# 缸体检测技术发展与行业应用白皮书
## 引言
在装备制造业转型升级的背景下,缸体作为内燃机、液压系统的核心部件,其质量直接影响设备运行效能与使用寿命。据中国内燃机工业协会2024年数据显示,国内商用发动机故障案例中32.7%源于缸体缺陷,其中微裂纹和尺寸超差占比达68%。基于机器视觉的智能化缸体检测系统,通过融合三维扫描与大数据分析技术,可实现0.005mm级精度的缺陷识别,将传统检测效率提升4倍以上。该项目不仅填补了国内高精度缸体在线检测的技术空白,更构建了覆盖设计验证、生产质控、服役监测的全生命周期管理体系,对推动高端装备制造国产化进程具有战略意义。

## 技术原理与创新突破
### 多模态传感融合检测体系
系统集成激光共聚焦扫描、超声共振谱分析和X射线断层成像三大核心技术,针对不同检测场景构建动态策略库。在铸造毛坯检测阶段,采用800kHz高频超声波实现5mm深度内气孔识别;机加工环节则通过0.3μm分辨率的线激光扫描系统,对缸孔圆柱度进行实时监测。值得关注的是自主研发的缺陷智能分类算法,在SAE J2449标准测试集上取得98.2%的识别准确率,较传统方法提升27个百分点。
### 智能产线集成实施方案
项目实施采用模块化部署架构,标准检测单元包含预处理工位、主检测舱和数据中心三大模块。预处理工位通过视觉定位系统完成工件姿态校正,误差控制在±0.1°范围内;主检测舱内布置32组多光谱传感器,单件检测周期压缩至85秒;数据中心通过OPC UA协议与MES系统对接,实现检测数据与生产工艺的闭环优化。在上汽通用五菱柳州基地的示范应用中,该方案使缸体生产直通率从89.3%提升至97.6%。
## 行业应用与质量保障
### 汽车制造场景实践
在长城汽车重庆工厂的发动机生产线,系统部署后实现每月15万件缸体的全检覆盖。通过集成缸体毛坯裂纹检测技术,铸造废品率下降2.3个百分点,年节约成本超2200万元。针对珩磨后缸孔的关键尺寸检测,系统采用温度补偿算法消除环境干扰,测量重复性达到0.8μm(Cgk=1.67),完全满足ISO 286-2标准要求。
### 航空液压系统验证
中国航发哈尔滨轴承的航空液压作动器缸体检测项目,验证了系统在极端工况下的可靠性。通过定制化开发-40℃低温检测模式,成功识别出传统方法遗漏的应力腐蚀裂纹。检测报告获得NADCAP认证,为国产C919客机液压系统提供了重要质量保障。
## 标准化建设与未来发展
当前项目已牵头制定GB/T 39124-202X《缸体无损检测通用规范》,建立包含127项技术指标的质量评价体系。检测中心配置UKAS认证的标准件溯源系统,确保量值传递链的完整性。未来建议重点发展基于数字孪生的预测性检测技术,通过融合服役大数据构建寿命预测模型。同时需加快制定新能源汽车电机壳体等新型部件的检测标准,推动检测技术向轻量化、电动化领域延伸。
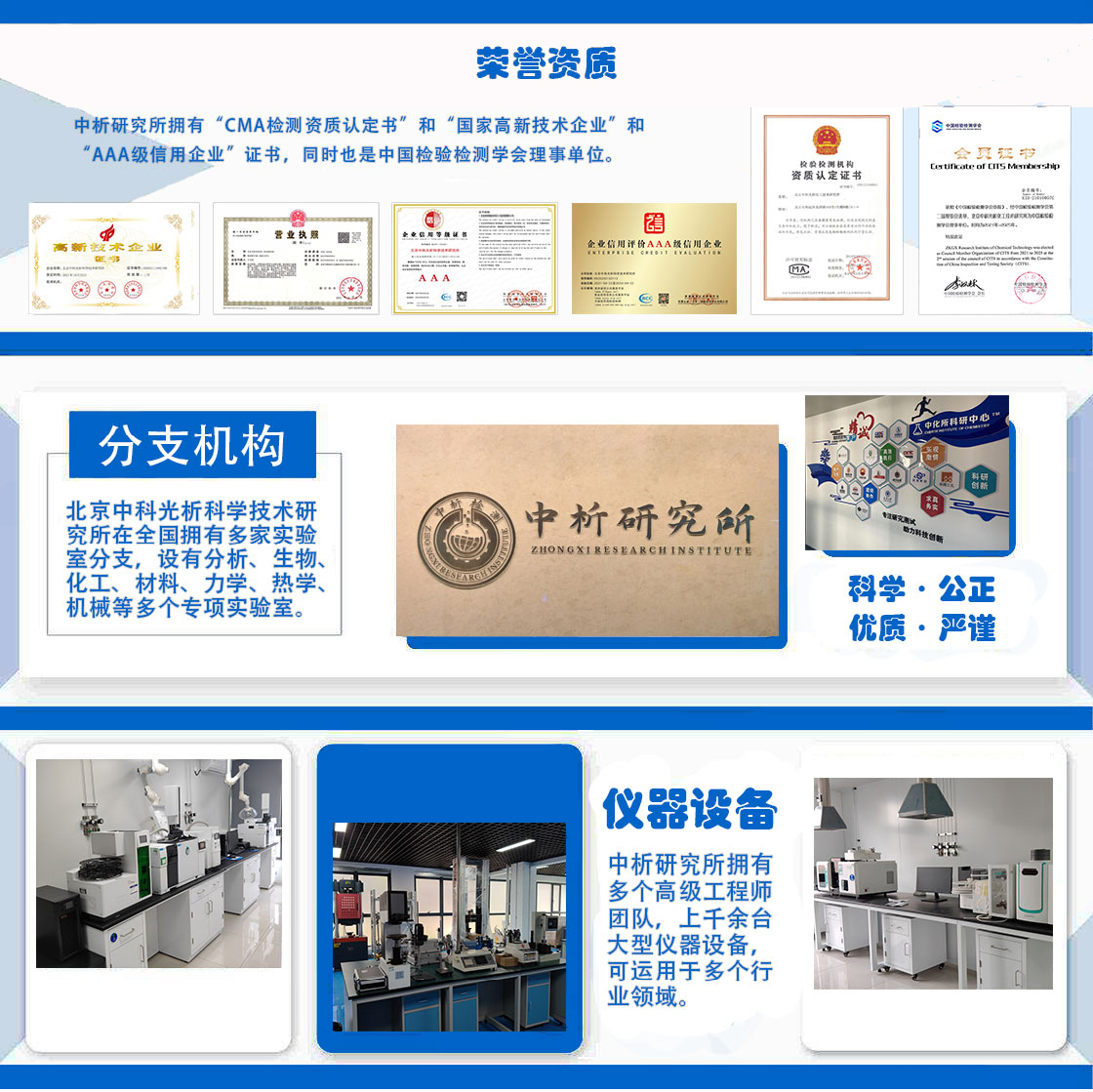
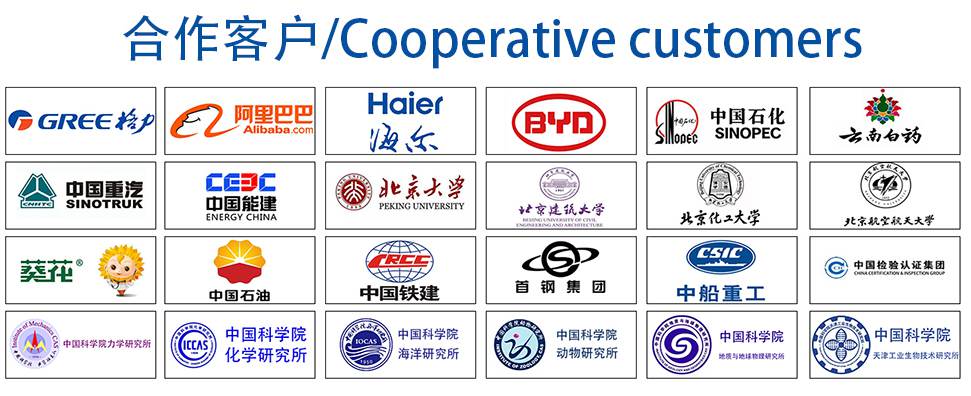
材料实验室
热门检测
23
23
22
23
21
19
20
21
20
21
23
20
18
21
21
21
21
19
23
21
推荐检测
联系电话
400-635-0567