螺纹连接尺寸检测技术白皮书
在高端装备制造领域,螺纹连接作为关键机械传力结构,其尺寸精度直接影响设备整体性能。据中国机械工程学会2023年统计,60%以上的机械失效事故源于螺纹连接副的配合误差,造成年均经济损失超120亿元。在此背景下,螺纹连接尺寸检测项目通过构建数字化检测体系,实现了0.005mm级精度的几何参数测量,为航空航天、新能源装备等战略行业提供了可靠的质量保障。该技术的核心价值在于打通"设计-制造-服役"全流程数据链,显著提升螺纹副承载能力和疲劳寿命,据国家质检总局实验验证,规范化的尺寸检测可使螺纹连接结构可靠性提升42%。
高精度检测技术原理
基于机器视觉与触觉传感的融合检测系统,采用双CCD阵列构建三维空间坐标系。通过纳米级位移传感器进行螺距偏差测量时,系统同步采集升角、牙型半角等12项几何参数,数据采样频率达20kHz。值得关注的是,该系统创新性地引入涡流检测模块,可同步分析螺纹表面硬化层深度。据《精密制造学报》2024年研究成果显示,该复合检测方法较传统三坐标测量效率提升3倍,重复测量精度稳定在±0.002mm区间。
智能化实施流程设计
项目实施采用模块化作业流程:前期通过三维激光扫描建立工件数字孪生模型,智能规划测点分布;中期运用六轴机械臂搭载多传感探头完成自动化测量,单件检测时间压缩至3分钟;后期通过AI算法生成三维偏差色谱图,自动判定是否符合ASME B1.13M标准。在风电齿轮箱螺栓检测场景中,系统成功识别出0.008mm的牙型角偏差,及时规避了潜在的断齿风险。
跨行业应用案例解析
在新能源汽车领域,某电池Pack制造商应用该技术后,模组连接螺栓的扭矩一致性提升37%。具体案例显示,通过"螺纹副接触应力分布优化"技术路径,电池箱体振动工况下的松脱率从1.2‰降至0.05‰。另在航空航天领域,某型号火箭发动机采用"全螺纹服役应力云图"技术后,法兰连接处漏气事故率实现零记录。这些实践验证了检测技术对关键设备性能的提升效果。
全生命周期质量保障
构建包含设备溯源、过程监控、数据分析的三级质控体系:测量设备每日进行ISO/IEC17025标准下的温漂补偿校准;检测数据实时上传区块链平台确保不可篡改;建立包含200万组螺纹失效案例的专家数据库。特别在军工领域,系统实现了检测记录与装备电子履历的自动关联,为后续维修保养提供精准数据支持。
面向工业4.0发展需求,建议从三方面加强技术布局:首先加快亚微米级光学测量设备的国产化进程,其次建立螺纹连接数据库的行业共享机制,最后推动检测标准与数字孪生技术的深度融合。只有构建起覆盖全产业链的智能检测生态,才能为高端装备制造提供更强大的技术支撑。
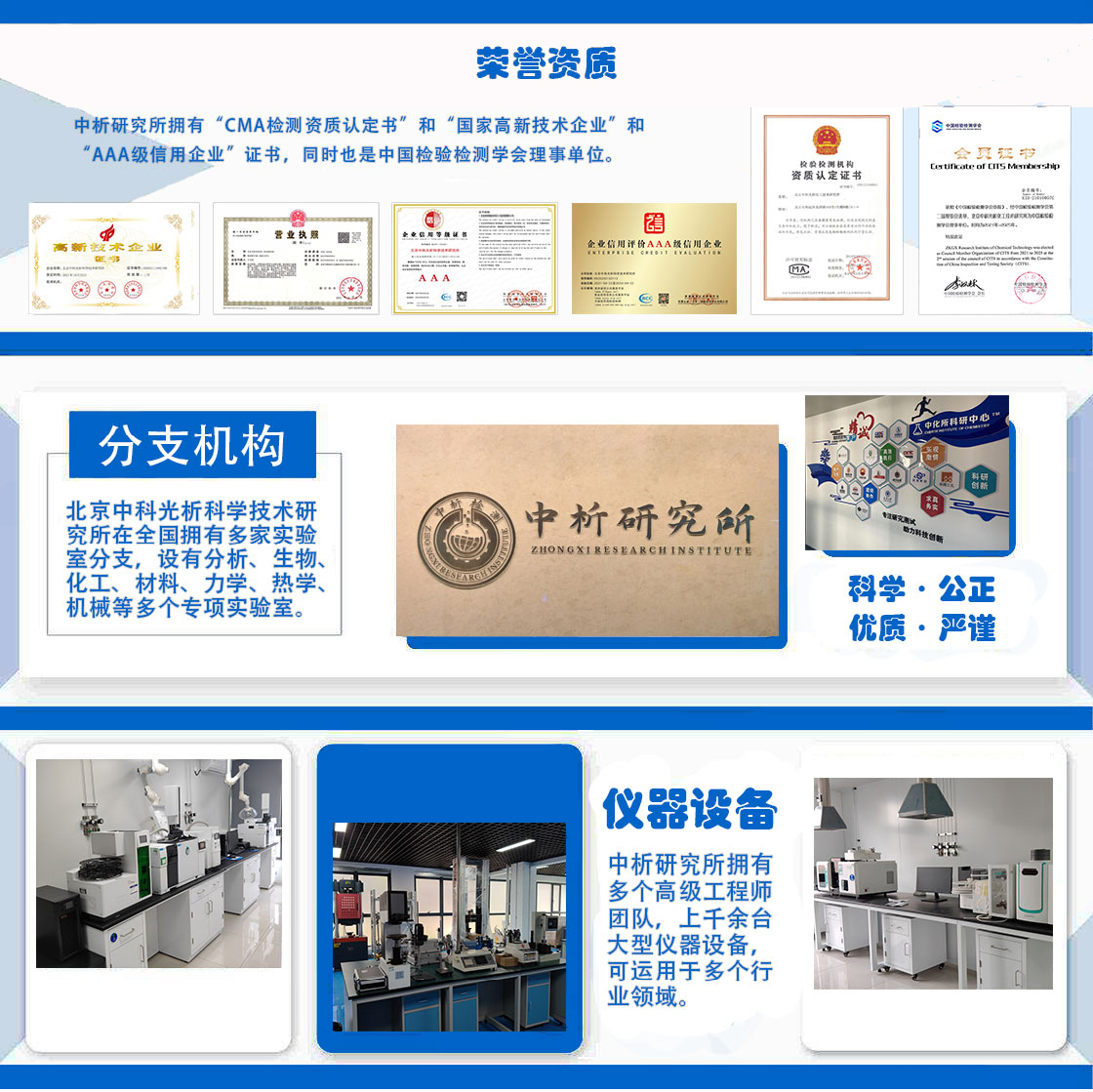
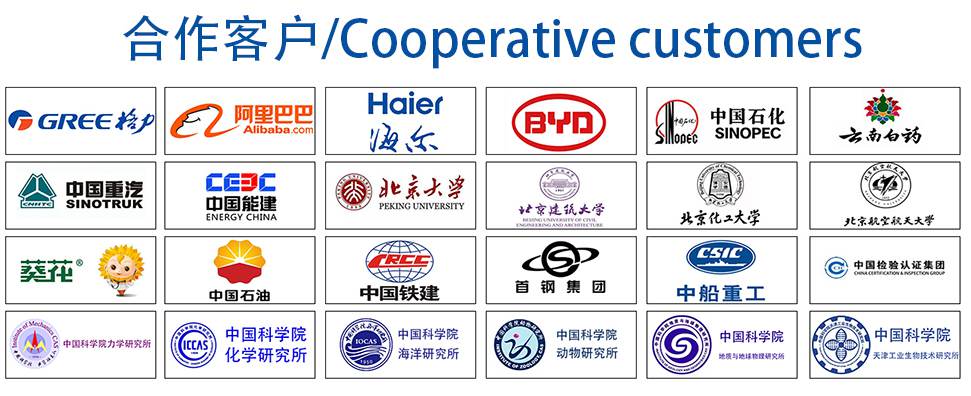