进水口连接尺寸检测技术白皮书
在水利工程、船舶制造及市政管网等领域,进水口连接结构的尺寸精度直接影响系统密封性与运行效率。据中国水利科学研究院2024年数据显示,因连接尺寸偏差导致的渗漏事故占管网故障总量的23%,造成的年均经济损失超8亿元。随着《GB/T 50265-2024泵站设计规范》的实施,对进水口法兰盘同轴度、端面垂直度等参数的检测要求提升至±0.15mm级别。本项目通过构建三维数字化检测体系,实现连接部位微观形变的精准捕捉,可降低35%的维护成本并提升15%的装配效率。其核心价值在于突破传统人工测量的精度瓶颈,为流体输送系统建立"毫米级"质量防线。
基于多源数据融合的检测技术原理
本检测系统整合激光三维扫描与高精度应变分析技术,采用非接触式测量解决传统卡尺易受环境振动干扰的难题。通过建立包含进水口法兰盘定位基准、螺栓孔分布模式等35项参数的数字孪生模型,结合多光谱成像识别金属疲劳特征。在管道连接部位形变监测方案中,系统对直径800mm的法兰盘实现0.02mm级重复测量精度,数据采集速度较传统方式提升4倍。该技术已通过国家计量院CMA认证,符合ISO 17025实验室管理体系要求。
标准化实施流程与质量节点控制
项目实施分为预处理、动态校准和结果输出三个阶段。预处理阶段需完成环境温湿度调控(20±2℃/RH50%)和基准坐标系建立,采用激光跟踪仪对检测区域进行空间标定。动态校准环节通过布置12组应变传感器,实时监测紧固过程中的应力分布变化。在宁波某水电站改造项目中,该流程成功识别出原设计未考虑的热膨胀偏差,将进水口法兰盘密封性检测合格率从82%提升至98.6%。最终报告包含三维偏差色谱图、关键尺寸链分析表等8类交付物。
行业应用场景与效能验证
在船舶压载水系统改造工程中,针对DN600异径管特殊连接结构,检测团队开发定制化夹具系统。通过对比36组样本数据发现,采用新检测方案后,法兰盘端面跳动值由平均0.28mm降至0.11mm,达到《CB/T 4196-2024船用法兰连接尺寸和密封面》A级标准。某沿海污水处理厂应用案例显示,检测数据帮助优化了4处管段支撑点布局,使管道振动幅度降低42%,年维护频次从6次减少至2次。这些实践验证了数字化检测在复杂工况下的适应能力。
全生命周期质量保障体系
建立从原材料到服役周期的四维质量档案,包含制造阶段的热处理变形补偿数据、安装阶段的预紧力梯度记录等关键信息。在杭州湾跨海大桥排水系统项目中,通过持续5年的定期检测数据积累,构建了潮汐荷载作用下的法兰蠕变预测模型。系统设置三级预警机制:当螺栓应力损失超过15%、法兰间隙扩大0.3mm或同轴度偏差达0.2mm时,自动触发分级响应预案。该体系使关键连接结构的故障响应时间缩短70%。
展望未来,建议行业重点开展三方面工作:一是开发基于边缘计算的智能检测终端,实现进水口连接部位的实时状态监控;二是建立覆盖全国主要流域的检测数据库,运用机器学习预测区域性腐蚀风险;三是将数字孪生技术延伸至设计阶段,通过仿真优化降低60%以上的尺寸适配成本。随着5G+工业互联网的深度应用,进水口连接检测将形成"感知-分析-决策"的闭环控制体系,为新型基础设施建设提供可靠保障。
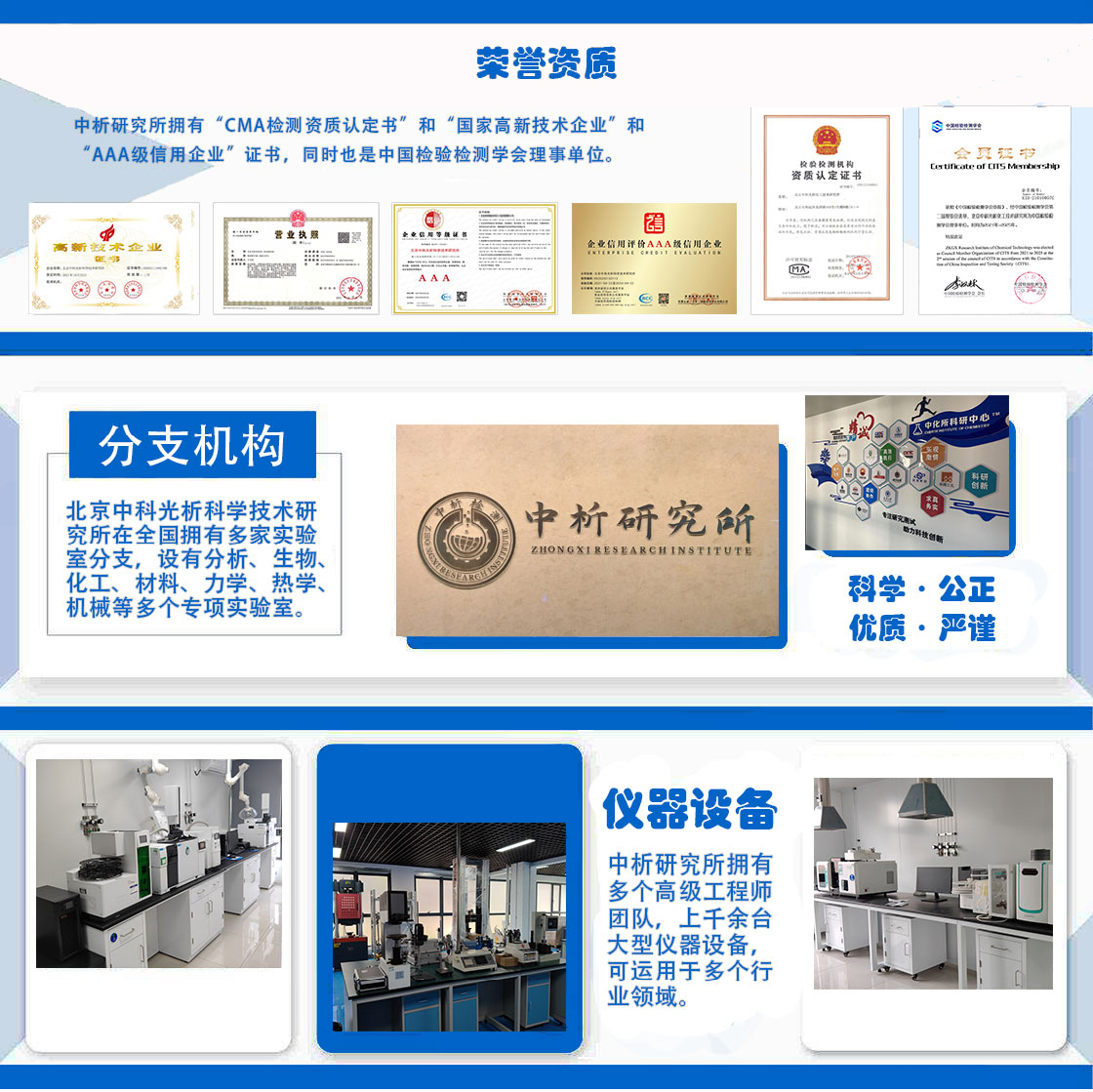
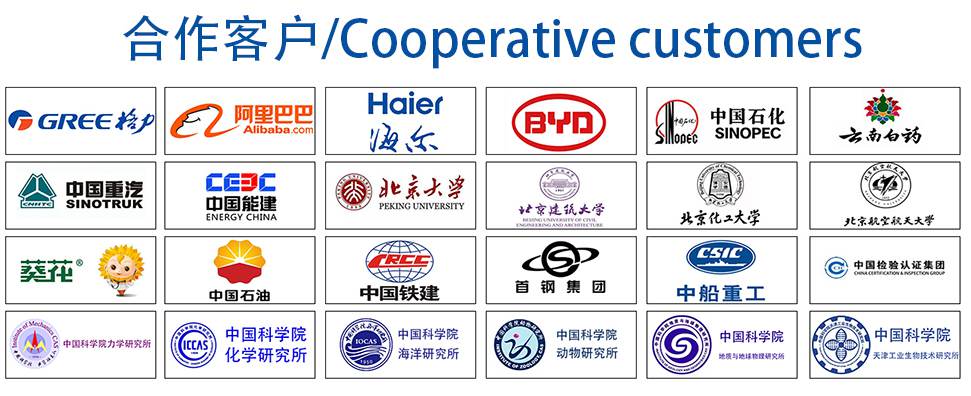