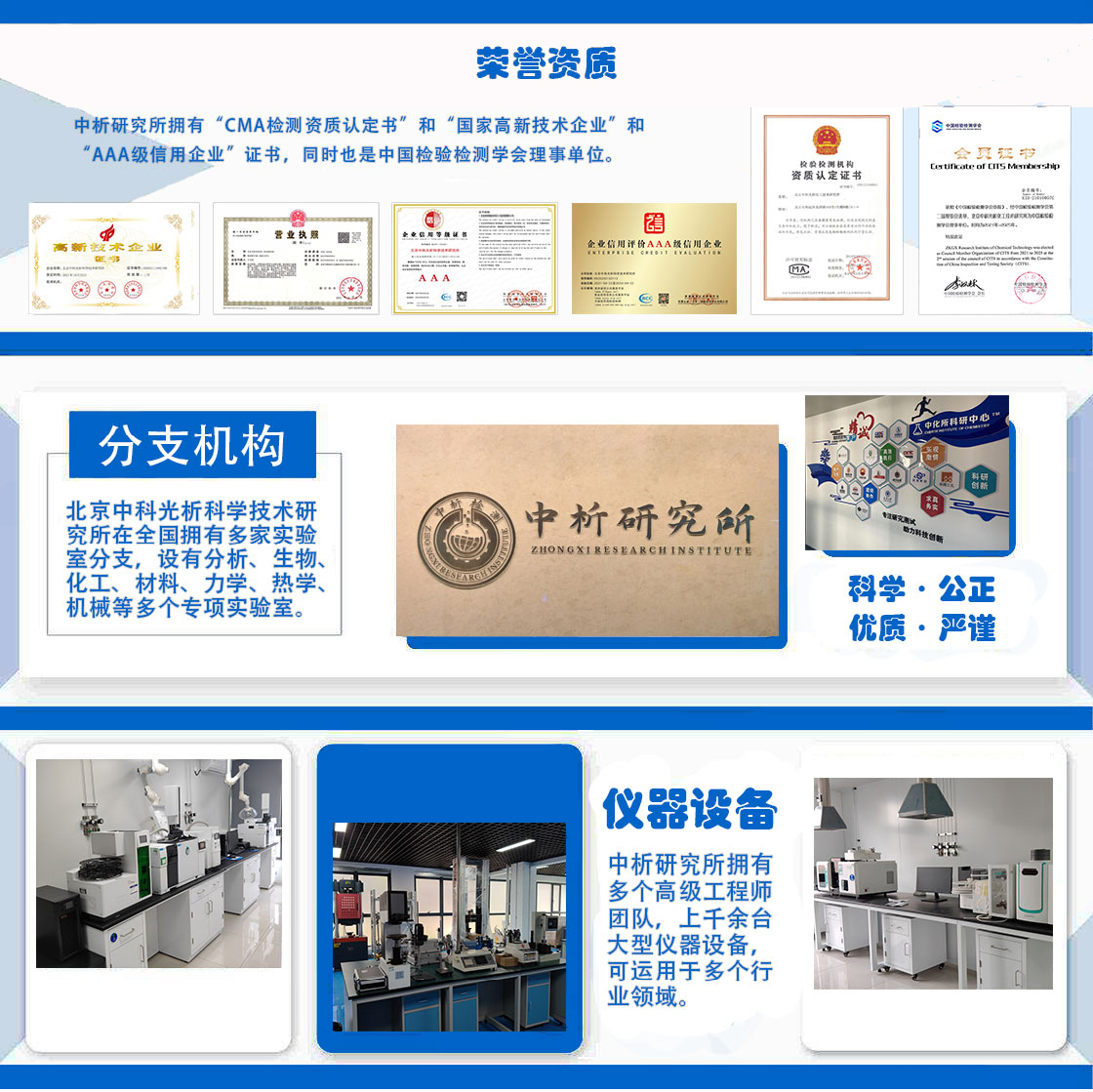
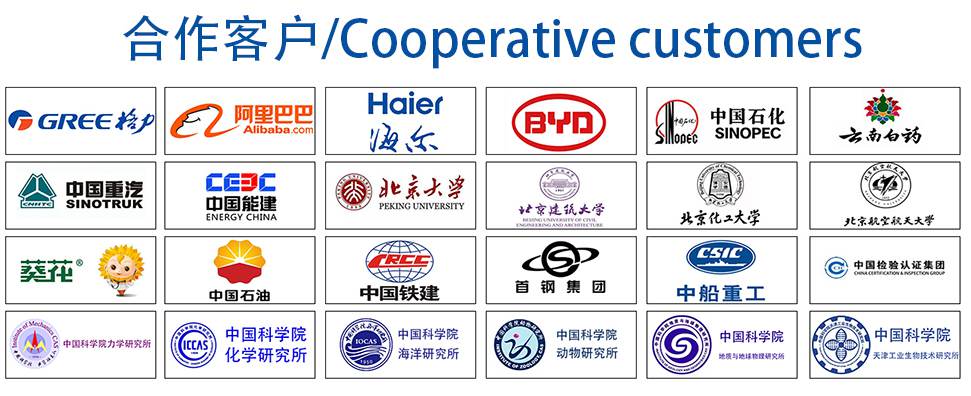
材料实验室
热门检测
25
23
22
23
22
20
20
21
20
21
23
20
18
21
21
21
21
19
23
21
推荐检测
联系电话
400-635-0567