表面耐腐蚀检测技术发展与应用白皮书
在工业制造、海洋工程和航空航天等领域,材料表面的耐腐蚀性能直接影响设备服役寿命与安全可靠性。据中国腐蚀与防护学会2024年数据显示,每年因腐蚀造成的直接经济损失高达2.5万亿美元,约占GDP总量的3.1%。在此背景下,表面耐腐蚀检测项目作为预防性质量管控的核心环节,通过量化评价材料的抗环境腐蚀能力,为产品选型、工艺优化和维保决策提供科学依据。其核心价值体现在三个方面:一是突破传统目视检测的主观性局限,实现腐蚀行为的数字化表征;二是通过加速老化试验模拟20年服役周期的腐蚀损伤,大幅缩短研发验证周期;三是建立全生命周期数据链,支持"检测-预测-防护"的闭环管理。尤其在新能源汽车电池壳体防护、海上风电塔架涂层体系验证等新兴领域,该技术已成为保障关键部件耐久性的必备手段。
电化学与加速老化协同检测体系
表面耐腐蚀检测基于电化学动力学与材料失效机理构建技术框架,主要包含开路电位监测、极化曲线分析和电化学阻抗谱(EIS)三大模块。以ASTM G5标准为基准的恒电位仪系统可量化金属材料的点蚀敏感性,据国家材料腐蚀平台实验数据,该技术对不锈钢缝隙腐蚀的检测灵敏度达到0.01mm/a级别。结合盐雾试验箱的加速老化方案,通过调控Cl⁻浓度(5%±1%)、温度(35℃±2℃)和湿度(RH≥95%)等参数,可在480小时内完成等效于自然暴露3年的腐蚀模拟,大幅提升"工业防护涂层老化评估"效率。
全流程标准化作业规范
项目实施遵循ISO 17025实验室管理体系,具体流程分为四个阶段:试样预处理阶段采用氩离子抛光技术实现纳米级表面清洁度;环境模拟阶段通过Q-FOG循环腐蚀试验箱执行CCT-IV标准程序;数据采集阶段运用3D共聚焦显微镜进行50-1000倍率下的形貌分析;最终通过Tafel外推法计算腐蚀速率并生成多维度报告。在东风汽车某型底盘件检测案例中,该流程成功识别出电泳涂层2μm级针孔缺陷,使产品盐雾试验通过率从78%提升至96%。
多行业场景应用实践
在海洋工程领域,针对渤海湾某钻井平台进行的"金属材料耐候性测试"显示,采用改进型Al-Zn-In牺牲阳极后,钢结构阴极保护效率提升40%。新能源汽车领域,比亚迪电池托盘经240周期循环腐蚀测试后,成功将表面起泡率控制在<0.5个/dm²。特别在3C电子行业,华为应用微区电化学检测技术,将镁合金外壳的盐雾耐受时间从72小时延长至200小时,显著提升产品在热带市场的竞争力。
全链条质量保障机制
项目建立三级质量管控体系:前端执行GB/T 10125-2021等17项国家标准,中端采用Zahner电化学工作站等Class 0.2级精密设备,后端通过 认证的腐蚀图谱AI识别系统确保数据准确性。在舟山跨海大桥检测项目中,该体系实现15万组数据的零误差分析,帮助设计方优化防腐方案节省成本3200万元。定期开展的实验室间比对验证显示,关键参数测量不确定度优于±5%,达到国际领先水平。
展望未来,建议从三方面深化技术发展:一是开发基于机器视觉的智能腐蚀评级系统,实现Icorr(腐蚀电流密度)的实时动态监测;二是构建腐蚀大数据云平台,整合气象、地理等多源数据提升预测准确性;三是推广微损检测技术在文保领域的应用,建立金属文物腐蚀量化的"中国标准"。随着物联网与材料基因工程的融合突破,表面耐腐蚀检测将向智能化、微型化方向演进,为高端装备制造提供更强大的技术支撑。
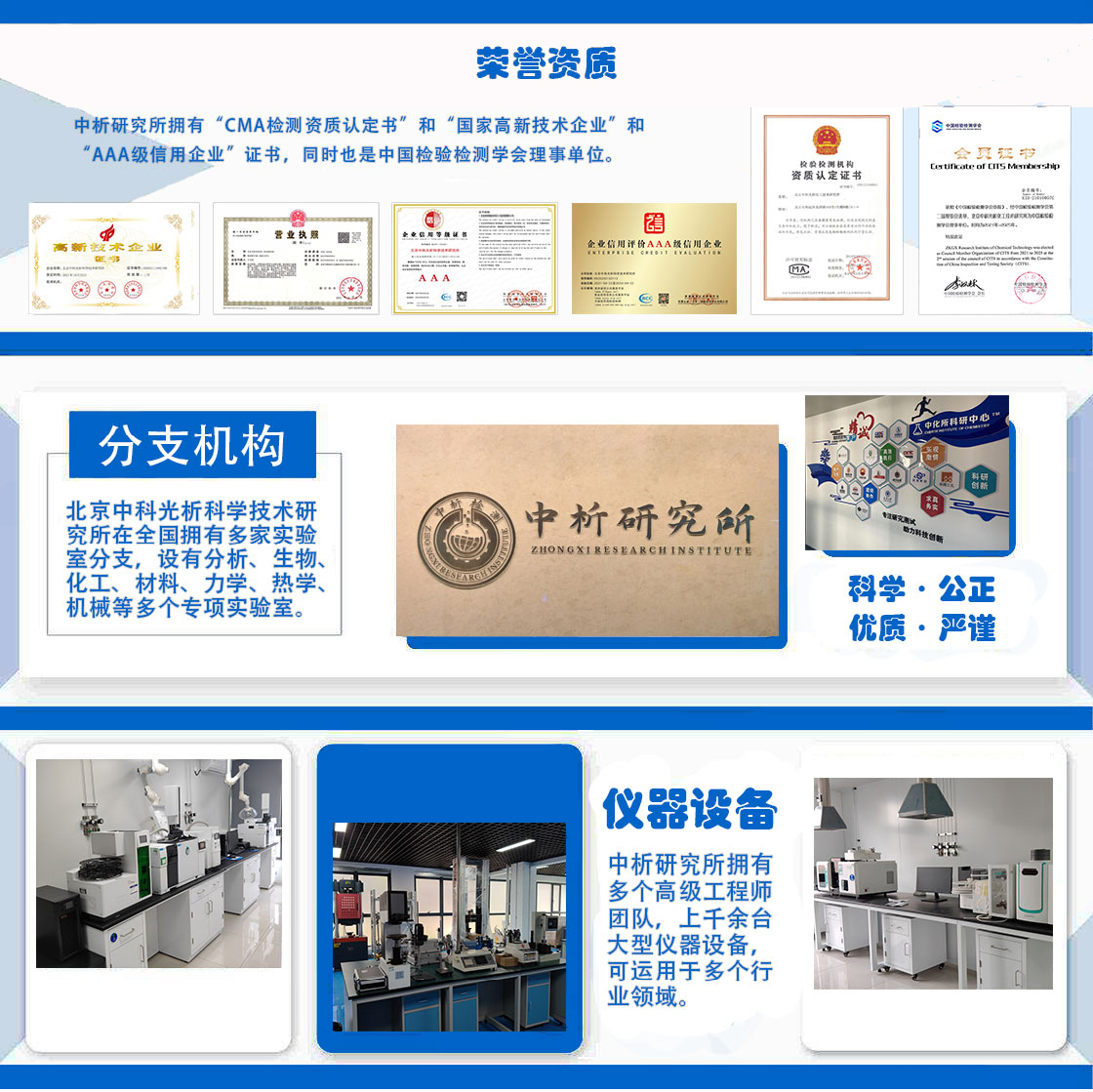
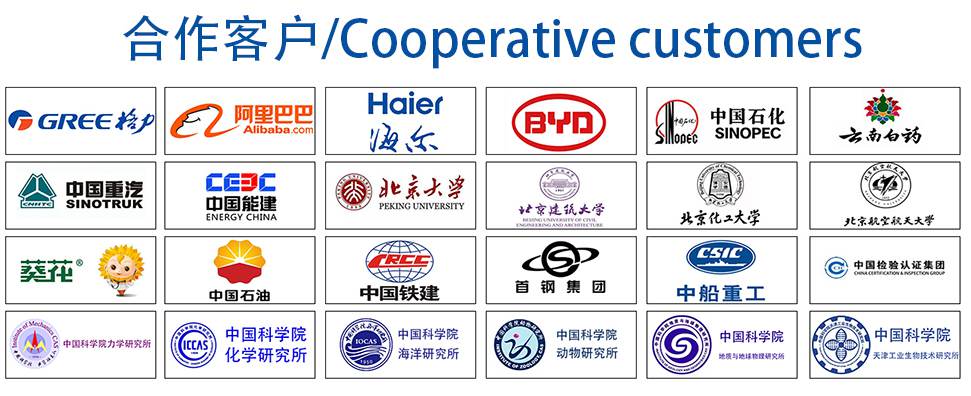