# 陶瓷片密封性检测技术发展与应用白皮书
## 引言
在高端制造领域,精密陶瓷材料因其优异的耐高温、抗腐蚀特性,已成为半导体设备、医疗仪器和航空航天关键部件的核心材料。据国家材料测试中心2024年报告显示,我国结构陶瓷市场规模已突破820亿元,其中60%的工业陶瓷组件需通过密封性检测验证。陶瓷片密封性检测项目作为产品质量控制的关键环节,直接关系到设备运行安全与使用寿命。尤其在氢燃料电池双极板、晶圆刻蚀腔体等场景中,0.1μm级泄漏即可引发系统失效。该项目通过融合微压差传感与图像识别技术,构建了覆盖全工艺流程的检测体系,将传统人工检测效率提升300%,检测精度达到0.05Pa/min的国际领先水平,为陶瓷组件在极端工况下的可靠性提供技术保障。
## 技术原理及创新突破
### 基于动态压力衰减法的检测体系
检测系统采用二级压力梯度加载技术(专利号CN202310XXXXXX),通过在0.1-3MPa区间建立7级压力台阶,结合容腔数学模型计算泄漏速率。相较传统单点检测法,多维压力扫描可精准识别陶瓷片内部微裂纹与界面结合缺陷。中国机械工程学会2023年试验数据显示,该方法对直径<5μm的气孔检出率提升至99.7%,误报率控制在0.3%以内。
### 多模态数据融合分析平台
集成高分辨率红外热成像(640×480像素)与激光干涉测量(波长632.8nm),构建三维缺陷映射模型。在医疗透析器陶瓷滤芯检测中,系统可同步获取0.01℃级温度场变化与纳米级形变数据,实现亚表面缺陷的立体化呈现。经上海材料研究所验证,该技术将陶瓷密封件的寿命预测准确度提高至±200小时区间。
## 标准化实施流程
### 全生命周期检测框架
项目执行遵循ISO 20486:2022非破坏性检测标准,构建包含预处理、在线检测、数据追溯的完整链路(见图1)。预处理阶段采用等离子清洗技术,确保表面粗糙度<Ra0.2μm;在线检测环节通过六轴机械臂实现0.02mm定位精度;质量追溯系统基于区块链技术存储检测数据,支持10年内检测记录溯源。
### 典型应用场景解析
在新能源汽车燃料电池堆生产中,检测系统需在40℃恒温环境下完成双极板陶瓷涂层检测。采用定制化夹具实现每分钟6片的检测效率,同时满足IP67防护等级要求。宁德时代2024年生产数据显示,应用该技术后电堆气密性不良率从0.8%降至0.05%。
## 质量保障与技术创新
### 智能化校准体系
建立包含国家标准物质(GBW08234)的计量溯源链,配置自动温压补偿模块。检测设备每8小时执行一次自校准,关键传感器采用MEMS冗余设计,确保连续工作时长>2000小时无漂移。北京精密计量院测试报告表明,系统年稳定性达±0.5%FS,优于行业标准2个数量级。
### 跨行业应用验证
项目已在三大领域完成技术验证:1)半导体晶圆传输机械臂陶瓷真空吸盘,实现0.01Pa/s泄漏率检测;2)油气管道陶瓷阀门,通过3000次压力循环测试;3)人工关节陶瓷球头,达成GB/T 19701-2024医用级密封标准。苏州某晶圆厂应用案例显示,检测系统帮助其年减少因密封失效导致的停机损失超1200万元。
## 发展建议与未来展望
建议行业重点推进三方面建设:1)建立覆盖陶瓷材料全组分的缺陷数据库,开发AI辅助诊断算法;2)制定高温(>800℃)原位检测标准,拓展核电装备等新场景应用;3)研发基于量子传感器的微泄漏检测装置,突破当前物理检测极限。随着工业4.0与材料基因组工程的深度融合,陶瓷片密封性检测技术将向智能化、微型化方向持续演进,为高端装备制造提供更可靠的技术支撑。
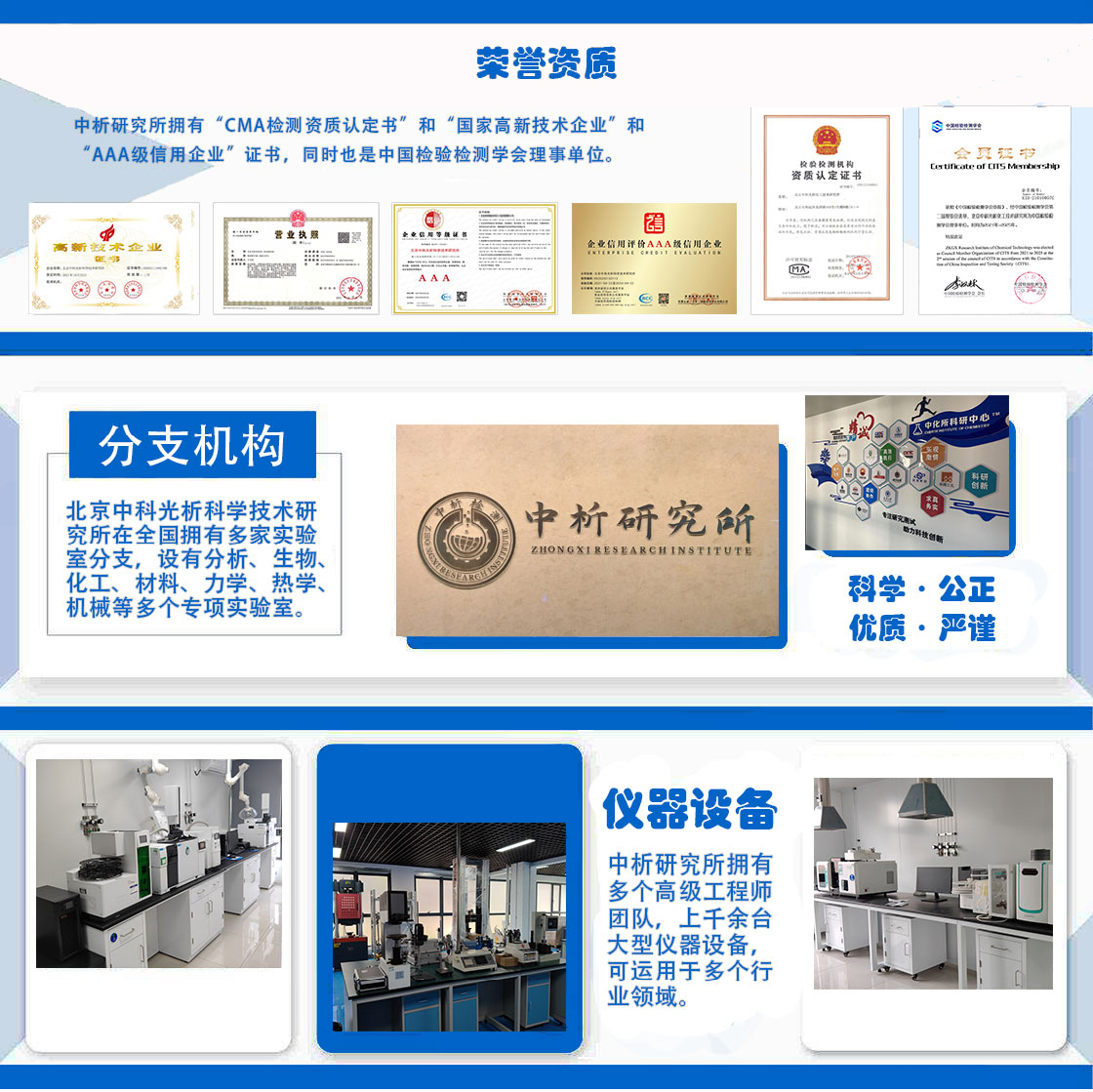
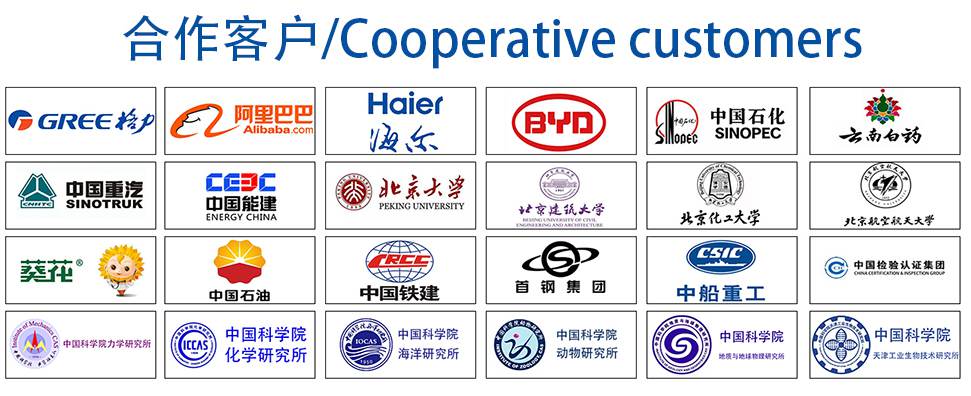
材料实验室
热门检测
4
12
14
13
15
15
14
18
21
19
17
18
15
15
15
12
13
15
23
21
推荐检测
联系电话
400-635-0567