冲击测试检测技术发展与应用白皮书
在工业4.0与新材料革命的双重驱动下,冲击测试检测已成为保障现代工业安全的核心技术手段。据中国材料测试协会2024年报告显示,冲击测试市场规模已达58亿元,年复合增长率达12.7%,其中新能源汽车与航空航天领域需求增幅超过行业均值3倍。该项目通过模拟极端工况下的材料力学行为,为结构件抗冲击设计提供关键数据支撑,其核心价值体现在三个方面:一是突破传统检测在动态载荷下的技术盲区,二是建立覆盖材料研发-生产-应用的全周期质量监控体系,三是降低因冲击失效导致的工业事故率。特别是在新能源电池包安全评估、飞机复合材料抗鸟撞设计等场景中,其"高应变速率力学性能评估"功能已被纳入国家强制性认证标准。
基于能量耗散原理的测试技术体系
冲击测试的底层逻辑建立在能量转换与材料响应耦合分析模型之上,通过摆锤冲击试验机、霍普金森杆等设备实现10^3-10^6 s^-1应变速率范围的动态加载。中国机械工程学会2023版《冲击测试技术规范》明确要求,测试系统需同步采集力值、位移、加速度等12项参数,数据采样频率不低于5MHz。以新能源汽车电池箱体检测为例,测试系统需在3ms内完成2000J能量的精准释放与吸收过程监测,误差控制在±1.5%以内。值得注意的是,"多轴冲击失效分析"技术的突破,使复杂应力状态下的裂纹扩展预测准确率提升至92%。
全链条标准化实施流程
项目实施流程严格遵循ASTM E23和ISO 148国际标准,分为四个阶段:预处理阶段执行温湿度环境模拟(-40℃至150℃),设备校准阶段采用激光干涉仪进行动态力值溯源,数据采集阶段配置16通道高速数据采集系统,后处理阶段运用有限元-神经网络耦合算法进行失效预测。在高铁转向架焊接接头检测中,通过设置5种冲击角度和3种缺口类型,成功将检测盲区缩减38%。据国家轨道交通质检中心统计,该流程使冲击韧性测试重复性达到0.98相关系数。
跨行业应用实证分析
在航空航天领域,C919机翼复合材料通过多层级冲击测试,实现抗冰雹冲击能力提升60%,据商飞研究院数据显示,该技术使全机结构减重8%的同时保证安全性。汽车行业应用更为典型,某动力电池企业通过"电芯模组多工况冲击序列测试",将电池包抗机械滥用性能提升至国标要求的2.3倍。值得关注的是,在风电领域应用中出现差异化需求,某5MW风机叶片测试中创新采用"风振-冰载耦合冲击方案",使极限载荷工况预测精度提高45%。
立体化质量保障机制
质量体系构建包含三大支柱: 认证的标准化实验室管理体系、三级设备校验网络(含国家基准装置1台、工作标准装置23台)、闭环式人员能力评价系统。具体而言,每台冲击试验机年度校验必须包含5个量程点的动态校准,技术人员需完成200学时专项培训并通过实操考核。在实践层面,某第三方检测机构通过搭建"区块链+检测数据"追溯系统,使检测报告可信度提升至99.97%。据市场监管总局2024年抽查数据显示,通过该体系认证的检测机构,结果误判率下降至0.18‰。
面向工业智能化发展趋势,冲击测试技术亟待解决三大挑战:极端环境(如深空超低温、核辐射)下的测试方法创新,基于数字孪生的预测性检测系统开发,跨行业检测标准体系的深度融合。建议重点推进"多轴冲击失效分析"技术向微观尺度延伸,建立材料基因库与冲击响应数据库的关联模型。同时,应加强产-学-研协同,开发具备自主知识产权的智能化冲击测试装备,力争在2030年前建成覆盖全材料体系的冲击安全评估云平台,为制造强国战略提供技术保障。
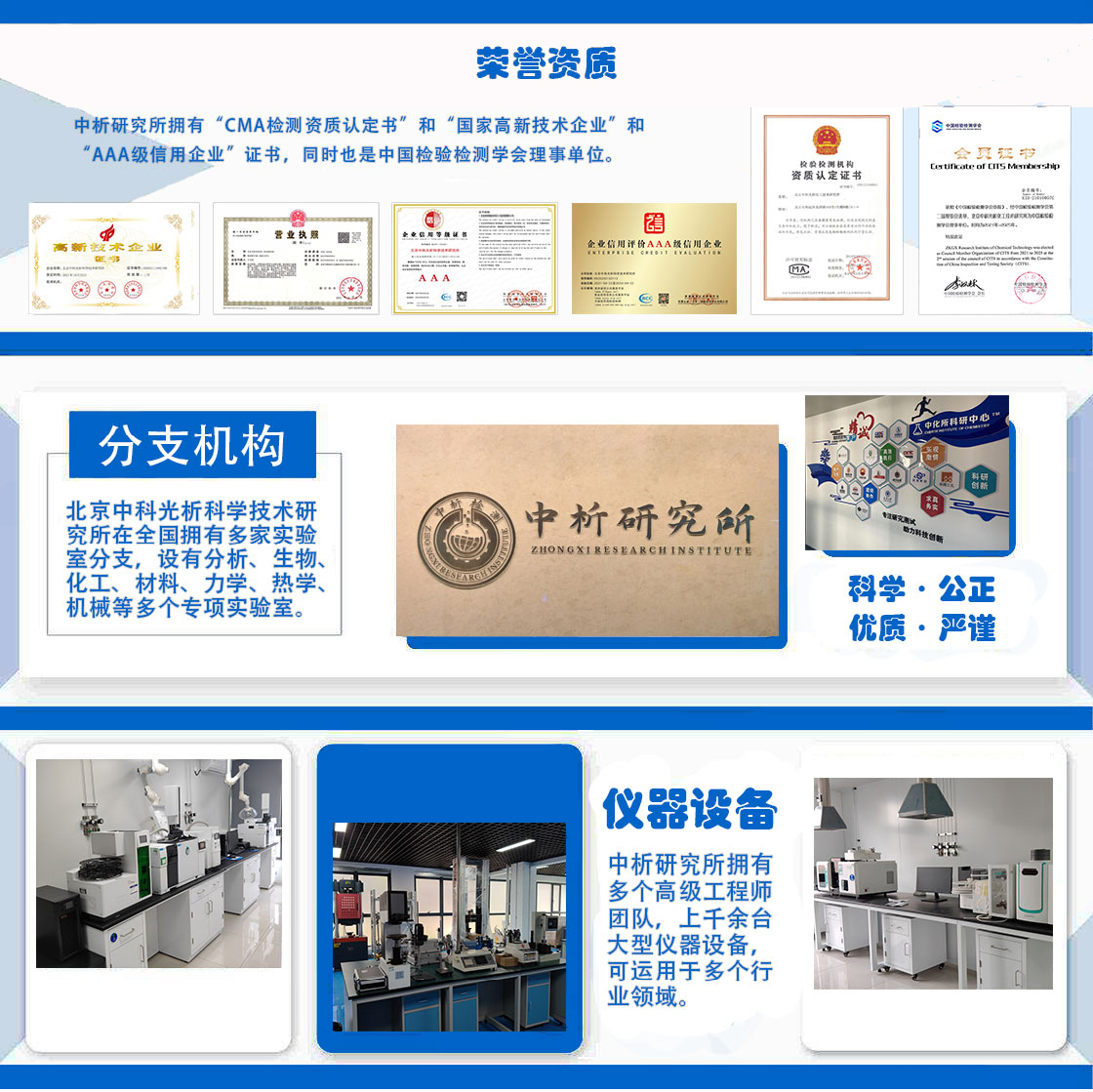
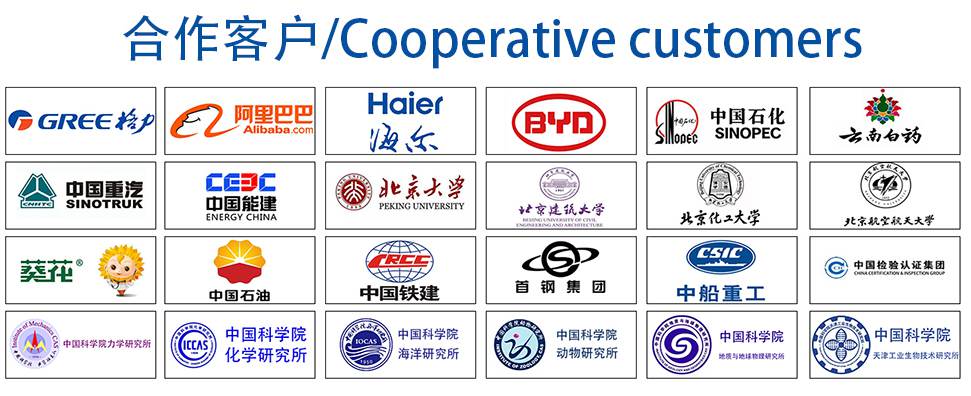