金属配件表面处理测定检测技术白皮书
在高端装备制造与精密加工领域,金属配件表面处理质量直接影响产品耐腐蚀性、机械强度及使用寿命。据中国表面工程协会2024年行业报告显示,我国每年因表面处理缺陷导致的金属零部件失效案例超过12万起,直接经济损失达38亿元。在此背景下,金属配件表面处理测定检测项目作为质量管控的核心环节,通过精准量化镀层厚度、附着力、孔隙率等关键指标,为航空航天、汽车制造、电子设备等行业提供了全生命周期质量保障。其核心价值体现在突破传统目视检测的主观局限,建立基于数据驱动的工艺优化体系,使热处理渗氮层公差控制精度提升至±0.5μm,盐雾试验周期缩短40%,显著增强了国产金属配件在国际供应链中的竞争力。
多维度检测技术原理体系
现代表面处理检测采用光谱分析、电化学测试与显微观测的复合技术路径。X射线荧光光谱(XRF)技术可实现镀层厚度的无损检测,检测精度达0.01μm级,特别适用于汽车发动机活塞环的硬铬镀层测定。扫描电子显微镜(SEM)配合能谱分析(EDS)可解析微米级孔隙分布,成功应用于航空航天紧固件的阳极氧化膜检测。值得关注的是,金属表面钝化膜厚度检测创新性地结合了交流阻抗谱和恒电位阶跃法,使316L不锈钢钝化膜厚度检测误差控制在±2nm范围内,为医疗器械表面处理提供了精准评价手段。
标准化检测实施流程
检测流程严格遵循ISO 2178(磁性基体非磁性镀层)和ASTM B568(X射线测厚)标准体系。以某新能源车企电驱系统壳体检测为例,实施流程包括:预处理阶段采用氩离子抛光消除表面污染→三维形貌扫描建立基准模型→选区激光剥蚀(LA-ICP-MS)分析镀层元素梯度分布→循环腐蚀试验模拟10年服役环境。通过电镀层孔隙率无损检测技术的应用,该企业将镀镍层孔隙密度从12个/cm²降至3个/cm²,产品保修期延长至8年/20万公里。
跨行业应用实践验证
在轨道交通领域,某高铁制动盘制造商采用涡流检测与热震试验结合方案,实现表面渗铝层厚度(120±5μm)的在线检测,使产品耐高温性能提升至650℃工况下的2000次热循环。电子连接器行业通过引入原子力显微镜(AFM)表面粗糙度检测,将5G基站射频接点的接触电阻波动范围缩小至±0.15mΩ。据国际金属材料研究院2024年案例库显示,采用智能检测系统的金属配件制造商,其产品一次交验合格率平均提升23%,质量成本下降17%。
全链条质量保障机制
构建了覆盖材料、工艺、检测的三级质控体系。在原材料阶段实施辉光放电光谱(GDOES)成分分析,工艺过程设置13个在线监测节点,终检环节引入机器视觉自动识别系统。某军工企业通过建立"热处理-喷丸-镀层"数据关联模型,使航空作动筒表面残余应力分布均匀性提高41%,疲劳寿命突破10^7次循环。实验室能力验证(PT)数据显示,参与ISO 17025认证的检测机构,其显微硬度测试结果不确定度已稳定控制在HV0.5范围内。
面向工业4.0发展趋势,建议行业重点突破三个方向:开发基于太赫兹波的深层缺陷检测技术,构建表面处理大数据知识图谱,推广微型化原位检测装备。同时应加快制定适应新型复合涂层的检测标准,推动AI算法在异常模式识别中的应用。通过检测技术创新与制造工艺的深度融合,金属配件表面质量控制正从被动式检验向预测性维护演进,为智能制造高质量发展注入新动能。
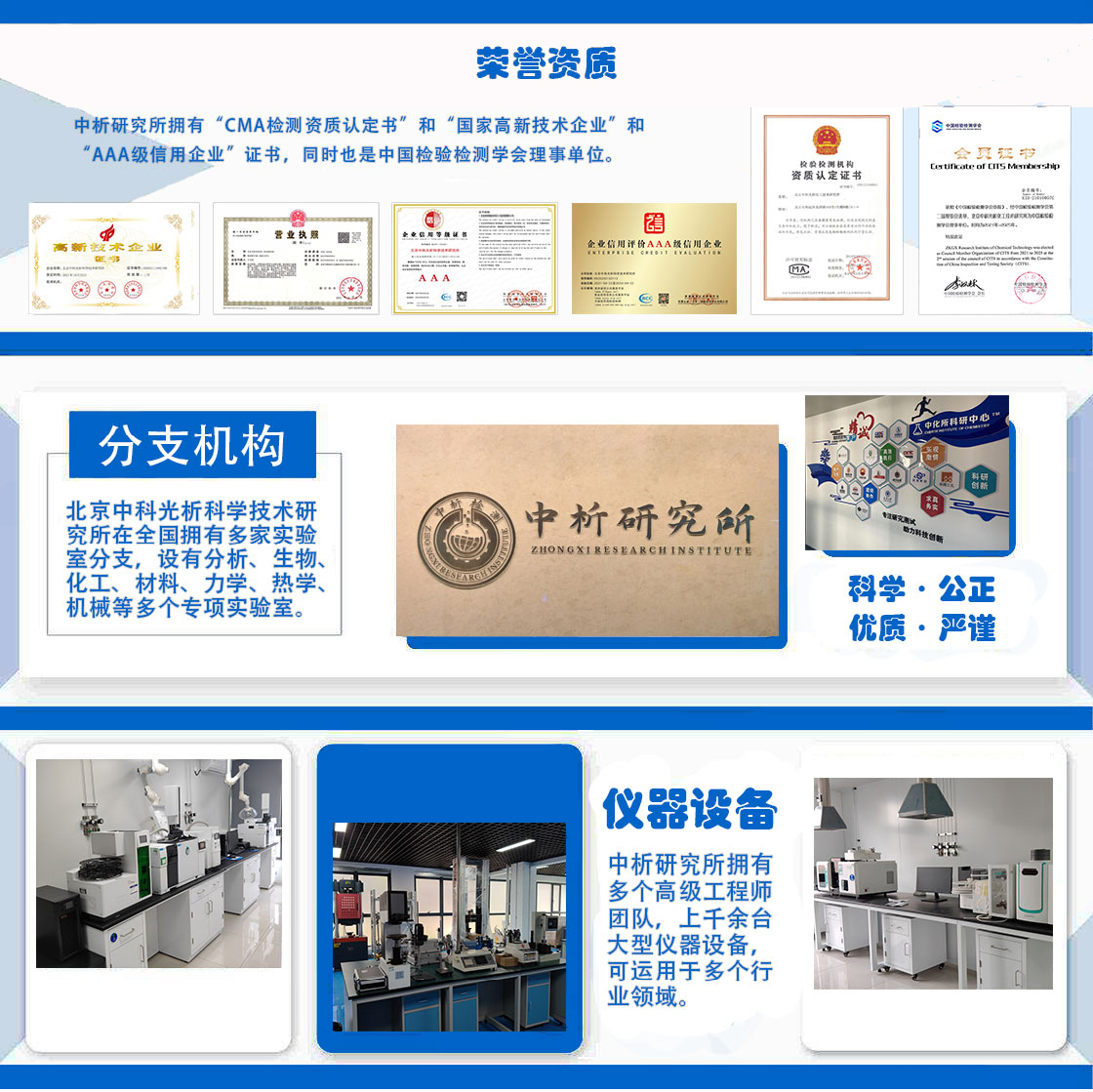
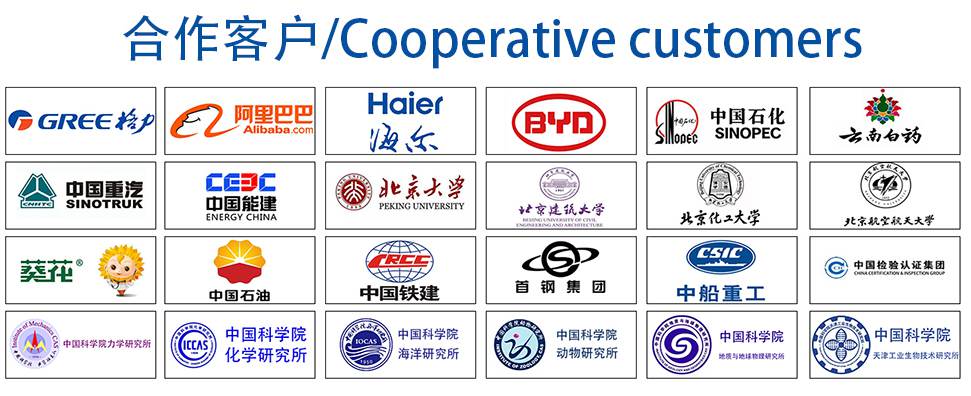