在海洋工程、石油化工、航空航天等高端制造领域,材料耐腐蚀性能直接影响装备服役寿命与安全可靠性。据中国腐蚀与防护学会2024年数据显示,我国工业领域因腐蚀造成的年损失达2.1万亿元,相当于GDP总量的2.3%。耐腐蚀性能试验检测通过模拟极端环境下的材料失效过程,构建从实验室数据到工程应用的转化桥梁,其核心价值体现在三个方面:为设备选型提供量化依据、优化防腐涂层设计参数、建立全生命周期腐蚀数据库。特别是在海上风电桩基阴极保护系统评估、核电站冷却管路完整性监测等场景中,精准的腐蚀检测可降低30%以上的非计划停机风险。
## 技术原理与测试方法电化学与模拟环境复合检测体系
现代耐腐蚀检测采用多尺度分析方法,结合电化学工作站与气候模拟箱实现全维度评价。电化学阻抗谱(EIS)技术通过测量材料表面双电层电容变化,可解析钝化膜生长动力学(据美国材料试验协会ASTM G59标准)。加速腐蚀试验箱则通过调控温度(35±2℃)、盐雾沉降率(1.5ml/80cm²·h)等参数,精准复现海洋大气、工业酸雨等典型腐蚀环境。值得注意的是,针对深海高压环境开发的"阶梯式加压腐蚀测试系统",可在720小时内完成相当于自然环境下10年的腐蚀进程模拟。
## 标准化实施流程全链条质量管控体系
检测流程严格遵循ISO 17025实验室管理体系,包含五大关键环节:试样预处理(依据GB/T 10125进行表面脱脂)、环境参数标定(采用NIST溯源传感器)、过程数据采集(每15分钟记录开路电位)、失效特征分析(应用SEM/EDS微观表征)以及腐蚀等级判定(参照ASTM G31累计失重法)。在输油管道焊缝腐蚀检测案例中,该体系成功识别出Cr-Mo钢在H₂S环境中的应力腐蚀开裂倾向,为工艺改进提供关键数据支撑。
## 行业应用实践典型场景解决方案
在新能源电池壳体制程中,检测机构通过组合"循环盐雾-湿热-紫外线老化"试验(参照SAE J2334标准),将铝合金壳体耐蚀寿命从行业平均的8年提升至12年。某海洋工程集团运用"实海挂片+电化学噪声监测"双验证模式,使跨海大桥钢筋腐蚀速率预测误差从±25%降至±8%。而针对氢能储运设备的特殊需求,开发的高压氢环境应力腐蚀试验平台(压力范围15-100MPa),已纳入TSG 23-2021特种设备安全技术规范。
## 质量保障与技术创新数字化检测系统构建
通过建立实验室信息管理系统(LIMS),实现检测数据的区块链存证与AI趋势分析。中国船级社2023年认证数据显示,采用机器视觉的自动腐蚀评级系统使判定效率提升40%,误判率低于1.5%。同时,基于数字孪生的虚拟腐蚀试验技术,可在产品设计阶段预测10种以上介质的腐蚀交互作用,将研发周期缩短60%。值得关注的是,新型微区扫描电化学工作站可实现50μm级局部腐蚀的原位监测,为异种金属连接件提供纳米尺度防护方案。
## 发展展望与建议随着极端环境装备需求增长,耐腐蚀检测技术将向多场耦合、原位动态监测方向发展。建议行业重点攻关三方面:开发适用于超临界CO₂环境的腐蚀预测模型、建立覆盖"材料-结构-环境"的数字化孪生数据库、制定氢脆与腐蚀协同作用评价标准。政府层面需加大公共检测平台建设投入,企业应推进腐蚀大数据与智能运维系统融合应用,最终构建覆盖设计、制造、服役全过程的腐蚀防护生态体系。
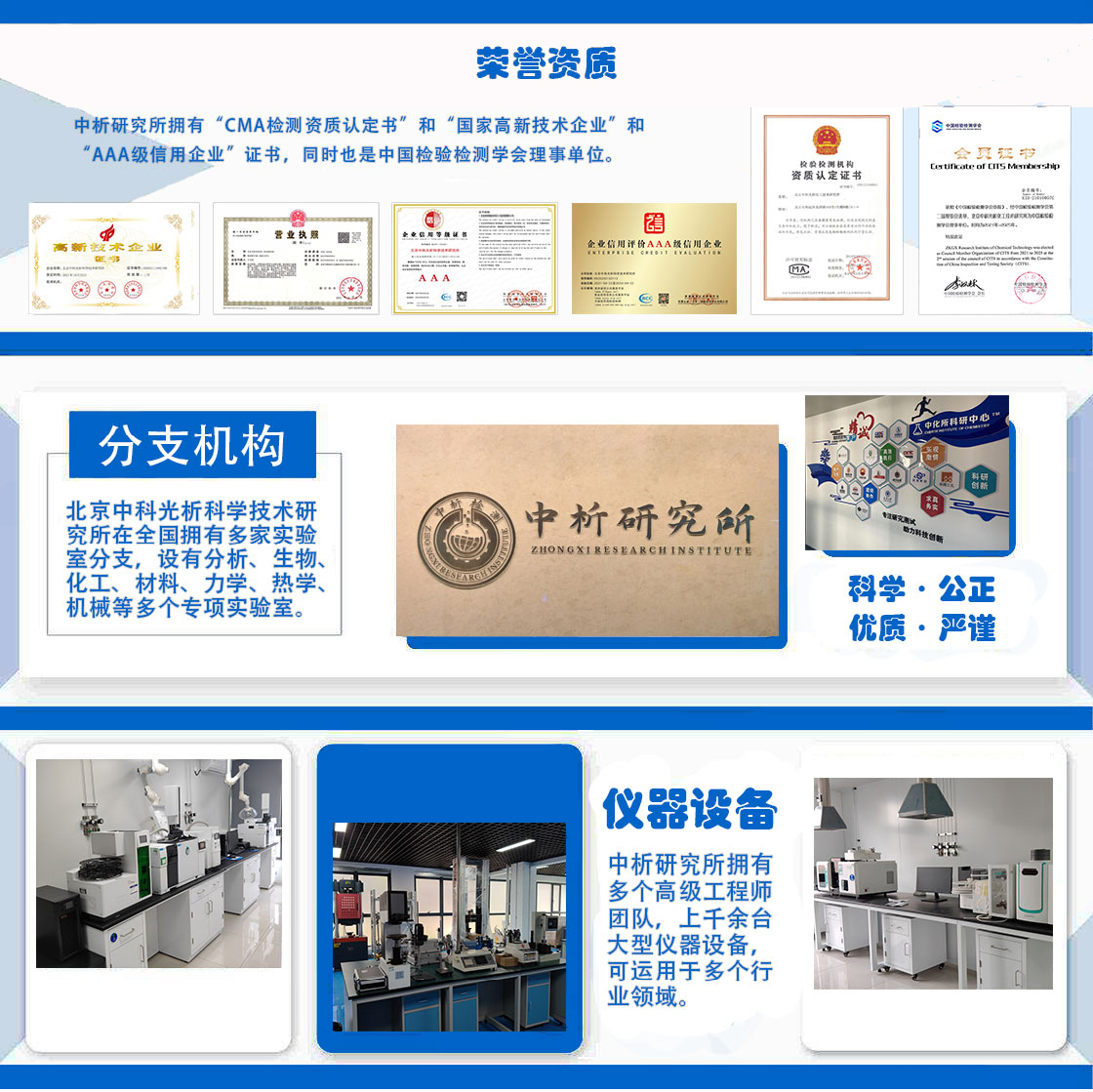
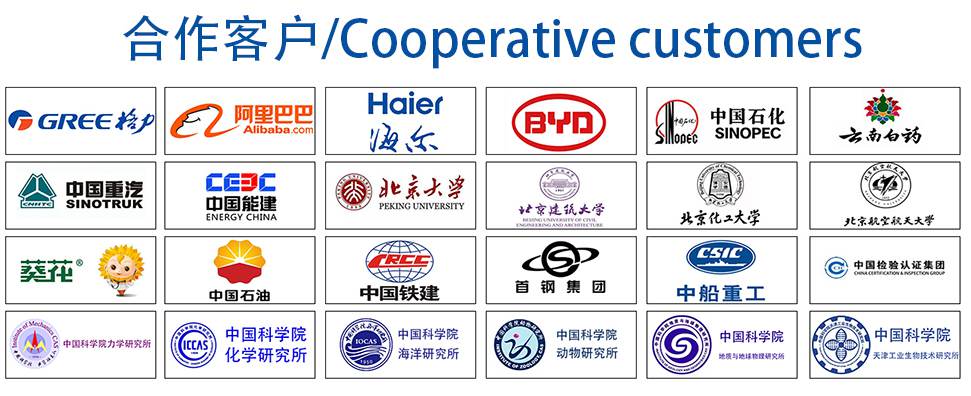